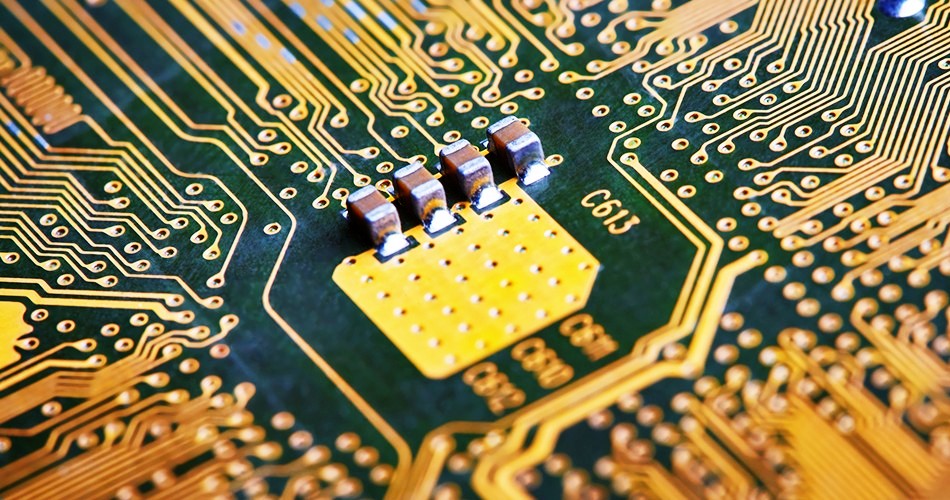
The latest PCBA electronic processing plant PCB new product trial production process in 2022
1、 Process preparation:
1. Reference drawings: The Process Department shall count the reference drawings and relevant information of the trial production project.
2. Process Output Document: determines whether all process output documents have been issued.
Process output documents include:
BOM files: circuit board BOM, bare metal BOM, packaging BOM, accessory (product) BOM, etc.
PCBA support worker: PCB splicing drawing: PCB processing requirements (length, width, thickness, splicing method, etc.) sent to the PCB factory
Steel mesh fabrication document: steel mesh PCB patch diagram for veneer fabrication required for external processing of SMT: provide veneer size and configuration description
PCBA welding operation instructions: requirements for welding and processing of circuit boards for outsourced workers.
Inspection documents: finished product inspection procedures and delivery inspection reports.
Commissioning instructions: including chip program burning, circuit board program burning, electrical parameter testing, and function testing.
Assembly operation instructions: including process flow, production configuration table, instructions for each station (welding, assembly, verification, network configuration, etc. prepared according to the station based on the production configuration table).
Packaging operation instructions: guide how to package and verify products.
Aging operation instruction: It is important to guide the aging process, including core aging, whole machine aging and aging records.
Equipment operation instructions: equipment safety operation procedures.
2、 Internal process review:
1. Process document review: review whether there are defects. What needs to be improved.
2. Internal review of the prototype of the first board: review whether the circuit board and the prototype have design risks and unreasonable designs.
3. Fixture review: review fixture design, approval cycle and internal procedures.
4. Understand the outsourcing processing of PCBA, and confirm whether it affects the subsequent assembly and commissioning. If necessary, it shall be reported at the trial production preparation meeting and the handling measures shall be determined.
The minutes of the pre trial production process review meeting shall be sent by email.
3、 Contents confirmed in trial production preparation meeting
1. Specify the trial production target.
2. Determine the nature of trial production:
The nature of trial production includes:
Customer requirements/new models
Change supplier
Design change/project trial
Routine experiment
Engineering Experiment
Add mold/engineering trial
other
3. Refer to drawings, BOMs and process documents: the Process Department will hold a pre trial production process review meeting internally after the completion of the process documents to integrate information and report it at the trial production preparation meeting.
4. Confirmation of completeness of materials --- the Planning Department shall report the completeness of materials. It includes information such as shortage report and arrival date after production material preparation.
5. IQC incoming material inspection: the data content includes the problem points of the defective problems, the judgment results, and the judge. (It is convenient to verify the acceptance of defective products and determine the impact on product assembly during later assembly).
6. Tooling and equipment allocation --- The Production Department evaluates the satisfaction according to the production allocation table.
7. Personnel allocation --- the Production Department shall evaluate the satisfaction according to the production allocation table.
8. Work division of project members for trial production: the process cooperates with hardware to provide technical support for debugging and testing. Process collaboration structure provides assembly technology support.
9. Trial production plan: make a trial production plan according to the time confirmed at the trial production preparation meeting, and send it to each project member by email. The trial production plan includes personnel training time: deployment time of the Production Department (before formal trial production)
Trial production start time: the production department determines the trial production time according to the schedule
First article inspection time (QA estimate)
Total trial production time (PE estimate)
Trial production summary meeting time (PE estimate)
At the trial production preparation meeting, the Sign in Form shall be filled in and<<minutes of trial production preparation meeting>>shall be issued after the meeting. For the corresponding problems, the planned completion time and actual completion time shall be determined for the uncompleted tracking items, and the completion progress shall be tracked for the corresponding responsible person. A notice shall be issued one day before the trial production to explain the reasons for the delay and the planned completion time. The Production Department shall re determine the trial production time according to the planned completion time.
4、 Personnel training meeting
1. Product introduction and preliminary understanding of this trial production product
2. Understanding of various parts of the product
3. Explanation of process documents (process flow, configuration, key stations and precautions, inspection points, safety matters)
4. Description and demonstration of sample assembly process.
Fill in<<Product Trial Production Training (Description) Record Form>>during training.
5、 First article of trial production product
1. During the trial production, the project leader, R&D engineer, process engineer and quality engineer will guide the production on site.
2. First piece quantity: 5 monitors; 10 handheld products, 10 finger clip products and 10 accessory products respectively.
3. First article inspection: the production department shall fill in the first article inspection report and submit it to the quality department for inspection.
4. The Quality Department shall conduct all tests on the first product at the first time and reply to the test results,
5. Relevant technicians shall conduct the first article review at the trial production site according to the first article inspection results to confirm whether the subsequent batch trial production can be carried out (trial production continues or is suspended)
6、 Batch trial production shall be carried out after the first article is passed
1. Production data statistics in the trial production process: The production department truthfully counts the defective ratio of materials and the defective ratio of each test procedure, and timely reports the material situation. Provide all data to the process engineer every day. According to the data provided by the production, the process engineer counts the assembly, testing and other problems in the entire production process.
2. The process shall analyze and classify the statistical data, and propose solutions through consultation with relevant personnel.
3. At the end of the trial production every day, a summary meeting will be held on site, and the improvement plan for the next day will be formulated for the defects of the day. The Production Department and the Quality Control Department are the main information data providers in the trial production stage, and the Process Department is the information data summary and analysis party.
4. In the process of trial production, the process line shall be arranged, the production line shall be optimized, the working hours shall be recorded and the production capacity shall be counted.
5. During trial production, the Production Department shall record the following forms
5.1 Chip burning: If the chip needs to be burned before the outsourcing of PCB board, fill in<<Chip burning program record form. xls>>.
5.2 Debugging: The<<Dynamic Concern Rate Table>>shall be filled in during debugging. The purpose is to determine the production capacity, check the defective ratio, and determine the key defective points, so as to facilitate process improvement and defect analysis and handling. After debugging, repair the defective products and fill in the<<PCB test defect record>>.
5.3 Assembly: fill in<<Dynamic Concern Rate Table>>respectively in the stages of semi-finished products, finished products, data upload and network configuration. Fill in<<maintenance record>>during maintenance. For the reworked machines inspected, the<<maintenance record>>shall also be filled in.
5.4 Materials: Production records of material loss of trial production models<<Material Defect Statistics>><< The Material Defect Statistics Table>>includes picking quantity, usage quantity, incoming material defect quantity and production loss. The operator of the docking material station shall fill in the<<Material Defect Record Form>>, and the Production Department shall fill in the<<Material Defect Statistics Form>>after statistics.
5.5 Inspection: QC shall make statistics and summary on the total number, defective rate, problem points, working hours and personnel of trial production inspection.
Note: For batch trial production of accessories, it is only necessary to fill in the Statistical Table of Accessory Product Process Quality.
6. The process department shall show the form before the "trial production summary meeting":
6.1 Record of problems during trial production: record problems found during trial production
The contents shall be classified and recorded according to functional problems, structural problems, poor incoming materials, production and assembly problems, and the handling measures in trial production and post processing measures shall be recorded.
6.2 Trial production process record: summarize the production capacity and defective rate in trial production according to the<<Dynamic worry rate table>>in the production record. The time of temporary shutdown during trial production shall be recorded.
6.3 Maintenance record form: summarize the key defects according to the maintenance records recorded in the commissioning and assembly stages of production, and feed back to the relevant departments for control and improvement.
6.4. Loss rate: make statistics according to the production record and determine the loss rate, control the production loss and feed back the defective incoming materials to the supplier through IQC.
7、 Internal process review
1. Review of process documents: review documents are missing and need to be improved. Attention should be paid in the future:
1.1 Reference drawings: For the reference drawings and relevant information of the trial production project, each department of the factory shall propose whether to update and update the requirements, and the Process Department shall track the update progress.
1.2 Process output document: determine whether the process output document needs to be updated and its contents.
1.3 Understand the outsourcing processing of PCBA, and confirm the problems and improvement of PCBA. The pending and other needs shall be reported at the trial production summary meeting, and the handling measures shall be agreed. The minutes of the process review meeting after trial production shall be sent by email.
1.4 The process department shall summarize PCBA outsourcing processing problems. The pending and other needs shall be reported at the trial production summary meeting, and solutions shall be agreed for rectification. And issue<<minutes of trial production review meeting>>after the meeting
2. Clamping apparatus review: review the effect of the use of the clamping apparatus and the areas that need to be improved in the future.
3. Trial production overall review: review problems encountered in the trial production process and good solutions, and exchange trial production experience.
The minutes of the process review meeting after trial production shall be sent by email.
8、 Process summary
1. Production overview: Briefly introduce the operation time, number of people and equipment used in each stage of trial production.
2. Material condition: whether the production material preparation and planning requirements are met, whether there are defective incoming materials, temporary measures for defective incoming materials and long-term treatment measures. See<<Material Defect Statistics>>
2.1 Production of PCB and PCBA
2.2 PCB splicing and PCB processing.
2.3. Problems such as poor welding, handling and design exposed in the external support workers of circuit boards.
2.4 How to control the welding quality of circuit board external support workers to ensure it (personnel and relevant inspection equipment).
2.5 For problems in incoming inspection and commissioning of circuit boards, please refer to<<Bad Test Record of Circuit Boards>>
It shows whether the debugging environment is satisfied, whether the incoming materials of devices are poor, and whether the welding and design are poor.
3. Product assembly
3.1 According to the product process flow, feed back the treatment measures and post treatment measures for the functional problems, structural problems, poor incoming materials, production and assembly problems in the trial production process and the problems mentioned above. Refer to<<Problem record in trial production process>>and<<Maintenance record in assembly stage>>.
3.2 Special instructions shall be given to key engineering stations, such as high-temperature aging, high-voltage, leakage current detection, data upload, network configuration, bare metal inspection, packaging, etc.
3.3 Analyze the process of each station according to the process flow: possible legacy, and propose solutions.
4. Process documents
4.1 Describe the completion of process documents before trial production and the update of process documents after trial production.
4.2 Process flow evaluation and process bottleneck description.
5. Tooling and equipment
Description of tooling and equipment in trial production, performance and effect verification of new tooling and equipment, etc.
6. Opinions and suggestions on improving product design process
Briefly list the problems exposed by the design. In order to improve the product process level, some reasonable suggestions can be added to avoid remaining hidden dangers.
7. Process summary conclusion
Evaluate the capacity (see<<Trial Production Process Record>>), process rationality, and equipment processing capacity, and evaluate the expected effect of good improvement of the opinions and suggestions on process. Then give the conclusion of the process department on this trial production
9、 Hold trial production summary meeting after trial production
1. After the trial production, the Process Department shall organize the project team members to hold a "trial production summary meeting" to negotiate long-term solutions for the problems in the<<trial production process problem record>>. After the meeting, the long-term solutions negotiated will be verified by classification, including functional design problems, structural design problems and assembly problems, which will be verified by the process, and incoming material problems will be jointly verified by the process and IQC.
2. Gather the problems encountered by various departments of the factory, negotiate with the project team members for solutions, and rectify according to the negotiated solutions after the meeting. Lay a good foundation for later mass production.
3. Update of reference drawings, BOMs and process documents: the Process Department will hold a post trial production process review meeting internally after the trial production is completed, integrate it and report it at the trial production preparation meeting.
10、 Circuit board trial production summary report
After the "Trial Production Summary Meeting", the Process Department shall organize to fill in the Trial Production Summary Report and submit it to the Project Management Department. In the Trial Production Summary Report, the process director evaluates the process rationality, equipment processing capacity and capacity, and makes factory conclusions and suggestions for trial production. The trial production summary report of the Process Department is attached.