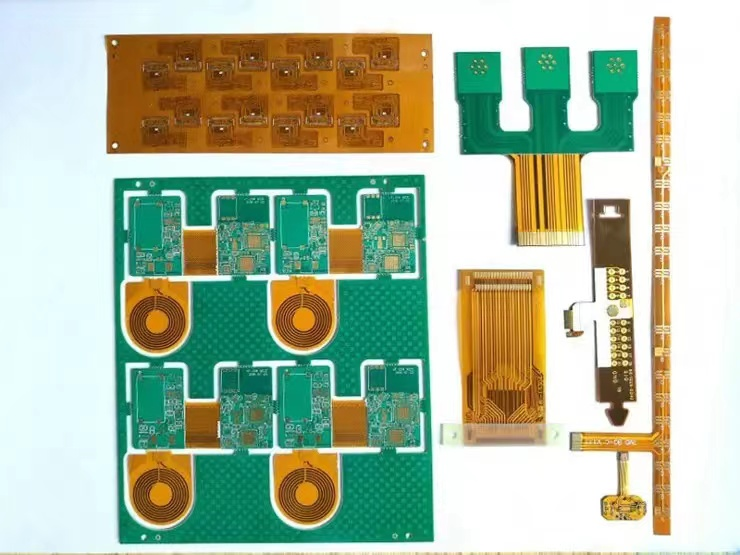
flexible PCBs offer versatility and other advantages over rigid circuit boards. However, for OEMs with tight budgets or looking to bring an affordable product to market, the benefits may not outweigh the costs.
flexible PCBs are ideal for medical devices, implants, sensors, and mobile consumer electronics because they are suitable for use where space and/or weight are limited. flexible PCBs are the preferred and recommended solution for products requiring:
l Suitable for wiring solutions that cannot be solved by rigid boards
l Lightweight and durable lightweight products
l Miniaturized version of existing technology
l 3D packaging geometry
l Small number of equipment interconnections
l Anti-shock and vibration
flexible PCBs help reduce the size and weight of applications. Ideal for high temperature and high density applications.
High temperature and high density applications
flexible PCBs are preferred by engineers for industrial and manufacturing applications because they are small and durable, can withstand high temperatures, and are resistant to chemicals, radiation, and UV light. flexible PCBs are typically made of polyimide or similar polymers, which dissipate heat better than the materials used to construct rigid circuit boards. Variations in polyimide or polymers allow flexible PCBs to be placed in products that experience extreme conditions without negatively impacting the product's performance. For example, industrial sensor technology.
Will flex circuits replace rigid circuit boards in all applications?
No, although flexible circuit boards are useful and can be used in a range of applications, they do not replace rigid circuit boards.
For manufacturers, the costs associated with the efficiency of implementing proprietary flex circuit board designs in consumer products can be high, which directly affects consumers. rigid circuit boards are less expensive to manufacture and install (when using standard automated high-volume manufacturing equipment).
Most innovative products incorporate flex circuits when necessary, and where possible use robust and reliable rigid circuit boards to reduce manufacturing and assembly costs.
Some manufacturers use hybrid rigid-flex PCBs that are connected to each other by ribbon flex circuits for product manufacturers. By focusing on the individual strengths of each board underlying technology, rigid-flex boards can be compounded and engineered to meet a variety of engineering needs. These boards are commonly used in the manufacture of medical devices and other high reliability products.
It is strongly recommended that you consult a PCB and PCBA service provider before starting a project to ensure that you are effectively utilizing the provider's capabilities.