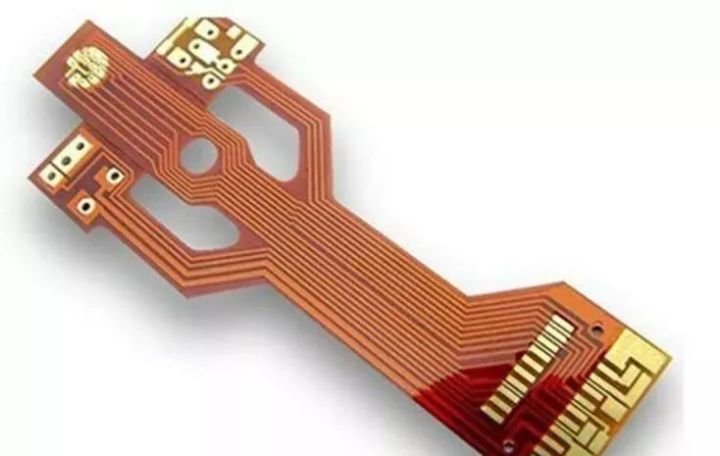
Three main characteristics of Flexible circuit board
Today we will introduce the three main characteristics of flexible circuit board:
1. Flexibility and reliability of flexible circuit board
At present, there are four types of FPC: single-sided, double-sided, multi-layer flexible board and rigid-flex board.
①Single-sided flexible board is a printed board with the lowest cost and low electrical performance requirements. When single-sided wiring, a single-sided flexible board should be used.It has a layer of chemically etched conductive patterns, and the conductive pattern layer on the surface of the flexible insulating substrate is rolled copper foil. The insulating substrate can be polyimide, polyethylene terephthalate, aramid and polyvinyl chloride.
②The double-sided flexible board is a conductive pattern made by etching on both sides of the insulating base film. The metallized hole connects the patterns on both sides of the insulating material to form a conductive path to meet the flexible design and use function. The cover film protects single and double-sided conductors and indicates where the components are placed.
③Multi-layer flexible board is to laminate 3 or more layers of single-sided or double-sided flexible circuits together, form metallized holes by drilling and electroplating, and form conductive paths between different layers. In this way, no complicated welding process is required. Multilayer circuits have huge functional differences in higher reliability, better thermal conductivity, and easier assembly performance. When designing the layout, the interaction of assembly size, number of layers and flexibility should be considered.
④ Traditional rigid-flex boards are composed of rigid and flexible substrates selectively laminated together. The structure is compact, and the conductive connection is formed by metallization. If a printed board has components on the front and back, rigid-flex boards are a good choice. But if all the components are on one side, it is more economical to use a double-sided flexible board with a layer of FR4 reinforcement laminated on the back.
⑤ The flexible circuit of the hybrid structure is a multi-layer board, and the conductive layer is composed of different metals. An 8-layer board uses FR-4 as the inner dielectric and polyimide as the outer dielectric, with leads extending from the main board in three different directions, each made of a different metal. Constantan alloy, copper and gold are used as independent leads. This kind of hybrid structure is mostly used in low temperature situations where the relationship between electrical signal conversion and heat conversion and electrical performance is relatively harsh. price-performance ratio.
2. The economy of FPC flexible circuit board
If the PCB design is relatively simple, the total volume is not large, and the space is suitable, most of the traditional interconnection methods are much cheaper. If the circuit is complex, handles many signals or has special electrical or mechanical performance requirements, a flexible circuit is a better design choice. Flexible assembly is most economical when the size and performance of the application exceeds the capabilities of rigid circuits. A 1mil pad with a 5mil through hole and a 3mil line and space flex circuit can be fabricated on a single film. Therefore, it is more reliable to mount the chip directly on the film. Because it does not contain flame retardants that may be a source of ionic contamination.
These films may be protective and cure at higher temperatures, resulting in higher glass transition temperatures. The reason for the cost savings of flexible materials over rigid materials is the elimination of connectors. The high cost of raw materials is the main reason for the high price of flexible circuits. The price of raw materials varies greatly. The cost of raw materials used in polyester flexible circuits with the lowest cost is 1.5 times that of rigid circuits; high-performance polyimide flexible circuits are as high as 4 times or more. At the same time, the flexibility of the material makes it difficult to automate processing during the manufacturing process, resulting in lower yields; defects in the final assembly process, including peeling off flexible attachments, line breaks. This type of situation is more likely to happen when the design is not suitable for the application. Under high stresses caused by bending or forming, it is often necessary to select reinforcing or reinforcing materials. Although the cost of raw materials is high and the manufacturing is troublesome, the foldable, bendable and multi-layer paneling functions will reduce the size of the overall assembly, and the materials used will be reduced, so that the total assembly cost will be reduced.
The flexible circuit industry is in a small but rapid development. The polymer thick film method is an efficient and low-cost production process. The process selectively screen prints conductive polymer inks on inexpensive flexible substrates. Its representative flexible substrate is PET. Polymer thick film conductors include screen-printed metal fillers or carbon powder fillers. The polymer thick film method is inherently clean, uses lead-free SMT adhesives, and does not require etching. Because of the addition process and the low cost of the substrate, the polymer thick film circuit is 1/10 of the price of the copper polyimide film circuit; it is 1/2 to 1/3 of the price of the rigid circuit board. The polymer thick film method is especially suitable for the control panel of the device. On mobile phones and other portable products, the polymer thick film method is suitable for converting components, switches and lighting devices on printed circuit boards into polymer thick film circuits. Save costs and reduce energy consumption.
Generally speaking, flexible circuits are indeed more expensive and more expensive than rigid circuits. In the manufacture of flexible boards, many cases have to face the fact that many parameters are out of tolerance. The difficulty in making flexible circuits is the flexibility of the material.
3. The cost of FPC flexible circuit board
Despite the above-mentioned cost factors, the price of flexible assemblies is falling, becoming close to that of traditional rigid circuits. The main reasons for this are the introduction of newer materials, improved production processes and altered structures. The current structure makes the product more thermally stable, with very few material mismatches. Some newer materials allow for more precise lines due to thinner copper layers, making components lighter and more suitable for fitting into small spaces. In the past, copper foils were attached to adhesive-coated media using a rolling process. Today, copper foils can be produced directly on the media without the use of adhesives. These techniques can get several microns thick copper layer, get 3m. 1 Precision lines with even narrower widths. The flexible circuit has flame retardant properties after some adhesives have been removed. This both speeds up the uL certification process and further reduces costs. Flexible circuit board solder masks and other surface coatings further reduce the cost of flexible assembly.
In the coming years, flexible PCB that are smaller, more complex and more expensive to assemble will require newer methods of assembly and the addition of hybrid flexible circuits. The challenge for the flexible circuit industry is to take advantage of its technology to keep pace with computing, telecommunication, consumer demand and dynamic markets. In addition, flexible circuits will play an important role in the lead-free movement.