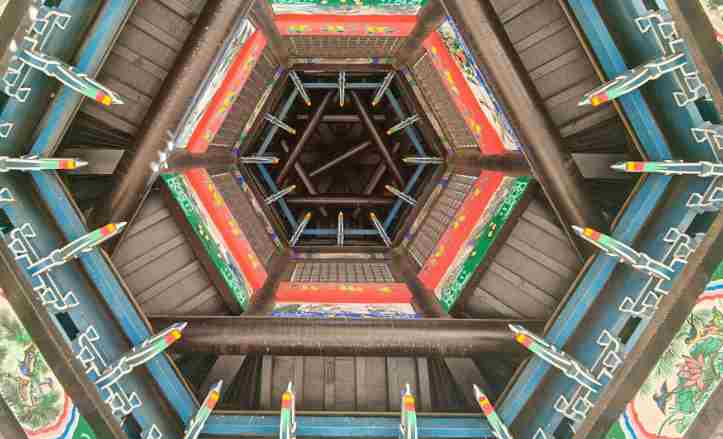
1. How to deal with PCB sensitive circuit
(1) Power cord
According to the size of the printed circuit board current, try to thicken the width of the power line to reduce the loop resistance. In particular, attention should be paid to the power supply direction of the power cord and ground wire, which is opposite to the transmission direction of data and signals, that is, the power supply mode promoted from the end stage to the forward stage, which helps to enhance the anti-noise ability.
(2) Ground wire
The design principle is) digital and analog separately. If the circuit board contains both logical and linear circuits, keep them as separate as possible. Low frequency circuit should be as far as possible to use a single point of parallel grounding, the actual wiring difficulties can be partially connected after the parallel grounding. High frequency circuit should adopt multi-point series grounding, ground should be short and rented, high frequency components around as far as possible with a large area of grid foil. The ground cable should be as thick as possible. If the grounding wire is very flexible line, the grounding potential changes with the change of current, so that the noise resistance performance is reduced. The ground wire should therefore be thickened so that it can pass through three times the allowable current on the printed board. If possible, the ground cable should be at least 2 mm to 3mm. The ground wire forms a closed loop. For printed boards composed only of digital circuits, the ground circuit is arranged into a group loop, which can improve the noise resistance.
2. What interference elements are in PCB
A source is a component, device, or signal that generates interference. It is described in mathematical terms as follows: du/dt, where the di/dt is large, the interference source. Such as: lightning, relay, thyristor, motor, high frequency clock can become the source of interference. Propagation path refers to the path or medium through which interference is transmitted from the interference source to the sensitive device. The typical interference transmission path is conduction through wire and radiation in space. Sensitive components are objects that are easily interfered with. Such as: A/D, D/A converter, MCU, digital IC, weak signal amplifier.
3, can be divided into radiation and conduction interference
Radiation interference is the interference source uses space as a medium to interfere its signal to another electrical network. Conduction interference is to use conductive medium as a medium to interfere with signals on one electrical network to another electrical network. In the design of high-speed system, integrated circuit pins, high frequency signal lines and all kinds of plugs are common sources of radiation interference in PCB board design. The electromagnetic wave they emit is electromagnetic interference (EMI), which will affect the normal work of themselves and other systems. Bioneng belongs to Qinji Group, is the leading electronic industry service platform in China, providing online components, sensor procurement, PCB customization, BOM, material selection and other electronic industry supply chain solutions, one-stop to meet the comprehensive needs of small and medium-sized customers in the electronics industry.
4. How to deal with sensitive components in PCB
The placement of components should conform to production and maintenance convenience. The capacitor polarity should be consistent. Heating components and sensitive components should be placed away from each other. Moisture-sensitive components tend to be packaged in tape-and-reel systems, each with a large number of components. When compared with the pin components in the IC tray, the key issue is longer exposure to moisture. Exposure time must be increased to dry storage time during setup and treatment.
Compared with the microstrip, the ground coplanar waveguide has a larger ground area because it not only has ground ground on the bottom surface of the medium, but also distributes ground ground on both sides of the signal transmission line at the top of the medium. Coplanar waveguides achieve electrical stability by using ground to surround signal lines.
The transmission modes of microstrip and ground coplanar waveguide circuits are quasi-transverse electromagnetic mode (quasi-TEM). Due to the enhanced grounding structure of the ground coplanar waveguide circuit, its machining is more complicated to some extent. Compared with the microstrip, the ground coplanar waveguide circuit has the characteristic of low dispersion, and the radiation loss of the ground coplanar waveguide circuit is lower than that of the microstrip circuit when the frequency rises to the millimeter wave band.
Grounded coplanar waveguide circuits have a wider effective bandwidth and a wider impedance range than microstrip circuits due to the enhanced grounding structure. However, the microstrip circuit structure is relatively robust, and its simple bottom-to-ground circuit structure is easy to process. In addition, microstrip circuit performance is not sensitive to circuit machining factors, and the circuit performance is less affected by conductor/gap etching difference and conductor thickness difference.
And the RF circuit layout those sharp corners are specially designed to compensate for the transmission line corners
When a transmission line is required to bend (change direction) due to wiring constraints, the bend radius used should be at least 3 times the width of the intermediate conductor. In other words:
Bending radius ≥ 3 × (line width).
This minimizes the characteristic impedance change of the corner.
If gradual bending is not possible, the transmission line can be bent at right angles (not curves), as shown below. However, this must be compensated for to reduce the impedance mutation caused by the increase in the local effective linewidth when passing through the bend point.