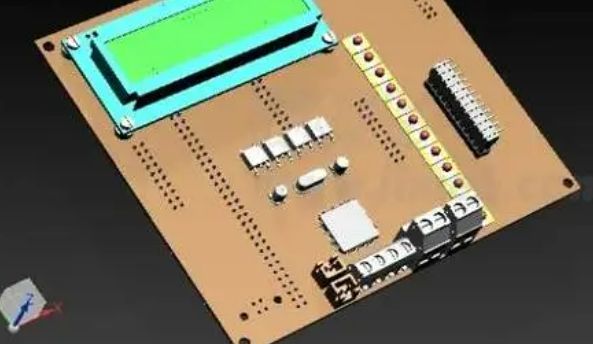
PCB circuit opening and short circuit are the problems encountered by PCB manufacturers almost every day, which has been troubling the production and quality management personnel, resulting in insufficient shipment quantity and replenishment, affecting on-time delivery and leading to customer complaints, which is a difficult problem for people in the industry to solve.
The reasons for the above phenomenon and the improvement methods are listed as follows:
A, open circuit caused by exposing the substrate
1. There is scratch phenomenon before the copper clad plate enters the warehouse;
2. The copper clad plate is scratched in the process of opening;
3. The copper clad plate is scratched when drilling;
4. The copper clad plate is scratched in the transfer process;
5. When stacking plates after copper sinking, copper foil on the surface is injured due to improper operation;
6. The copper foil on the surface of the production plate is scratched when it passes the horizontal machine;
Improvement method:
1. IQC must carry out spot inspection before entering the warehouse to check whether the surface of the copper clad plate is scratched and exposed to the substrate. If so, contact the supplier in time and make appropriate treatment according to the actual situation.
2. The copper clad plate is scratched in the process of opening, the main reason is that there are hard objects on the surface of the opening machine. Friction between the copper clad plate and the objects causes the copper foil scratch to form the phenomenon of exposing the substrate.
3, after copper sinking, the whole board plating after stacking board due to improper operation was scratched: after copper sinking, the whole board plating after storage board, because the board is stacked together and then put down, the board has a certain number of weight is not light, and the board Angle down and with a gravitational acceleration, the formation of a strong impact impact on the board surface, causing the board surface scratches the substrate.
4, the production board is scratched when the horizontal machine: the baffle of the grinding machine sometimes comes into contact with the board surface, and the edge of the baffle is not smooth and the favorable objects are raised, and the board surface is scratched when the board is crossed; Stainless steel drive shaft, due to damage into a pointed object, when the plate scratches the copper surface and exposed substrate.
5, the copper clad plate is scratched when drilling, the main reason is that the main shaft clip is worn, or the clip inside the debris is not clean and clean, grasp the drill is not strong, the drill does not go to the top, than set the length of the drill, drilling height is not enough, the machine tool move when the drill tip scratch copper foil and form the phenomenon of dew substrate.
The clip can be replaced by the number of times recorded by the knife or according to the wear degree of the clip; Clean the clip regularly according to the operating procedures to ensure that there is no debris in the clip.
To sum up, for the copper after the scratch exposed substrate phenomenon, if on the line is in the form of open or line gap, easy to judge; If it is in the copper before the scratch exposed substrate, and on the line, after the copper sinking and sinking on a layer of copper, the thickness of the copper foil line is significantly reduced, the back open, short circuit test is difficult to detect, so that customers may be used because of too much current caused by the line burned off, the potential quality problems and the economic loss is quite large.
Two, no hole open circuit
1. No porosity of sunk copper;
2. There is oil in the hole causing no porosity;
3. No porosity caused by excessive micro-erosion;
4. No porosity caused by poor electroplating;
5, drilling hole burning or dust hole blocking caused by no holes;
Improvement measures:
1. Sunk copper without porosity:
A. No porosity caused by the pore-filling agent: it is due to the imbalance or failure of the chemical concentration of the pore-filling agent. The function of the pore-filling agent is to adjust the electrical property of the insulating substrate on the pore wall, so as to facilitate the subsequent adsorption of palladium ions and ensure the complete coverage of chemical copper. If the chemical concentration of the pore-filling agent is unbalanced or failure, no porosity will be caused.
b, activator: the main components are pd, organic acid, stannous ion and chloride. In order to deposit palladium uniformly on the pore wall, all parameters must be controlled to meet the requirements. Take the activator we are using as an example: the temperature is controlled at 35-44℃, and the low temperature leads to insufficient density of palladium deposition, resulting in incomplete chemical copper coating. The temperature is too high because the reaction is too fast, the material cost increases. Concentration colorimetric control is 80%--100%, if the concentration is low, resulting in insufficient density of palladium deposition, chemical copper covering is not complete; The concentration is too high because the reaction is too fast, the material cost increases.
c. Accelerant: The main component is organic acid, which is used to remove stannous and chloride ion compounds adsorbed by pore wall and expose catalytic metal palladium for subsequent reaction. The chemical concentration of the accelerant we use now is controlled at 0.35-0.50N. If the concentration is too high, palladium will be removed, resulting in incomplete chemical copper covering. If the concentration is low, the removal of stannous and chloride ions adsorbed by the pore wall is not effective, resulting in incomplete chemical copper coating.
2. There is wet film oil remaining in the hole causing no porosity:
a. When printing wet film, print a plate and scrape the bottom of the screen once to ensure that there is no pile of oil at the bottom of the screen. Under normal circumstances, there will be no residual wet film oil in the hole.
b, screen printing wet film is used 68-77T screen version, if the wrong screen version, such as ≤51T, the hole may leak into the wet film oil, the development of the oil in the hole may not be clean, electroplating will not be plated on the metal layer and cause no porosity. If the mesh is high, it is possible that because of insufficient ink thickness, the anti-coating film is broken by the current when electroplating, resulting in many metal points between the circuit and even short circuit.