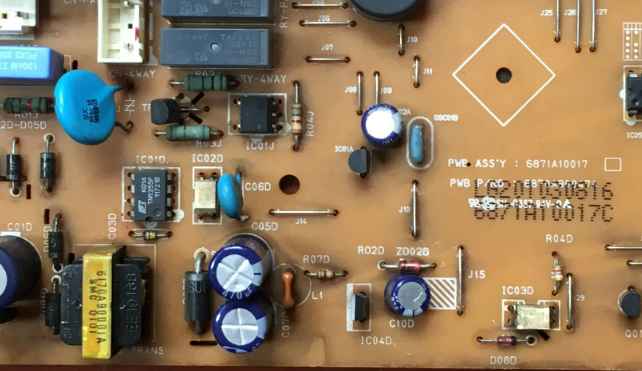
Table 1. Example of four-layer laminated design
In general, for more complex high-speed circuits, it is better not to use four layers, because it has several unstable factors, both physical and electrical characteristics. If you must do a four-layer board design, you can consider setting it as: power - signal - signal - ground. There is also a better scheme: the outer two layers of the ground, the inner two layers of the power and signal lines. This scheme is the best laminated scheme for the four-layer board design, which has excellent EMI inhibition effect and is also very beneficial for reducing the impedance of signal lines. However, the wiring space is small in this way, and it is difficult for the board with high wiring density.
Six layer board design
Now many circuit boards are using six-layer board technology, such as the design of memory module PCB, most of them use six-layer board (high-capacity memory modules may use 10-layer board). The most conventional six-layer lamination is arranged as follows: signal - ground - signal - signal - power - signal. From the point of view of impedance control, this arrangement is reasonable, but because the power supply is far from the ground plane, the radiation effect of small common mode EMI is not very good. If the copper coating area is placed in layer 3 and layer 4, it will cause poor signal impedance control and strong differential mode EMI problems. There is also a scheme to add a ground plane layer, the layout is: signal - ground - signal - power - ground - signal, so that both from the impedance control and from the EMI reduction point of view, the need for high-speed signal integrity design environment. However, the disadvantage is that the stacking of layers is unbalanced. The third layer is the signal wiring layer, but the corresponding fourth layer is the power layer with a large area of copper, which may encounter some problems in PCB manufacturing. In the design, copper can be applied to all the blank areas of the third layer to achieve the effect of approximately balanced structure.
Table 2 Example of six-layer laminated design
Manufacturing, assembly, testing, and logistics costs are important factors in any project, design, and cost control that uses a combination of soft and hard design techniques. Combined soft and hard designs often require mechanical teams to assist in the flexible design and PCB integration of the final product. The process is time-consuming, costly and error-prone.
To make matters worse, PCB design tools often ignore the folding and assembly problems of hard-soft combined designs. The combination of soft and hard design requires designers to think and work with 3D thinking. Flexible parts can be folded, twisted and rolled up to meet mechanical design requirements. However, traditional PCB design tools do not support 3D board design or bending and folding simulation of rigid design parts, or even the definition of different stack design parts, including flexible design parts.
Because of this, hard-soft designers are forced to manually convert the rigid and flexible parts of a 3D design into a flat, 2D production format. After that, the designer also needs to manually document the soft design area and carefully review the area to ensure that no components or holes are placed between rigid and flexible. This process is also hampered by many other rules, most of which are not supported by PCB design software.
In general, it takes more effort to design a combination of soft and hard PCB than a standard rigid PCB designed with traditional PCB software, which is at a weak position in the competition. Fortunately, modern design tools with advanced 3D capabilities can support the definition and simulation of bending in flexible design parts, as well as the definition of different design parts and different board stacks. These tools largely eliminate the reliance on mechanical CAD tools for flexible parts, saving designers and design teams time and money.
Through the use of modern PCB design tools, developers and board manufacturers coordinate in a timely manner to promote the combination of soft and hard technology to save time and efficiency. The combination of soft and hard design requires closer collaboration between designer and manufacturer than traditional rigid circuit board and cable design. The successful production of hardboard requires the designer and manufacturer to jointly develop design rules, including: the number of boards in the design, material selection, hole size, bonding mode and size control. With the right design tools in place, clear definitions and trade-offs can be made early in the design process to optimize the combination of soft and hard panels and further reduce overall costs.
There is no denying that current industry trends and consumer demands are pushing designers and design teams to push the envelope and develop new electronic products to meet market challenges. These challenges, especially the demands of today's mobile devices, have pushed the combination of soft and hard technology into the design mainstream and into higher commercial value in a wide range of applications, especially for projects that start with hundreds of sets. Modern PCB design tools support 3D product development, upfront collaboration and all the necessary definition and simulation of the combination of hard and soft, greatly reducing the annoyance of the combination of hard and soft design and making their solutions more attractive; In addition, it is cheaper than rigid cable-connected PCB designs. For the design team, different choices mean that the success or failure of the product is on the line.