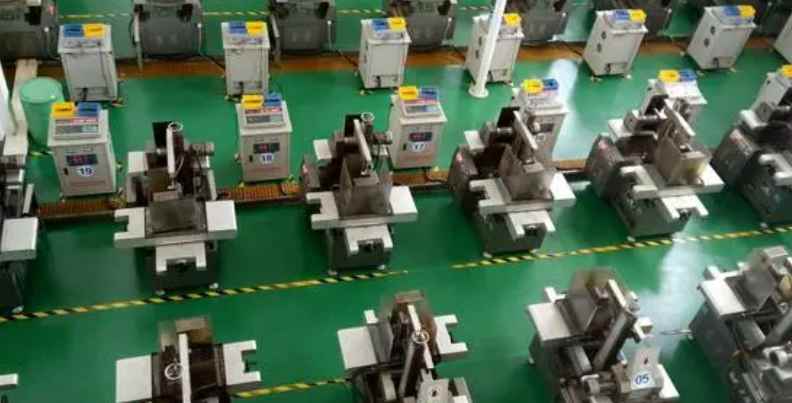
For high frequency products, because the component mounting process can alter the laminate resin system in the PCB and thus affect the results of the high frequency test, it is important to expose the material to any high temperature you will apply before conducting the final high frequency test. The solder joint itself is another very complex process that creates a connection between the surface of the circuit board and the surface of the component to form intermetallic compounds of different materials and different surface coatings while preventing oxidation. Looking at the whole process, there are a lot of things that can fail. Similarly, from leaded solder to lead-free solder, the actual mechanical properties of lead-free solder are not as satisfactory as those of leaded solder. There are so many different lead-free combinations on the market that it's kind of like baking a cake with a little bit of this and a little bit of that. All of these small amounts of material, as little as 1-2%, can improve the crystal structure of the solder so that there is less stress inside the solder when the solder joint is formed, which is what causes the product to fail in the field.
Johnson: I have a software background. What I want to know is how to model. This is a physics lab test.
Neves: Exactly. In our lab, we have a water-cooled return furnace with 13 zones, and we can use this return furnace to run circuit boards and samples, and other types of things. We have a HATS2 tester in our factory that can perform reflux simulation on samples in place of circuit boards while taking electronic measurements throughout the process to obtain data. When the sample is exposed to reflux temperatures, you can observe the resistance of the through-hole in the sample to check if the coating on the through-hole wall separates at high temperatures. Many times you will re-establish a strong electrical connection as the material cools and shrinks again to its normal size.
If the plating on the wall of the through-hole or microthrough-hole of the circuit board separates due to stress caused by the expansion of the material at high temperatures, you can see electrical disconnection at high temperatures. But when the PCB shrinks again during cooling, you end up with a mechanical connection that is electrically durable, and you may never see this coating separation again during cold testing. You only get a chance to see this problem when the reflux temperature is at its highest, when the through hole is physically separated by extreme expansion of the coating. You're starting to see this more with PCBS doing these reflux monitoring tests, and the reflux monitoring tests are starting to become a requirement on PCBS that people need to do this "electrical monitoring" reflux simulation. These are electrical tests that are done during the reflux simulation, and after that certain types of thermal shock planning are done to make sure that you get certain types of thermal cycles that illustrate the life acceleration that can be done for actual use.
Johnson: Can you explain what you meant earlier when you said that "figuring out reliability comes at a high price"?
Neves: Take cars for example. We do a lot of car testing in the lab. Most car customers have to deal with five or six different environments in which their product must work, such as a car. Different environments include inside the car, on the engine, in the engine bay, transmission sensors, brake sensors, etc., even if they are all in the same car, they are in very different environments, under different mechanical pressures. What happens to your transmission sensor processing is very different from the air-conditioning electronics or stereo system in your car. It's easier to model worst-case life and use that model everywhere (for example, durability), but that means you're spending a lot of money on parts that don't require that level of reliability, parts that are used elsewhere in the car that don't require that level of reliability to reach life expectancy.
If the parts of the brake system I buy for my car are certified at 200°C, the stereo system made from them will be very expensive. It doesn't make economic sense to use these parts everywhere in the car. Be cost conscious and understand exactly what level of reliability is required for different locations in the car. This will limit the cost of putting the product into actual use.
Automakers have spent a lot of time and money modeling different environments in order to figure out which parts they must keep working reliably over the multi-decade life cycle of a car. They take this model, they compress the impact of environmental changes over decades into 30-45 days of peer testing, and they can say, "I know if I take this model, I'm doing a Weibull correlation on the data, I'm taking one or two decades of data out of the data to see how long my product is going to work in the real world. If it can go through this kind of simulated accelerated testing, I know it will work for ten or twenty years in the real world."
They've done this in a variety of environments on the car. When you limit a product to a certain area of the vehicle, there is a specific set of reliability requirements associated with that area, depending on the final use environment. Parts need to withstand a certain number of cycles and a specific temperature or type of environment. To understand all the different operating environments of an entire vehicle, they try to understand real-world applications and build models to speed up the test environment. It took them years to make these accelerated models. Because these models have been built over many years at a cost of millions of dollars, this is a very important asset. For startups like Tesla, their approach does not evolve directly from other manufacturers or tier 1 suppliers. They did not use the procurement model used by most established carmakers, buying components from tier one suppliers. These Tier 1 suppliers have decades of experience in the automotive sector, and given that they are ultimately financially responsible for reliability, they do a lot of work in modeling.