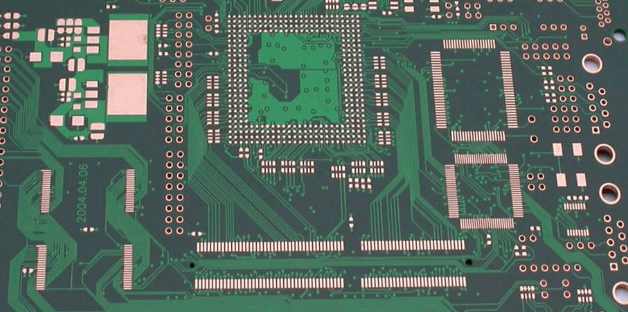
Matties: Part of the question is under what conditions are they going to test reliability, for example, when producing prototype products, but will the yield be different in mass production? How did you overcome this problem?
Neves: Let's say that whatever happens, you're going to do reliability testing on your product, and the changes you're making aren't going to change much. This rarely happens with different batches, different runs, and different batches of PCBS. It takes hundreds of processes to make a PCB, and that many processes can lead to a lot of changes.
Accept this fact, and a reliability test becomes a competency test. "I have the ability to make the product reliable, but I don't know if over time it will be as reliable with customers as it was when I built it." I do reliability testing, and then I say, "I have the ability to make this product reliable. I need to monitor the changes that may occur as I build the product and make sure they don't affect the level of reliability that I have built up." I need to know what changes affect reliability. I can perform certain reliability tests with the lowest or highest standards, so I can understand how "if the problem is on the circuit board or on the component or on the solder joint, it will deviate from my reliability test results."
Matties: In general, products may be pre-produced by different manufacturers, rather than being manufactured where they end up being mass-produced.
Neves: In today's manufacturing environment, every component on a circuit board is assembled this way: you have different manufacturers. You buy different materials from different sources. You'll also run into all the questions related to the reliability of the source material. Make sure you're getting what you really want, not a defective or counterfeit product. You need to focus on getting the product you want. Then, there is usually a change when the product is processed, or when you switch from one component supplier to another. In your first large, long-term test, you need to monitor various issues to ensure that reliability does not change
Matties: Do you see defects recurring over and over again?
Neves: When you start looking at material changes, the more complex the component, the more likely it is to fail. When you look at a resistor or capacitor, you will see that each resistor or capacitor usually has to go through less than 50 processes to get to the finished product. Because these components themselves don't have many variables that can go wrong, their chances of failure are dramatically reduced compared to many of the processes required to make PCBS. It's easy for the manufacturer to control the variables, and there's a good quality system in place to monitor those fewer processes very well, to make sure that they're consistently producing the same product.
Now if you look at transformers or PCBS or other components, these are products that require hundreds of processes to be made, and you're going to have problems with how these processes interact with each other, and it's going to be very difficult for the manufacturer to figure out why the processes are changing. Changes naturally permeate the process through the interaction between processes and ultimately affect the reliability of the product in practical use.
Johnson: In your test preparation, you mentioned "welding simulation". What is welding simulation?
Neves: When we start putting components into the holes in the PCB, we usually do a dip weld test. We take a sample that represents a PCB, dip it into a large pot of solder, and transfer heat to the PCB sample. This heat is similar to all the heat used in assembling a PCB, and is the same as what you see in a wave soldering operation. At present, the welding techniques used to assemble circuit boards mainly include convection air reflow welding and manual welding for maintenance, or some other special welding that cannot be handled by air reflow welding. At the user site, at least on the PCB side, we have a variety of tests to put the board through a simulated reflux process. These simulations try to get the same surface temperature on a circuit board that has been exposed to the worst conditions many times for the longest time with various components, and in this way grasp the limits of what the finished product can withstand. However, there are many times when you reflow the circuit board, and then you rework or repair the circuit board. The mounting process for analog components typically consists of four to six harsh reflux exposures. This is very common in the electronics industry. Some people run the boards through the worst reflux process four to six times. To understand the most extreme damage that can occur during the reflux process while manufacturing circuit boards, you should try to simulate the same type of damage and pressure on your sample in a preconditioning simulation before conducting reliability tests.
Because the finished product needs to be used under the worst conditions, the components it uses need to be exposed to high temperatures multiple times for as long as possible. Therefore, these simulations attempt to obtain the surface temperature of the board that is the same as the component under these conditions.
This applies not only to the interconnection and isolation of circuit boards, but also to the high frequency testing of circuit boards, because the material will change its electrical characteristics after undergoing the component welding process. Most current materials have a relatively high glass transition temperature (Tg) and can be processed lead-free, but these materials are not homogeneous materials and are mixed with a variety of different resins and additives. Even if your material has a Tg rating of 180°C, it is not composed of a resin system of Tg180°C. If they made a material like this, it would be brittle and crack easily.
You'll run into all sorts of other problems. You have a Tg of 130-140s, or 160s resin mixture, and you mix it into this amazing set of resins, and it becomes a resin matrix of high Tg material. High component welding temperature, especially lead-free welding temperature, has a considerable effect on the low Tg resin in the material matrix, and can change the dielectric constant (Dk) and consumption factor (Df) of PCB materials. Repeated exposure to high temperatures will alter the matrix of the resin. When the substrate in the resin system starts to break down your Dk and Df, your impedance changes as this happens.