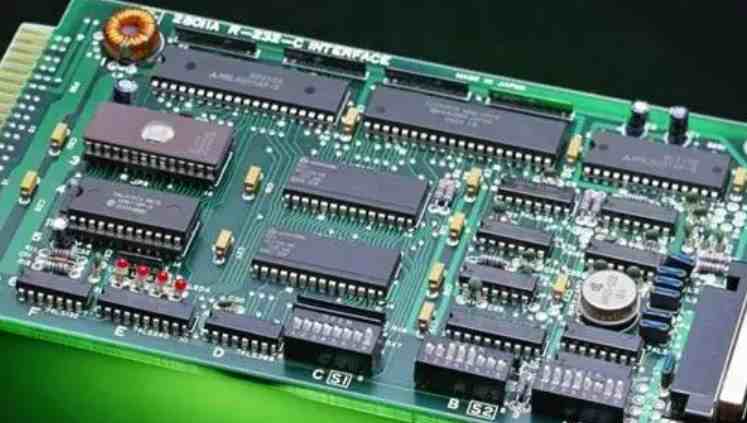
In order to ensure the quality of finished PCB products, reliability and adaptability tests are required. The temperature resistance test of PCB circuit boards is to prevent adverse reactions such as board bursting, foaming and delamination at excessively high temperature, leading to poor product quality or direct scrap, which is a problem that needs to be paid attention to. So PCB circuit board temperature resistance is how much, how to do heat resistance test?
The temperature problem of PCB circuit board is related to the temperature of its raw materials, solder paste and surface parts. Usually, the highest temperature resistance of PCB circuit board is 300 degrees, 5-10 seconds; Over lead-free wave soldering temperature is about 260, over lead is about 240 degrees.
PCB circuit board heat resistance test:
1, first prepare PCB circuit board production board, tin furnace.
Sample 5 pieces of 10*10cm base plate (or pressed plate, finished plate); "(Copper-containing substrate without foaming stratification).
Substrate: more than 10cycle; Pressing plate: LOWCTE15010cycle above; HTg material more than 10cycle;
Normal material at least 5 cycles.
Finished plate: more than LOWCTE1505cycle; HTg material more than 5cycle; Normal material at least 3 cycles.
2. Set the temperature of tin furnace at 288+/-5 degrees, and adopt contact temperature measurement and correction;
3, soak with a soft brush for flux, apply to the board face, reoccupy crucible 煹 pliers buccal test board into tin stove, timing out 10 SEC after cooling to room temperature, visual presence of foaming board appear, this is 1 cycle;
4. If the problem of bubbling and bursting plate is found visually, immediately stop leaching tin and analyze the initiation point f/m. If there is no problem, continue the cycle until the bursting plate, with 20 times as the end point;
5. It is necessary to slice and analyze the bubbling place, understand the source of detonation point, and take pictures.
The above content is about the temperature resistance of PCB circuit boards, I believe we all understand. PCB circuit boards will produce some bad problems in the overheating temperature, so for different materials of PCB circuit boards, the temperature resistance, need to be understood in detail, do not exceed its maximum limit temperature, so as to avoid PCB circuit boards scrap, increase the cost.
Circuit board baking time and temperature should be how much
Before SMT plant on-line, need to bake the circuit board. If the circuit board is properly vacuum packed, it can be assembled without baking. If it has been placed for a period of time, it is recommended to bake for about 40-60 minutes at 120-130°c, which may be the appropriate temperature and time, but it must also depend on the metal surface treatment condition, some treatment is not suitable for baking.
The IPC does not have such rules because there are too many changes in products, materials and so on to make rules. 120-130°C is set because the water volatilization temperature is 100 °C, and 40-60 minutes is set because of previous experience that the water content of FR4 material can be reduced to a very low and stable value under such conditions.
General Circuit board assembly if you can add baking, should be able to reduce the residual water and explosion risk. But because the current circuit board metal treatment method is diversified, some treatment is not suitable for baking, so no one will stipulate that must bake. Moreover, most circuit board factories hope not to bake on the circuit board assembly, so you can save trouble. But it must be noted that if it is soft sheet material easy to absorb water, it is best to bake. In addition, even if the package is good, if standing in a non-dry environment for a long time, it is best to bake and then assemble otherwise easy to cause problems. However, it should be baked as long as it is unsealed. The material characteristics and environmental factors are too influential to set standards.
Assuming the use of silver or organic welding film for metal treatment, it is difficult to require baking before assembly, because baking does have the opportunity to destroy the copper surface protection affecting the solderability of the circuit board, the above for your reference.
What is the significance of copper layer on PCB design
In the process of PCB design, some engineers in order to save time do not want to carry out the table bottom whole board copper. Is this the right thing to do? Is copper layer necessary for PCB?
First of all, we need to be clear: the bottom layer of copper is good and necessary for PCB, but the whole board copper must comply with some conditions.
The bottom of the table full plate paving copper benefits
1. From the perspective of EMC, the whole board at the bottom of the table is covered with copper, which provides extra shielding protection and noise suppression for the inner signal and the inner signal. At the same time, it also provides some shielding protection for the underlying devices and signals.
2. From the perspective of heat dissipation, since the current PCB board is more and more high-density, the BGA main chip needs to consider the heat problem more and more. The whole board copper floor improves the heat dissipation capacity of PCB board.
3. From the perspective of process analysis, the whole board is laid with copper, so that the PCB board is evenly distributed, and the PCB board can avoid bending and warping when the PCB is processed and pressed. At the same time, the PCB warping deformation caused by the different stress caused by the PCB over-reflow welding caused by the copper foil imbalance can be avoided.
Reminder: For two layers of plate, copper coating is very necessary
On the one hand, since there is no complete reference plane for the two layers, the floor can provide a return path and can also be used as a coplanar reference to achieve the purpose of impedance control. We can generally lay the ground plane at the bottom, and put the main devices and power lines and signal lines on the top. For high impedance circuit, analog circuit (analog to digital conversion circuit, switching mode power supply conversion circuit), copper coating is a good practice.
Conditions for laying copper on the bottom of the table
While the bottom layer of copper is good for PCBS, there are some conditions that need to be followed:
1, shop at the same time as far as possible manual shop, do not cover all at once, avoid broken copper, appropriate in the copper area to add holes to the ground plane.
Reason: The surface coppered plane will be fragmented by the surface components and signal wires. If there is poorly grounded copper foil (especially the thin long broken copper), it will become an antenna, resulting in EMI problems.
2. Consider especially the thermal balance of small devices, such as 0402 0603 and other small packages, to avoid the presence of monument effect.
Reason: If the whole plate is covered with copper and the pin of the component is fully connected, the heat will be lost too fast, resulting in difficulties in diswelding and repairing welding.
3. The whole slab paving is the best continuous paving, and the distance from the paving to the signal needs to be controlled to avoid the impedance discontinuity of the transmission line.
Reason: Copper sheets that are too close to each other when paving the floor will change the impedance of the microstrip transmission line, and discontinuous copper sheets will also cause negative impact on the impedance discontinuity of the transmission line.
4. Some special cases depend on the application scenario. PCB design does not appear absolute design, should be combined with various theories to weigh and use.
Reason: in addition to sensitive signals need to cover the ground, if the high-speed signal lines and components are more, a lot of small and long broken copper, and the wiring channel is nervous, need to try to avoid surface copper through the hole and ground plane connection, this time the surface can choose not to spread copper.