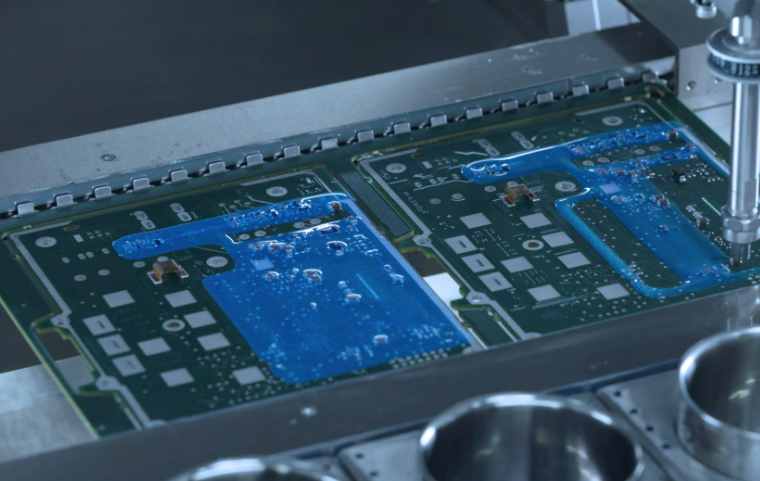
PCB ink quality is excellent, in principle can not be separated from the combination of the above major components. Ink quality is excellent, is the formula of science, advanced and environmental protection of the comprehensive embodiment. It is reflected in:
viscosity
It is a short name for dynamicviscosity. The viscosity is generally expressed in terms of the shear stress of the fluid flow divided by the velocity gradient in the direction of the flow layer in international units of Pa/s (Pa). S) or millipa/second (mPa. S). In PCB production, it refers to the fluidity of ink driven by external forces.
Conversion relationship of viscosity unit:
1Pa. S=10P=1000mPa. S=1000CP=10dpa.s
Refers to the ink deformation by external force, still maintain its properties before deformation. The plasticity of ink is beneficial to improve the printing accuracy;
thixotropic
Ink is gelatinous when standing, and is touched when the viscosity changes a property, also known as shaking, anti flow hanging;
liquidity
(leveling) ink under the action of external force, to the extent of development. Fluidity is the reciprocal of viscosity. Fluidity is related to the plasticity and thixotropy of ink. Plasticity and thixotropy is large, the fluidity is large; Large liquidity is easy to expand imprinting. Small liquidity, easy to appear net, produce ink phenomenon, also known as mesh;
viscoelasticity
Refers to the ink in the scraping board after printing, the shear fracture of the ink quickly rebound performance. It requires fast ink deformation and quick ink rebound to be conducive to printing;
dryness
Required ink on the screen drying as slowly as possible, and hope that the ink transfer to the substrate, the faster the better;
fineness
Pigment and solid particle size, PCB ink is generally less than 10μm, the size of the fineness should be less than one third of the mesh opening;
Drawing property
When the ink spatula is used to stir up ink, the degree of silk - like ink stretching without breaking is called wire drawing. Long ink wire, there are many filaments in the ink surface and printing surface, so that the substrate and printing plate stained, or even unable to print;
Transparency and covering power of ink
For PCB ink, according to the use and requirements of different ink transparency and hiding power also put forward a variety of requirements. Generally speaking, line ink, conductive ink and character ink, are required to have a high hiding power. The solder choke is more flexible.
Chemical resistance of ink
PCB ink according to the use of different purposes, the corresponding requirements of acid, alkali, salt and solvent requirements have strict standards;
Physical properties of ink
PCB ink must meet external scratch resistance, heat shock resistance, resistance to mechanical stripping, and meet various strict electrical performance requirements;
Ink safety and environmental protection
PCB ink requirements have low toxicity, odorless, safety and environmental protection.
Above we summarized the basic performance of twelve PCB inks, and in the actual operation of screen printing, and the operator is closely related to the viscosity problem. The viscosity of the silk screen printing is appropriate or not, has a great relationship. Therefore, in PCB ink technical documents and QC reports, the viscosity is clearly marked, indicating under what conditions, what type of viscosity testing equipment is used. In the actual printing process, if the ink viscosity is high, it will cause difficulty in leakage, and the graphic edge is serrated seriously. In order to improve the printing effect, diluent will be added to make the viscosity meet the requirements. However, it is not difficult to find that in many cases, in order to obtain the ideal resolution (image resolution), no matter what viscosity you use, it will not be possible to achieve. Why? After in-depth study, it was found that ink viscosity is an important factor, but not the only one. There is another quite important factor - thixotropy. It is also affecting the printing accuracy.
PCB and external device interconnection
We can now assume that we have solved all the signal management problems on the board and on the interconnection of discrete components. So how do you solve the signal input/output problem from the circuit board to the wire connecting the remote device? Coaxial cable technology innovator Trompeter Electronics is working on solving this problem and has made some significant progress (Figure 3). Also, look at the electromagnetic field given in Figure 4. In this case, we manage the conversion from microstrip to coaxial cable. In coaxial cables, the ground layers are ring-interwoven and evenly spaced. In the microzone, the ground layer is below the active line. This introduces some edge effects that need to be understood, predicted, and taken into account during design. Of course, this mismatch can also lead to losses and must be minimized to avoid noise and signal interference.
The management of impedance problems in circuit boards is not a negligible design problem. The impedance starts at the surface of the circuit board, then passes through a solder joint to the joint, and finally ends at the coaxial cable. Since impedance varies with frequency, the higher the frequency, the more difficult impedance management is. The problem of using higher frequencies to transmit signals over broadband appears to be the main problem facing the design.