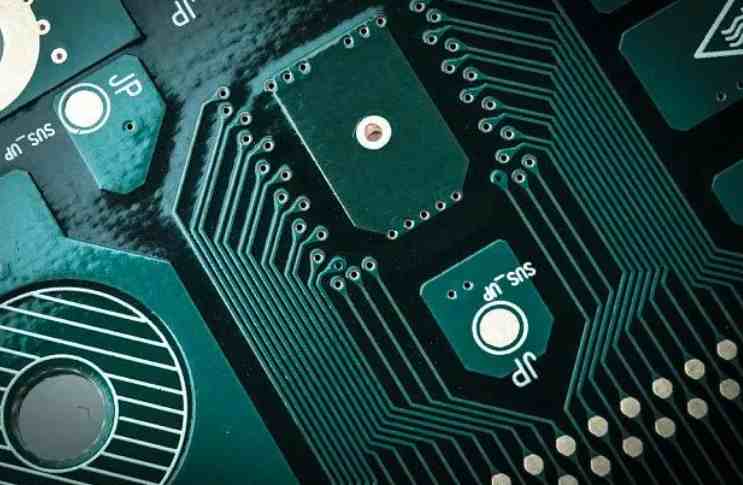
As our enterprise electronic information management technology level continues to improve the development of innovative ability, product iteration update is fast, automation, intelligent product quality problems become increasingly popular. The functional design requirements of electronic products are higher and higher, but students' requirements for volume are smaller and smaller. This requires the IC chip size to be smaller and smaller, the degree of complexity and enterprises continue to study through increasing, a kind of students to learn China's advanced high-density packaging technology - BGA patch packaging technology innovation ability to achieve rapid social and economic development. However, BGA is a headache for manufacturers. If you do not pay attention to the production and processing, you need to return to the factory for maintenance. So is there any better welding BGA patch method during SMT patch processing? The following hundred thousand into a small series to explain in detail to you!
BGA patch welding principle:
When the solder temperature reaches above the melting point, the oxide layer on the copper surface is cleaned by activating the flux. At the same time, the copper surface and the metal particles in the solder are capable of achieving a sufficient degree of activation. The molten solder wets onto the surface of the pad, and as described before, the surface of the pad copper is cleaned with flux. Through diffusion reactions using analytical chemical techniques, metal compounds can be formed directly on the solder and pad surfaces. Through this series of changes and functions, the bga has been fixed in place on the PCB.
In order to understand the "zero defect" welding bga method, we need to understand the final assembly process. Patch assembly involves the following steps:
Solder paste printing → Solder paste testing system → chip installation → reflow welding → Automatic Optical Inspection (aoi)→ Automatic X-ray Inspection (X-ray) In order to optimize bga welding during chip installation, necessary measures need to be taken before and during welding. Therefore, the following will be discussed from two aspects: pre - welding and welding.
First, before welding
In order to fix the BGA patch component to the PCB bare board, the first thing we need to do ourselves is to keep both the BGA component and the bare board PCB in good condition at all times. After all, even the slightest defect, such as dampness, can affect the welding process of the parts and even cause the company's entire social product to be scrapped.
1. Circuit board
(1) Select a suitable surface treatment method for the printed circuit board to meet engineering and product requirements. The comparison of several common surface treatment methods needs to be particularly clear. For example, some products need to meet EU rohs requirements and then need to be treated lead-free. You can choose from lead-free spray tin, lead-free chemical nickel gold or lead-free chemical tin plating and then decide on the surface treatment method based on the advantages and disadvantages of each.
(2) Bare boards should be properly preserved and used. Circuit boards must be vacuum-packed with moisture-proof bags and humidity indicator cards. The humidity indicating card can conveniently and economically check whether the humidity is within a controllable range. The color of the card is used to show how much water is in the bag, and also to show how waterproof it is. Once the moisture content of the package is significantly above or equal to an indicated value, the corresponding circle will turn pink on its own.
(3) Exposed printed circuit boards need to be cleaned and baked. Baking helps prevent moisture in the circuit board from forming weld defects during welding. Generally through baking need to be analyzed at 110±10℃ for two hours. In addition, the surface of the printed circuit board can become covered with dust during movement and storage, so it needs to be cleaned before installation and welding. Our company uses ultrasonic cleaning machine, can thoroughly clean the exposed PCB and assembled PCB, to ensure its cleanliness. This can fully ensure the reliability of the circuit board.
2. BGA components
BGA patch as a moisture sensitive component, its storage environment should be kept constant temperature and dry. In the process of storage management development, operation technology researchers must strictly comply with the storage specifications and regulations of components to prevent the quality and safety of components products and services from being affected by China's social environment. In general, bga components need to be stored in a moisture-proof box at a temperature of 20 to 25 degrees Celsius and a relative humidity of 10%, which can be better saved with nitrogen.
Bga components need to be baked before welding, and the welding temperature should not exceed 125℃, because too high a temperature may cause changes in the metallographic structure. When the components go through reflow welding process, it is easy to separate the solder ball from the package, thus reducing the welding quality of SMT components. If the baking temperature is too low, the moisture will not be easily removed. Therefore, the baking temperature of bga element must be adjusted appropriately. In addition, the baked bga components need to cool for half an hour before entering the assembly line.
Two, welding
In practice, controlling reflow welding is not an easy task, so the temperature curve of reflow welding needs to be adjusted to obtain high quality bga.
1. In the preheating stage, PCB temperature rises steadily and the flux is awakened. Generally speaking, the temperature rise needs to be stable and continuous to prevent deformation of the circuit board after sudden temperature rise. The ideal heating rate should be controlled below 3℃\\u002Fs, 2℃\\u002Fs is very suitable. The time interval should be controlled between 60 and 90 seconds.
2. In the infiltrating stage, the flux is gradually evaporated. The temperature should be maintained between 150 and 180 degrees Celsius for 60 to 120 seconds so that the flux is completely non-volatile. The speed of temperature rise is constantly developing. We usually need to control the temperature at 0.3 to 0.5℃/S.
3. The temperature of the reflow phase exceeds the melting point of the solder, causing it to change from a solid to a liquid. At this stage, the temperature should be controlled above 183 degrees Celsius for 60 to 90 seconds. Too long or too short a time can lead to welding defects. Welding temperature should be controlled at 220 ± 10℃, about 10 to 20 seconds.
4. During the cooling system phase, the solder begins to learn to become solid so that the BGA patch assembly can be fixed to the board. Moreover, the temperature drop needs our enterprise development through internal control technology can not be too high, usually below 4℃/S. The ideal temperature drop is 3℃/S, too high temperature drop will affect the deformation of pcb, greatly improve the quality of BGA patch welding.