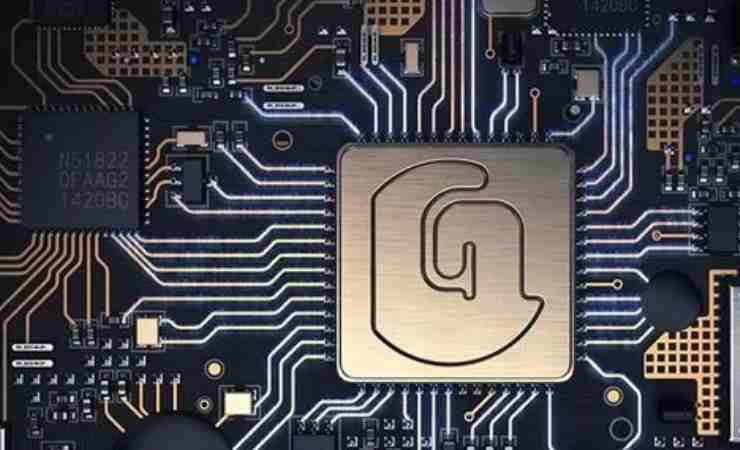
PCB is one of the important components of the electronic industry, the industrial output value accounts for about a quarter of the total output value of electronic components, the largest proportion in each electronic component subdivision industry, and flexible PCB board (FPC) is one of the fastest growing sub-industries in the PCB industry. From the development trend of various regions in the world, after large-scale restructuring, migration and technological upgrading, domestic PCB and FPC production and processing enterprises seize the opportunity of transferring electronic products to the domestic market, which further increases the proportion of domestic circuit board output value in the international market.
At the same time, the development of the circuit board industry, injet machine plays a decisive role in the production line. In order to prevent counterfeiting in the same industry and to effectively manage regional sales, manufacturers will use high-tech security means to identify their products. At this stage, the common use of ink inkjet machine, some problems continue to highlight: such as consumable consumption, high cost, the need for professional maintenance personnel, marking effect is easy to erase changes, high pollution problems.
Circuit board laser marking machine
With people's attention to environmental protection, laser marking is more and more prominent than the traditional inkjet marking advantages, laser marking can be processed serial number and two-dimensional code, to record the relevant production information, easy to trace the entire process of electronic products and quality control. In the PCB industry, laser labeling applications are showing a rapid growth trend.
The traditional coding methods of PCB circuit board are labeling or inkjet marking, which have many drawbacks in the process of processing.
Circuit board laser wipe machine
Circuit board laser wiping machine is a new type of circuit board cleaning equipment developed by Creative laser, replacing the traditional fiber bar wiping machine and eraser machine. Laser wiping machine output laser, and then through the ultra-high speed scanning mirror system to realize circuit board cleaning function, mainly used in the U disk circuit board, camera circuit board, card reader circuit board and other surface cleaning, circuit board conductive performance is stronger, better contact, better effect, and wipe board speed is 10 times the speed of traditional manual wipe board.
Sample of PCB circuit board laser wipe board
Disadvantages of traditional processing methods:
1, through chemical reagents to clean;
Clean with chemical reagents. This method has a certain pollution to the environment, but also exists after cleaning can not completely remove the moisture in the PCB matrix, resulting in the hidden danger of short circuit or leakage of products after the state.
2. Manually erase by hand;
Manual erasure using rubber blocks or fiber sticks. The disadvantage of this method is that the working intensity of workers is large, the enthusiasm is not high, the production efficiency is low, especially after cleaning PCB SMT, the cleaning quality is very unstable, and needs a lot of manpower.
3, through the wiping machine this automatic equipment to erase;
Erasing machine with circular rubber strip or fiber strip erasing method. This method is the use of electricity instead of human wiping board, greatly reducing the intensity of the work of workers; High production efficiency, compared with the workers using the force to wipe the plate operation mode, improve the production efficiency of more than 3 times; Different cleaning technical parameters can be selected according to different degrees of oxidation layer and fouling of PCB; With a circular rubber or fiber strip, electric wiping machine vertical high-speed rotation cleaning operation mode, to ensure the quality of cleaning.
Advantages of laser processing
1.WINDOWS2000 Chinese operation interface, easy to learn and understand;
2. Accurate CCD image visual instruction to achieve fast programming;
3. Any point, three-dimensional straight line, arc and other irregular lines or surface continuous wipe plate;
4. High speed, low noise speed DC brushless motor makes the wiping effect better;
5. Strong dust collecting device;
6 electrostatic eliminator can eliminate electrostatic within ±100V;
7. Wipe plate strength automatic compensation function, make the operation more convenient;
PCB aluminum substrate heat dissipation skills you know how much
1. Heat dissipation through PCB board itself: at present, PCB board is widely used in copper/epoxy glass cloth substrate or phenolic resin glass cloth substrate, and a small amount of paper-based copper coated plate. Although these substrates have excellent electrical properties and processing properties, but poor heat dissipation, as a heat dissipation way of high heating components, almost can not be expected from the PCB resin conduction heat, but from the surface of the components to the surrounding air heat dissipation. However, as electronic products have entered the era of component miniaturization, high-density installation and high thermal assembly, it is not enough to only rely on the surface of components with very small surface area to dissipate heat. At the same time, due to the large number of surface mounted components such as QFP, BGA, the heat generated by components to PCB board, therefore, the best way to solve the heat dissipation is to improve the heat dissipation capacity of PCB aluminum substrate in direct contact with the heating element, through the PCB board to conduct out or send out.
2. For equipment with free convection air cooling, it is best to arrange integrated circuits (or other devices) by length or by transverse length.
3. Use reasonable wire design to achieve heat dissipation: because the resin in the plate has poor thermal conductivity, and the copper foil line and hole are good conductors of heat, so improving the copper foil residual rate and increasing the heat conduction hole is the main means of heat dissipation.
4. High heating device with radiator, heat conduction plate: when the heat of a few components in PCB is larger (less than 3), can be added on the heating device radiator or heat conduction tube, when the temperature can not fall, can be used with a fan radiator, in order to enhance the heat dissipation effect. When the amount of heating devices is large (more than 3), you can use a large heat sink (plate), which is customized according to the position and height of the heating devices on the PCB board, or in a large flat radiator cut out different positions of the components. The radiator cover is fastened on the component surface as a whole, and contact with each component to dissipate heat. However, due to the low consistency of components during welding, the heat dissipation effect is not good. Soft thermal phase change pads are usually added on the surface of components to improve the heat dissipation effect.