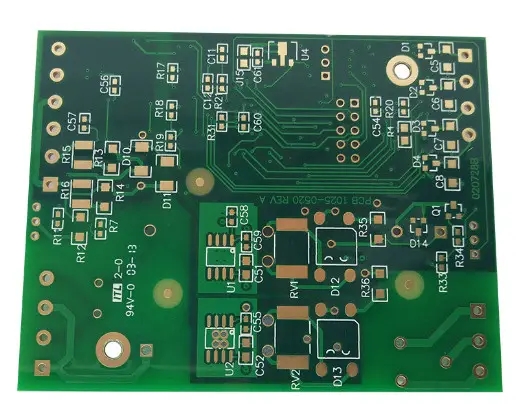
Circuit board factory: why high-frequency boards need to be tested
The circuit board manufacturer, circuit board designer and PCBA manufacturer explain to you why the Circuit board manufacturer should test high-frequency boards
printed circuit boards, also known as printed circuit boards, are providers of electrical connections for electronic components.
Printed circuit board is usually represented by "PCB", not "PCB".
PCB design is mainly layout design; The main advantage of using circuit board is to greatly reduce wiring and assembly errors, and improve the automation level and production labor rate.
High Frequency Circuit Board is a special circuit board with high electromagnetic frequency. Generally speaking, high frequency can be defined as the frequency above 1GHz. Its physical performance, accuracy and technical parameters are very high, and are commonly used in automotive anti-collision systems, satellite systems, radio systems and other fields.
The HF board factory basically sets test points to test whether the components on the HF board meet the specifications and weldability. For example, if you want to check whether there is a problem with the resistance on the circuit board, the simplest way is to use a multimeter to measure, and its two ends are known.
However, in the batch production of high frequency board factory, it is impossible to slowly measure the correctness of each resistor, capacitor, inductor and even IC circuit on each high frequency board with an instrument. Therefore, the so-called ICT (online testing) automatic testing machine appeared. It uses multiple probes (usually called nail beds) to contact all the parts on the plate that need to be measured at the same time, and then uses the sequence as the main sequence through program control. The properties of these electronic parts are measured in parallel. Generally, it only takes 1-2 minutes to complete all parts of the whole HF board, depending on the number of parts on the HF board. The longer the part, the longer the time.
However, if these probes are directly exposed to the electronic parts on the high-frequency plate or their welding feet, some electronic parts may be damaged. On the contrary, they are counterproductive, so there is a test point, which will result in another pair of dots at both ends of the part. There is no welding on it, which allows the test probe to contact these points without directly contacting the electronic components to be tested.
In the early days, the traditional plug-in (DIP) era was still on the high-frequency board. It does use the welding leg of the part as the test point, because the welding leg of the traditional part is strong enough to not be afraid of acupuncture, but the probe often contacts. Wrong judgment occurs. As common electronic parts eat tin through wave soldering or SMT, a residual flux film is usually formed on the surface of solder. The impedance of the film is very high, which often leads to poor contact of the probe. Therefore, it is often seen that the test operators of the production line often pick up the air spray gun and blow hard, or wipe these places with alcohol, which requires testing.
In fact, after the wave soldering test, the high-frequency plate still has the problem of poor contact of the probe. Later, after the prevalence of SMT, the situation of test misjudgment has been greatly improved, and the application of test points has also taken great responsibility, because SMT parts are usually fragile and cannot withstand the direct contact pressure of SMT. The use of test points can not directly contact the parts and their welding feet, and the probe is not allowed to protect the parts from damage. Moreover, because the misjudgment is reduced, the reliability of the test is also indirectly greatly improved.
The circuit board manufacturer, circuit board designer and PCBA manufacturer explain to you why the circuit board manufacturer explains why the high-frequency board needs to be tested.