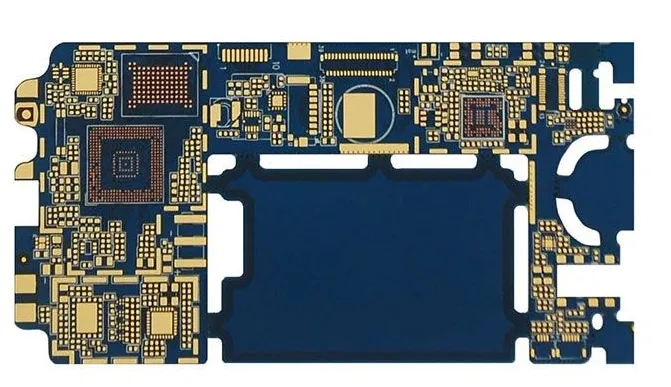
Remove the three proofing paint during the rework of PCBA
The three proofing paint protects the electronic assembly from moisture, dust, chemicals and high temperature in the operating environment where the electronic assembly is finally used. When we have to remove or replace the element due to on-site failure or manufacturing defects, the coating of the covered element must be removed first, and then the element can be removed and replaced. The correct method must be selected to remove this coating to avoid damaging PCB or adjacent components.
During rework, if the coating on the bottom of the component is not completely removed, the pad may be torn from the circuit board when the component is removed. If the coating is not completely peeled off, it may mean that the soldering tin may "spray out" from the package during reflow during the rework process, thus causing a short circuit. These problems, as well as other problems, may be caused by improper stripping of the three proofing paint.
There are many ways to remove the three proofing paint on the electronic assembly. The method and material used to remove the coating are determined according to the type, hardness of the coating and the size of the area to be removed. The most commonly used removal methods are chemical stripping, mechanical stripping, thermal scraping, mechanical scraping and laser ablation.
Some coatings can be softened or partially dissolved by chemical solvents. The remover is recommended by the paint manufacturer or prepared according to the formula recommended by the paint manufacturer. Follow the manufacturer's instructions to avoid damaging circuit boards and components as much as possible, however, it is always a good way to test the remover on discarded circuit boards. In many cases, the solvent can be selectively applied with a cotton swab by covering the surrounding area. Once the coating material becomes soft, the coating can be gently removed with a brush or stick.
In many cases, neutralizers must be added around the clearing area to prevent the continuous action of solvents. If the chemical substances of the remover are not thoroughly cleaned, the ion residues will be left on the circuit board. The acrylic three proof paint, which affects the reliability of components, is most sensitive to solvents. Therefore, they can be easily removed by using this technology. Silicone and polyurethane coatings are least sensitive to solvent removal. In general, solvent removal techniques are ineffective for epoxy and p-xylene.
Some three proofing paints can be removed from PCB and component surfaces by simple stripping or scraping. These soft coatings can be removed with toothpicks, sticks or sharp knives. This mechanical removal method can be combined with heating or solvent removal technology. In this removal process, care must be taken to ensure that elements and laminates are not damaged. This cleaning technology is often used to remove soft silicone based three proofing paint or other flexible three proofing paint.
Another coating removal technique uses a heat source to soften or decompose the coating to be removed. Usually a hot air gun or soldering iron is used as the heat source. After the coating to be removed is softened, the coating can be peeled off by gently pressing with a dental tool or a wooden stick. This cleaning method is applicable to most three proofing paints. Special care must be taken when heating the coating to avoid damaging the laminate under the element or adjacent elements. This technique can be used to remove acrylic, epoxy, and silicone coatings.
The micro grinding coating removal method uses various soft abrasives to break the three proofing paint through a small nozzle accelerated by inert gas. The mixture of walnut shell, glass, plastic bead powder, and other powder mixtures are pushed to the surface of the coating by the nozzle to grind the coating to a little air pressure. The removal of the intermediate nozzle directly affects the effect of the process. Ionized air source is usually used to offset the static charge generated in this process. This process can be used to remove the coatings including p-xylene, polyurethane and epoxy based coatings in the conformal coating of the three proofing paint for circuit boards
When it is required to remove the three proofing paint accurately, low light source shall be used. The high energy density pulse of laser gradually removes or ablates the coating material. A laser source with correct energy level and frequency, as well as several laser light source channels, must be established, so that it can only ablate the coating without damaging the materials below or around the coating. The coating can be selectively ablated with laser beam area as small as several microns. The polyxylene coating can be removed in this way.
Visually check whether the three proofing paint is removed in the correct area.
PCB manufacturers, PCB designers and PCBA manufacturers will explain how to remove the three proofing paint during the rework of PCBA.