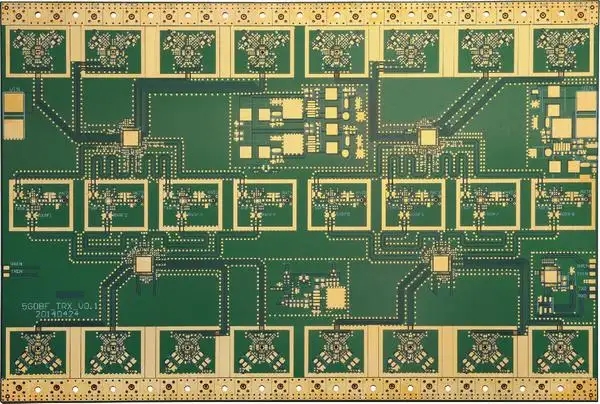
Failure of circuit board may be caused before and after application of three proofing paint
In order to ensure the high reliability and safety of circuit boards in key applications, the three proofing paint is widely used on circuit boards, because electronic failures may cause very serious consequences, even life threatening. In order to ensure that the reliability and safety of the three proofing paint meet the requirements, the components coated with the three proofing paint must be exposed in a series of different environments under appropriate test conditions to determine the performance range and limits suitable for the function of the circuit board. Basic tests include electrical performance tests and accelerated humidity tests, among which advanced tests can simulate various severe environmental conditions, such as salt spray, extreme temperature or rapid environmental change tests. The purpose of coating three proofing paint in the circuit board design is to protect PCB and ensure that they can work effectively in the final use environment. However, in some cases, even if the circuit board is coated with three proofing paint, the circuit board may have partial poor function, or even complete failure. At this time, these three proofing paint tests become an expensive and time-consuming nightmare for the Circuit board assembly manufacturer, and will also affect the reputation of the assembly manufacturer.
With the development of electronic technology, to achieve more functions in a smaller size, the probability of circuit board failure also increases. As the size of components becomes smaller and smaller, the spacing becomes narrower and narrower. Many designs are gradually approaching the limit of design rules, sometimes even challenging the limit of manufacturability. The more designers break through the limit of manufacturability, the higher the probability of failure will be.
In addition to the failure problems related to the circuit board design, when the circuit board is in a humid and ionic pollution environment, the density of the components is higher than before, and the components are closer to each other, which makes the hardware on the circuit board more vulnerable to corrosion. This is a complex diffusion controlled electrochemical process generated on the exposed metal surface. Cleaning the circuit board before coating the three proofing paint is a way to remove the corrosion conditions, which can more effectively coating the three proofing paint, improve the surface insulation resistance in these sensitive designs, and reduce the faults caused by the working environment.
Because PCB is very complex, there are many variables that may cause PCB failure. Some failure mechanisms occur slowly, which is helpful for detection, maintenance, and even repair. However, some failure mechanisms are sudden and unpredictable, and PCB failure is more likely in this case. Although the three proofing paint has been coated on the circuit board, faults still occur. The reason for this is that there are problems on the PCB before the three proofing paint coating process. Another case is that the coating material itself may not be suitable for this circuit board, or the coating method may not be suitable for this circuit board. There are also many other factors that can affect the correct coating of PCB, including the failure to clean components before coating, the failure to remove the original three proofing paint on the surface, electrostatic discharge, and even the poor structure of the unit itself to be coated.
The first and most critical step of applying three proofing paint to the circuit board is to check the circuit board before coating. This step is critical because it is to verify the overall quality of PCB to be coated and ensure that it is suitable for coating this kind of coating material and meets the customer's specification requirements. The inspection carried out at this stage is also crucial to detect any situation that may lead to circuit board failure, such as component failure, insufficient thickness of circuit board, and loose connection that affects connection performance. In terms of protecting the circuit board, the three proofing paint does have its limitations. During the coating operation, the existing pollutants on the circuit board will be sealed by the coating, which may lead to long-term problems - these pollutants may include fingerprints, flux residues and moisture, and other atmospheric pollutants. In order to achieve the best performance of the circuit board, the circuit board should be cleaned and dried frequently before applying the three proofing paint. Even if the so-called cleaning free flux is used when assembling the circuit board, cleaning the circuit board before coating the three proofing paint will help improve the performance and reliability of the circuit board.
As we all know, heat has a great impact on PCB and its components, and is another enemy of PCB. During the operation of the circuit board, various materials inside the PCB will experience a wide temperature variation range, and each component has a specified thermal variation range. The component will absorb heat. The amount of heat absorbed depends largely on its size and shape. The higher the power and the higher the density, the more heat will be generated by electronic products, and excessive heat will produce obvious mechanical stress, which will affect the connection of soldering tin and burn the components. To extend the life of devices and prevent failures, effective management of heat transfer is essential. The overheating on the circuit board will not only accelerate the failure mechanism, but also cause the device to become too hot to handle, and in some cases, it will also bring fire risk.
In addition to the problems related to heat, the continuous promotion of miniaturization means that there is no space for electronic products to accommodate multiple circuit boards, and the number of designs using hybrid technology is increasing. In the design, analog circuits, digital circuits and radio frequency (RF) circuits are closely combined with high-voltage circuits, which makes it more and more difficult to meet the gap and creepage design requirements. Even if the environment in which the circuit board is located has only a very small change, whether the increase of dust, humidity, splashing or exposure to potentially corrosive gases, it is enough to make the originally safe functional design exceed the safe operating clearance and creepage range, and cause performance failures.
Other factors that cause board and component failures include poor solder joints, unused or excessive flux, and tin whiskers. Cold solder joint refers to the solder joint formed when the soldering tin is not completely melted during the assembly process. This kind of solder joint causes poor connection of surface mounted components, which will burn the components and cause power problems. Residual flux will also cause corrosion due to absorption of moisture, resulting in short circuit and damage to components. Tin whiskers can also cause short circuits. During the operation of the device, the three proofing paint can usually prevent the formation of tin whiskers. However, if tin whiskers already exist in the components before coating, the effect of coating the three proofing paint will be poor. Generally speaking, the effect of three proofing paint on relieving tin whiskers mainly depends on the coverage of the coating, rather than the performance of the coating. Although some ambiguous data show that the harder and tougher the coating is, the better the tin whiskers can be relieved. However, this relief must be balanced with the impact of prolonging the life of solder joints. In general, it may be a more effective strategy to focus on achieving 100% coverage of metal surfaces.
Surge, lightning strike and overheating will cause damage to the wiring of the circuit board. Damage to silver or copper conductive paths is usually visible to the naked eye, but this is not always the case. Damage to wiring can cause serious problems, including conductivity problems, component problems, and device reliability problems. Fortunately, these wiring damages can usually be detected in the initial inspection and repaired.
Although this is not an exhaustive list of PCB failures caused by each single factor, it provides a comprehensive overview of the key factors that cause PCB failures. It can be used to help find the causes of PCB failures when PCB failures occur. Finally, the PCB design itself may be responsible for PCB failures. In order to improve the life of the circuit board, it is necessary to ensure that the selected components and materials are suitable, the layout of the circuit board is sufficient, and the special requirements of the design are verified. The design is also important in determining the appropriate coating method. The design of the circuit board will involve the cycle and cost of the three proofing coating process. Some simple things, such as trying to place connectors or other non coating areas on the same side of the component, can be easily coated, which can have a huge impact on the convenience of component coating, coating cost and overall reliability.
PCB fault after application of three proofing paint
There are many variables that can cause PCB failure after the coating process is completed. Generally speaking, these failures may be caused by inappropriate coating materials and methods, or by inadequate surface treatment, or by some chemical actions that have nothing to do with the coating materials. When condensation and ionic impurities combine to form a conductive channel between PCB wires, the coating with poor performance may lose its insulating property on the PCB surface. There is no doubt that condensation will seriously test the insulation resistance of the coating. There are many coating products that can withstand this kind of test. Therefore, this kind of problem can be avoided by selecting
appropriate materials at the beginning of design.
If the coating is not completely cured, its protective effect cannot be fully exerted. In this case, the coating process is the culprit. The correct coating process is a prerequisite for successful coating. As long as the coating process is correct, a series of coating problems can be solved at one time. For example, for poor coverage, insufficient thickness and sharp edge coverage, many coating materials are difficult to solve these problems. In areas prone to these problems, the coating is difficult to reach sufficient thickness, which is difficult to ensure the protective effect of the coating. These problems will be solved by combining material selection with coating technology and process. The IPC specification allows a dry film thickness of 30-130 microns, and thicker coatings are achieved by multiple applications. For example, when trying to obtain a dry film thickness of 130 microns, it is a disaster to use solvent based acrylic materials to achieve a dry film thickness of 130 microns at one time through selective coating process. Excessive bubbles, paint film shrinkage, coating delamination and additional stress will be generated on the components. The result of this coating is that the protective effect of the coating is relatively poor, and the protection of the circuit is not improved on the overall level. The coating process should aim at a uniform thickness of 30-50 microns, and focus on achieving perfect coverage for each coating, which is a better way to improve the protection of the three proofing paint on electronic circuits.
When applying the three proofing paint, it is important to get the correct coating thickness; Keep in mind that if the coating is too thick, it may cause the solvent to stay in the area where the coating is not fully cured. Similar to this situation, too thick coating will also lead to cracking of the coating during curing, and even lead to cracking of the coating of the coated component itself. This cracking is either caused by temperature change or caused by mechanical shock and vibration. The primary factor determining the reliability of the coating is the coating process. Generally, one kind of material with poor performance is well coated, while the other one with good performance is poorly coated. The effect may be equivalent when comparing the two cases, and sometimes the former is even better. When coating, it is necessary to cover the sharp edges sufficiently, instead of coating all metal surfaces with too thick material. Of course, some materials are "easier to apply" than others, and the coating process is as simple as possible; However, the performance of the final liquid applied coatings will always depend on their application effect.
Large arrays composed of discrete components will also face a huge coating challenge. This is due to the strong capillary force during coating, which often leads to disastrous results. Because there are areas on the circuit board that do not need to be coated and areas that need to be coated, at the junction of these two areas, the coating is prone to stress cracking, paint film separation and other coating defects in areas where the coating is too thick. This situation will eventually lead to premature failure of components, so try to avoid it!
Another reason for coating defects may also be the accidental interaction between other process materials used to prepare and manufacture PCB. Flux residue is a typical example of such problems. For example, in a "no cleaning" process, some materials used in the no cleaning process will inhibit the curing of certain types of coatings, or cause the insulation performance of the system to decline, which is more serious than any single material. To avoid this situation, the only way is to meticulously carry out the preparation before coating or implement the pre cleaning system before coating, otherwise, corrosive residues will cause the conductive wiring of PCB to bridge, which may lead to failure as time goes by. Although the coating may delay the failure of the circuit board for many years, the failure of the circuit board at a certain point in time is inevitable.
When the circuit board is powered on, the most important test for the performance of the three proofing paint is carried out under wet conditions. The three test conditions are condensation water, immersion or salt spray on the three proofing paint. The water containing soluble impurities is conductive, and it will find all weak points in the coating, eventually leading to a short circuit on the PCB surface. In order to provide protection under these circumstances, the metal surface of PCB must be 100% defect free covered with three proof paint, which is a real challenge to the coating material itself and the coating process. Fortunately, a new two-component three proofing paint material called "2K" can achieve a thicker coating thickness and perfect coverage effect, thus achieving a higher level of protection. Electrolube's 2K coating material has the advantage of excellent performance. It combines the toughness and corrosion resistance of the packaging resin with the ease of use of the coating. It has been positively proven in the three most demanding tests that the coating materials may experience, including electric condensation test and electric salt water immersion test.
conclusion
Our daily life and work depend on a variety of electronic devices, from smart phones, tablets, personal computers and laptops, to street lamps, televisions, refrigerators, microwave ovens and cars. PCB is the basis on which all electronic devices can play a role, and is where the vitality of electronic devices lies. When PCB fails, it will cause huge damage, which is very important in aerospace applications. Therefore, the materials selected to protect electronic components can actually determine the success or failure of the printed circuit board, especially when the circuit board must withstand a large number of physical shocks and thermal cycles. The inspection and testing before and after coating is critical to ensure the reliable operation and improve the life of PCB, especially for those PCBs destined to work in harsh environments. Proper materials shall be selected to protect the circuit board. These materials shall be used for good coating and the coating shall be completely cured. Check the interaction between the coating materials and chemicals used in other processes, and thoroughly clean the components before coating. If possible, spend some time in the design phase to simplify the coating process. It is a simple method to place the connector and as many components as possible without coating on the same side of the assembly without coating the connector, which will simplify the coating process of the three proofing paint. Unfortunately, after using the three proofing paint, PCB may still fail, but the positive news is that PCB failures can be prevented. Through systematic pre coating inspection, correct material selection, coating method, and more strict post coating testing, PCB failures can be effectively prevented.