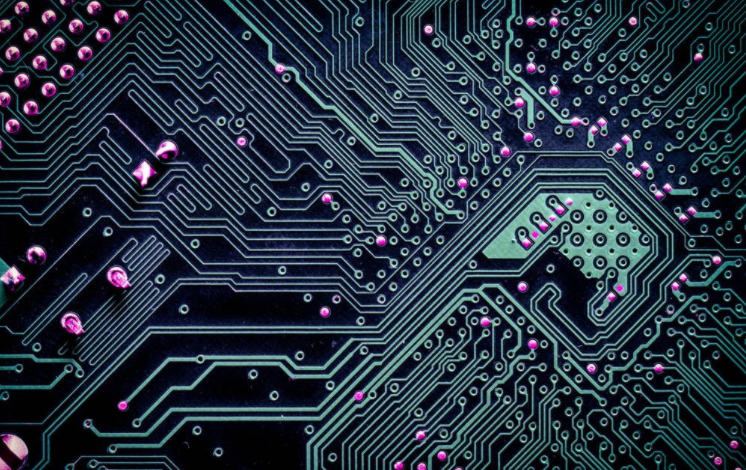
How to select base plate for drilling in PCB production
The requirement of the upper backing plate for PCB drilling is to have a certain surface hardness to prevent burrs on the upper surface of the drilling. But it should not be too hard to wear the drill bit. It is required that the resin composition of the upper and lower base plates shall not be too high, otherwise molten resin balls will be formed and adhered to the hole wall during drilling. The greater the thermal conductivity, the greater the better, so that the heat generated during drilling can be quickly taken away, reducing the temperature of the drill bit during drilling, and preventing the drill bit from annealing. There must be a certain rigidity to prevent PCB board from vibrating when lifting the drill, and there must be a certain elasticity to immediately deform when the drill bit is in contact with the drill, so that the drill bit can accurately align with the position of the hole to ensure the drilling position accuracy. The material shall be uniform, and there shall be no uneven soft and hard nodes caused by impurities, otherwise the drill bit is easy to break.
If the surface of the upper backing plate is hard and slippery, the small diameter drill bit may slip and deviate from the original hole position to drill elliptical inclined holes on the PCB. The top backing plates used in China are mainly 0.2~0.5mm thick phenolic paper adhesive plate, epoxy glass cloth plate and aluminum foil. For example, LF2Y2 (No. 2 rust proof aluminum in semi cold hardening state or LF21Y (No. 21 rust proof aluminum in cold hardening state) with a thickness of 0.3mm can be used as the top backing plate for drilling ordinary double-sided plates, which has a good effect and can prevent burrs on the surface of the drilling hole when the hardness is appropriate. Due to the good thermal conductivity and rigidity and elasticity of aluminum, it has a certain heat dissipation effect on the drill bit. The material of aluminum foil is more uniform than that of phenolic plate, and there is no impurity to cause the drill bit to break and the probability of hole deflection is greater than that of phenolic plate.
It can reduce the drilling temperature and is an environment-friendly material. It is increasingly widely used in many factories. Compared with phenolic board and epoxy board, aluminum foil is not likely to pollute the hole due to the resin contained in it, The thickness of aluminum foil commonly used in the use process is 0.15, 0.20 and 0.30 mm. In the actual use process, 0.15 has the best contact with the PCB surface, but it is difficult to control the process during cutting, transportation and use. The price of 0.30 is a little higher. Generally, 0.20 mm aluminum foil is used in compromise, and the actual thickness is generally 0.18 mm. There is a composite upper backing plate abroad. Its upper and lower layers are 0.06mm aluminum alloy foil, and the middle layer is a pure fiber core, with a total thickness of 0.35mm. It is not difficult to see that this structure and material can meet the requirements of the upper backing plate for PCB drilling. It is used as the upper backing plate for high-quality multilayer boards. Compared with aluminum foil, it has the advantages of high drilling quality, high hole location accuracy, and improved drill life due to small wear. At the same time, the shape of PCB recovered after being subjected to external force is much better than that of aluminum foil, and its weight is much lighter. It is especially suitable for drilling small holes. The underlays used in China are phenolic paper board, cardboard and sawdust board.
Cardboard is soft and easy to produce burrs, but its texture is even and it is not easy to break the drill bit and bite the drill bit, but it is cheap and can be used in thin copper foil or single panel. The wood chip board has poor texture uniformity, and its hardness is better than that of paper board, but if the PCB copper foil drilled is more than 35 microns, burrs will occur. I have tried to drill 70 microns copper foil double-sided boards with this board, and all of them failed. The best hardness uniformity of phenolic paper board is between the first two, and the use effect is the best, but it is expensive and not environmentally friendly. There is also a composite lower backing plate abroad. Its upper and lower layers are 0.06mm aluminum alloy foils, and the middle layer is a pure fiber core, with a total thickness of 1.50mm. Of course, its performance is very outstanding and environmental friendly, which is much better than that of phenolic paper board. Especially when drilling multilayer boards and small diameter holes, its advantages can be fully reflected. Of course, its disadvantage is that the price is expensive.
How to Select PCBA Factory to Avoid Pit Falling
1. The professional PCBA processing of PCBA processing plant is different from the traditional SMT patch and DIP plug-in. In the past, only electronic processing was used to provide materials for customers, and the processing plant only needed to produce as required. However, PCBA processing is a one-stop processing service for material procurement, material quality inspection, warehouse management, SMT patch, DIP plug-in, quality inspection, and finished product assembly. Therefore, PCBA processing plant is required to be professional, including professional equipment, Professional process system management and perfect quality control system.
2. Look at the service awareness of PCBA processing plant. The interfacing personnel of PCBA processing plant and the entire company team need to have a good service awareness. Only in this way can customers take the initiative to assume responsibility and solve problems when they encounter problems.
3. The experience of fast proofing of PCBA processing plants is that many PCBA processing plants only make batch orders, and they are not interested in small quantities of proofing orders. Even if such processing plants cooperate, they cannot cooperate 100%, which will only increase troubles and affect the efficiency of fast proofing of PCBA.
4. When choosing a PCBA express proofing factory, we should pay special attention to whether we can complete the proofing work on time with quality and quantity guaranteed. Because of the particularity of rapid proofing, we often need to complete this matter in a certain time window, otherwise, there will be no market for the product after this time point. Therefore, it is also very important to make delivery on time.