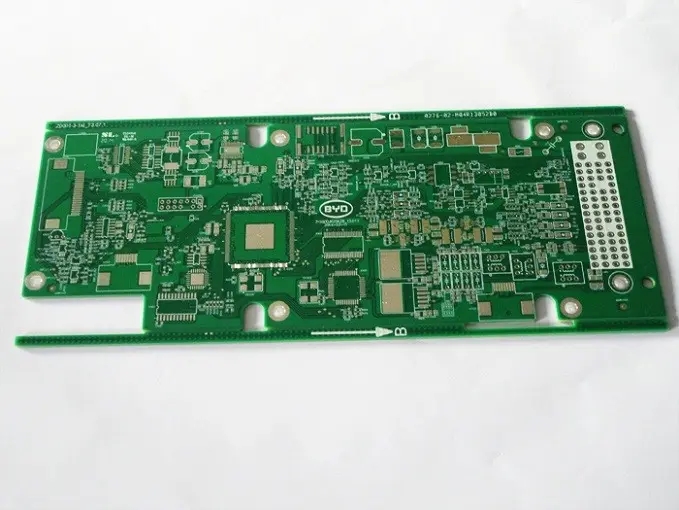
Problems in screen printing of double-sided flexible circuit board
FPC screen printing is a common printing method for flexible circuit boards. In Flexible circuit board printing, single-sided printed circuit boards are more common, double-sided printed circuit boards are relatively few, but double-sided hard circuit boards are more common. The principle of double-sided flexible circuit board is the same as the production principle of common printed hard circuit board. The printed hard circuit board realizes the conduction between two layers of lines through copper sinking; The double-sided flexible circuit board is made by infiltrating conductive carbon ink or silver ink through small holes and filling the upper and lower layers of circuits. The conductive inks used for the printed circuit board mainly include silver ink and carbon ink. The following is a brief introduction to the screen printing process of double-sided flexible circuit board with carbon ink as the conductive ink and the problems to be noted.
1: Screen printing of upper circuit
The materials must be baked to prevent the shrinkage deformation of the materials from causing trouble to the subsequent process. The line with high accuracy requirement is selected as the upper line (numbered A to distinguish the lower line B). Use carbon ink screen to print A-side lines. Pay special attention to controlling the thickness of the ink during screen printing to ensure that the resistance requirements of the lines are met.
2: Stamping carbon filling hole
The hole diameter is generally 0.8~1.0 m m. The carbon filling hole must be properly selected. The hole is too large. When screen printing the lower line, too much carbon ink permeates through the carbon filling hole, and the excess ink will flow through the carbon filling hole and remain on the screen printing workbench, which is easy to cause short circuit of the line. Moreover, due to the limit of the line width, the carbon filling hole cannot be made too large. However, if the carbon injection hole is too small, it is difficult to make the stamping die. In addition, after the carbon injection hole is punched, the material P E T used to make the circuit board is not easy to fall off, so it must be peeled off manually. Otherwise, the carbon filling hole will be covered in the next process, which will hinder the ink flow and affect the continuity of the upper and lower layers of lines. Moreover, the carbon filling hole is too small, and the amount of ink passing through is too small to make the upper and lower layers of lines conductive. In the process of punching carbon filling holes, it should be specially noted that side A (upper line surface) must face upward, so as to make the stamping fins (i.e. flash, serrated protrusions) face the side without screen printing. Its role will be fully reflected in the next process. In order to increase the conduction probability of the two layers of lines, a carbon filling hole can be added at the same place. The distance between the two holes depends on the line width and cannot be too large. In view of the small size and close distance of carbon injection holes, it is difficult to make a stamping die. Usually, two sets of dies are made, one of the two small holes is punched at a time, that is, half of the carbon injection holes are realized in two times.
3: Screen printing of lower line
With the positioning hole as the benchmark, print the lower line on the non screen printed surface. Since the front is facing the B side, a layer of ink is also covered on the front after screen printing. Under the action of gravity, the flowing carbon ink can fill the carbon filling hole smoothly and connect with the line on the A side (the upper line), so that the lines on both sides of A and B can be connected. If the front edge faces the A side, when screen printing on the B side, the ink flows to the A side line through the carbon filling hole, which is blocked by the front edge. The front edge has a certain height h. The ink is not easy to flow through the A side line of the front edge to connect, so the A and B layers of lines are less likely to be connected. The fluidity of conductive ink for screen printing is also important for the conduction of carbon filling hole. The ink is viscous and has poor fluidity, and the conduction probability of upper and lower layers is also small. In the process of screen printing, if machine printing is used, the worktable uses a vacuum suction device to facilitate the flow of conductive ink, but it is often easy to leave ink on the worktable, and the residual ink must be removed in time, otherwise the quality and beauty of the circuit will be affected, or even the circuit will be short circuited. If manual printing is used, the workbench does not have a vacuum suction device. After screen printing, the circuit board should be placed in a drying oven for drying after a period of time, so that the conductive ink can flow fully and the two layers of lines can be connected. During screen printing, the ink thickness shall be controlled to meet the requirements of line resistance.
4: Forming, stamping and final product inspection According to the use of the circuit board, stamping forms a shape with certain size requirements. Test whether the circuit is short circuited, open circuited and the resistance meets the requirements.
PCB manufacturers, PCB designers and PCBA manufacturers explain the problems that should be paid attention to in double-sided FPC screen printing.