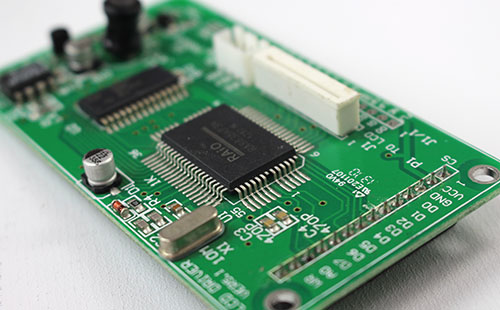
Summary of common problems in PCB dry area (circuit, solder resistance, text)
1. Why plug holes when BGA position is in resistance welding? What are the acceptance criteria?
A: First of all, the solder plug hole is to protect the service life of the via. Because the hole diameter of the plug required for the BGA position is generally small, between 0.2 and 0.35 mm, some of the liquid medicine in the hole is not easy to be dried or evaporated during the processing of the later process, and it is easy to leave residue. If the hole is not plugged or the plug is not full in the solder block, there will be residual foreign matters or tin beads during the processing of the later process, such as tin spraying and gold deposition. Once the customer installs the components and welds them at a high temperature, Foreign matters or tin beads in the hole will flow out and stick to the element, causing defects in element performance, such as open circuit and short circuit. The BGA position is in the solder plug hole A, must be full B, no redness or false copper exposure is allowed, and no too full protrusion is allowed to be higher than the pad to be welded beside (which will affect the effect of component mounting).
2. What is the difference between the table glass of the exposure machine and ordinary glass? Why is the reflector of the exposure lamp concave and uneven?
Answer: The table glass of the exposure machine will not produce light refraction when the light shines through. If the reflector of the exposure lamp is flat and smooth, when the light shines on it, according to the principle of light, it forms only one reflected light to shine on the board to be exposed. If the concave is uneven, according to the principle of light, the light shining on the concave and the light shining on the convex will form countless scattered lights, forming an irregular but uniform light to shine on the board to be exposed, so as to improve the exposure effect.
3. What is side development? What are the quality consequences of excessive side development?
Answer: The bottom width area of the developed part of the green oil on one side of the resistance welding window is called side development. When the side development is too large, it means that the greater the green oil area of the developed part in contact with the substrate or copper skin, the greater the degree of suspension it forms. When the side development part is attacked by high temperature, pressure and some potions that are more aggressive to the green oil in the later process processing, such as tin spraying, tin deposition, gold deposition, etc., it will form oil loss. If there is a green oil loss bridge in the IC position, The bridging short circuit will be caused when the customer installs the welding element.
4. What is bad solder mask exposure? What quality consequences will it cause?
Answer: After processing in the solder mask process, it is exposed in the bonding pad or the place to be welded where the components are mounted in the later process. During the solder mask alignment/exposure process, due to the problems of the light barrier or the exposure energy and operation, the outer side of the green oil covered by this part or all of it is exposed to light and has a cross-linking reaction. When developing, the green oil in this part will not be dissolved by the solution, and the outer side or all of the bonding pad to be welded cannot be exposed, It is called poor welding exposure. Poor exposure in the later process will lead to failure to mount components, poor welding, and even open circuit in serious cases.
5. Why should the grinding plate be treated before the circuit and resistance welding?
Answer: 1. The circuit board surface includes the foil clad substrate and the pre copper plated substrate after hole metallization. In order to ensure the firm adhesion of the dry film to the surface of the substrate, it is required that the surface of the substrate should be free of oxide layer, oil stain, fingerprints and other dirt, drilling burr and rough coating. In order to increase the contact area between the dry film and the substrate surface, the substrate is also required to have a micro rough surface. In order to meet the above two requirements, the substrate shall be carefully treated before film pasting. The treatment methods can be summarized as mechanical cleaning and chemical cleaning.
2. The same principle applies to resistance welding. Before resistance welding, the grinding plate is used to remove some oxide layers, oil stains, fingerprints and other dirt on the plate surface. In order to increase the contact area between the resistance welding ink and the plate surface and make it more secure, the plate surface is also required to have a micro rough surface (just like the wheel tire of a car, the tire must be ground to a rough surface to better combine with the glue). If the circuit or solder mask is not grinded before processing, and there are some oxide layers and oil stains on the surface of the board to be coated or printed, it will directly separate the solder mask and the circuit film from the board surface to form an isolation, and the film in this area will fall off and peel off in the later process.
6. What is viscosity? What effect does the viscosity of solder resist ink have on PCB production?
A: Viscosity is a measure that prevents or resists flow. The viscosity of solder resist ink has a considerable impact on PCB production. When the viscosity is too high, it is easy to cause no oil or screen sticking. When the viscosity is too low, the fluidity of the ink on the board surface will increase, which is easy to cause oil entry holes and local oil film. Relatively speaking, when the outer copper layer is thick (≥ 1.5Z0), it is necessary to control the viscosity of the ink to be lower. If the viscosity is too high, the fluidity of the ink will be reduced. At this time, oil free and exposed lines will form at the bottom and corner of the line.
7. What are the similarities and differences between dirty development and poor exposure?
Answer: The same point: a is that there is solder mask oil left on the surface of the exposed copper/gold area to be welded after solder mask, b is basically caused by the same reasons, such as the time, temperature, exposure time and energy of baking the plate.
Differences: The area formed by poor exposure is large, the residual solder mask oil is from outside to inside, and the width and degree are relatively uniform, most of which appear on the non porous pad, mainly because the ink in this part is exposed to ultraviolet light. The residual solder mask oil with poor development is only a thin layer of oil at the bottom of the layer. Its area is not large, but it forms a thin film. This part of the ink is mainly due to different curing factors, forming a layered form with the surface layer ink, which generally appears on the perforated pad.
8. Why do bubbles occur in resistance welding? How to prevent?
Answer: (1) Solder resistance oil is generally prepared by mixing the main agent of the ink+curing agent+diluent. When the ink is mixed and stirred, there will be some air left in the liquid. When the ink flows to the board after being squeezed by the scraper and the screen, the gas in the ink will flow rapidly and volatilize rapidly when it encounters strong light or equivalent temperature in a short time. (2) The line spacing is too narrow and the line is too high, so the solder mask ink cannot be printed on the substrate during screen printing, resulting in the presence of air or moisture between the solder mask ink and the substrate. The gas expands when heated during curing and exposure, causing bubbles. (3) The single line is mainly caused by the high line. When the scraper contacts the line, the angle between the scraper and the line increases, so that the solder mask ink cannot be printed to the bottom of the line, There is gas between the side of the line and the solder mask ink, which will form a small bubble when heated.
Prevention: a The prepared ink is still for a certain time before it is used for printing, b The printed board is also still for a certain time so that the gas in the ink on the board surface slowly volatilizes with the flow of the ink, and then it is taken off and baked at a certain temperature.
9. What is resolution?
Answer: Within a distance of 1mm, the resolution of the lines or spacing lines that can be formed by the dry film resist can also be expressed by the absolute size of the lines or spacing. The separation rate of the dry film is related to the thickness of the resist film and the thickness of the polyester film. The thicker the resist film is, the lower the resolution is. When light is exposed through the photographic plate and the dry film of the polyester film, the more serious the light side is due to the scattering effect of the polyester film on the light, The lower the resolution.
10. What are dry film and etching and electroplating resistance?
A: Corrosion resistance: the dry film corrosion resistant layer after photopolymerization shall be resistant to the etching of ferric chloride etching solution, persulfuric acid etching solution, acid chlorine, copper etching solution, and sulfuric acid hydrogen peroxide etching solution. In the above etching solution, when the temperature is 50-55 ℃, the dry film surface shall be free of hair, leakage, warping and falling off. Electroplating resistance: In acid bright copper plating, fluoroborate common lead alloy, fluoroborate bright tin lead alloy and various pre-treatment solutions for the above electroplating, the polymerized dry film anti-corrosive coating shall be free of surface hair, infiltration, warping and falling off.
11. Why does the exposure machine absorb vacuum when exposing?
Answer: In the exposure operation of non parallel light (the exposure machine with a "point" as the light source), the degree of vacuum absorption is a major factor affecting the exposure quality. Air is also a medium layer. If there is air between the plate, film and air extraction film during exposure, light refraction will occur and the exposure effect will be affected. Vacuum absorption is not only to prevent light refraction, At the same time, it is also to prevent the gap between the film and the board from expanding and ensure the quality of alignment/exposure.
12. What are the advantages of using pozzolanic grinding plates for pretreatment? Disadvantages?
Answer: Advantages: a. The combination of abrasive pumice powder particles and nylon brush is tangent to the cotton cloth, which can remove all dirt and expose fresh and pure copper; b. It can form a completely sandy, rough, uniform, multi peaked surface without cultivated ditch; c. The connection between the surface and the hole will not be damaged due to the relaxation of the nylon brush; d. Due to the flexibility of the relatively soft nylon brush, it can make up for the uneven board surface caused by brush wear; e. Because the board surface is uniform and without grooves, the scattering of exposed light is reduced, thus improving the imaging resolution. Disadvantages: pumice powder is easy to damage the mechanical part of the equipment, control the particle size distribution of pumice powder, and remove pumice powder residues on the surface of the substrate (especially in the hole).
13. What will happen if the development point is too large or too small?
Answer: The correct development time is determined by the development point (the point where the unexposed dry film is developed from the printed circuit board). The development point must be kept at a constant percentage of the total length of the development section. If the development point is too close to the outlet of the development section, the unpolymerized corrosion resistant film cannot be fully cleaned and developed, and the residue of the corrosion inhibitor may remain on the board surface, causing unclean development. If the developing point is too close to the entrance of the developing section, the polymerized dry film may become hairy due to the etching of Na2C03 due to the contact with the developing solution for a long time, resulting in excessive development due to film loss and luster loss. Generally, the development point is controlled within 40% - 60% of the total length of the development section (35% - 55% of our company).
14. Why should I pre bake the board before printing characters?
Answer: The pre baking plate a before character printing is to enhance the binding force between the plate and the characters, and b to enhance the hardness of the solder resist ink on the surface of the plate, so as to prevent the solder resist oil from being crossed during character printing or post process processing.
15. Why should the brush of the pretreatment plate grinder be swayed?
Answer: There is a certain distance between the grinding needle rollers. If you don't swing the grinding plate directly, there will be many places that can't be grinded, resulting in uneven cleaning of the plate surface. If you don't swing, straight grooves will be formed on the plate surface, which is easy to cause broken lines. If you don't swing the hole edge, it is easy to break holes and cause tail dragging.
16. What role does the scraper play in printing?
Answer: The angle of the scraper directly controls the oil volume, and the evenness of the scraping blade directly affects the surface quality of the printing.
17. What is the influence of temperature and humidity in resistance welding and circuit darkroom on PCB production?
Answer: When the temperature and humidity in the darkroom are too high or too low: 1. It will increase the garbage in the air; 2. It is easy to stick the film in the opposite position; 3. It is easy to deform the film; 4. It is easy to oxidize the board.
18. Why is resistance welding not used as developing point?
answer "Because there are many variable factors of solder mask ink, first of all, there are many kinds of ink, and each ink has different properties. During printing, the thickness of each board ink is different due to the influence of pressure, speed and viscosity. It is not as simple as the dry film, and the thickness is relatively uniform. At the same time, solder mask ink is also affected by different baking time, temperature and exposure energy in the production process. Relatively speaking, solder mask is developed It is difficult to ensure the same effect on each board. Therefore, it is of little practical significance to use resistance welding as developing point.
19. How did ghosts come into being? How to prevent?
Answer: Ghost usually appears on the white board, and it is generally at the position where the window is opened on one side. Because the white board does not have the UV light blocking function, when the PCB solder mask is exposed, part of the UV light on the unopened window surface will pass through the substrate to the edge of the PAD position of the window, causing the green oil at the bottom of the green oil window opening position to be exposed and cannot be completely developed, forming a ghost. Phantom of yellow plate is usually caused by the refraction or diffraction of ultraviolet light, which is common in the golden finger position.
Prevention: 1. The window on the white board shall be designed as large as possible on both sides. 2. If the window is opened on one side, the back of the window opening position shall be designed as large copper as possible. 3. When the window opening is single-sided and the back side of the window opening position is the substrate, the exposure energy of the substrate surface is 1-2 grids lower than that of the window opening surface during exposure.
20. What role does solder resist ink play in PCB?
A: Soldering resistance ink: It is a protective layer, which is coated on the substrate and circuit of the printed board that do not need to be welded. The purpose is to prevent bridging between lines during welding, provide a permanent electrical environment and a chemical resistant, heat resistant and insulating protective layer, and bring beauty to the appearance of PCB. Solder resist ink is divided into two systems: 1. thermosetting epoxy ink; 2. liquid photosensitive imaging ink. PCB manufacturers, PCB designers, and PCBA manufacturers will explain the summary of common problems in PCB dry area (circuit, solder resistance, and text).