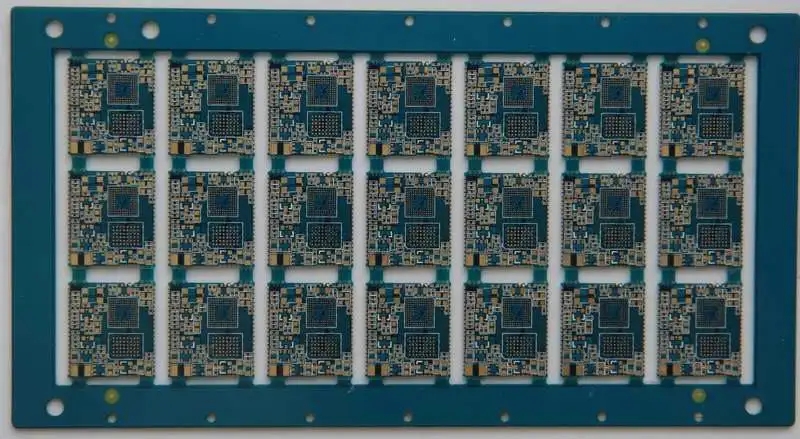
The circuit board manufacturer explains the method of manual welding
In SMT manufacturing process, manual welding, plate repair and repair are indispensable processes. With the continuous development of technology and the improvement of people's demand, there are some new components that are difficult to package and repair, such as BGA, CSP, QFN, etc. How to repair, how to improve the success rate of repair, we must master the correct welding method. 1、 Tools for manual welding The main tools for manual welding are electric soldering irons. There are many kinds of electric soldering irons, which can be divided into direct heating type, induction type, thermostatic electric soldering irons, intelligent electric soldering irons, tin suction pumps, hot air soldering stations, electric heating clips, etc. according to the heating mode. Manual welding shall
In SMT manufacturing process, manual welding, plate repair and repair are indispensable processes. With the continuous development of technology and the improvement of people's demand, there are some new components that are difficult to package and repair, such as BGA, CSP, QFN, etc. How to repair, how to improve the success rate of repair, we must master the correct welding method.
1、 Tools for manual welding
The main tool for manual welding is electric soldering iron. There are many kinds of electric soldering iron, which can be divided into direct heating type, induction type, thermostatic electric soldering iron, intelligent electric soldering iron, tin suction pump, hot air soldering table, electric heating clamp, etc. according to the heating mode. Anti static constant temperature electric soldering iron shall be selected for manual welding.
2、 Operation posture of welding
1. Distance maintained by welding
The gas generated during welding will be harmful to human body, so when using electric soldering iron, the distance between nose and electric soldering iron should be more than 30cm, and 40cm is a suitable distance.
2. Electric iron holding method
The electric soldering iron has three kinds of grip methods: reverse grip, positive grip and pen grip. The reverse grip action is stable, and it is not easy to fatigue after a long time of operation. It is suitable for holding high-power electric soldering iron. The positive grip is suitable for the operation of medium power electric soldering iron or electric soldering iron with elbow. The pen grip method is generally used when welding components and repairing circuit boards.
3. How to handle tin wire
There are generally two ways to handle tin wires. For some lead tin wires, wear gloves during welding or wash hands after operation to avoid eating. The electric soldering iron shall be generally equipped with a soldering iron frame and placed on the right front of the workbench. After use, the electric soldering iron shall be placed on the soldering iron frame. Pay attention not to touch the soldering iron head with wires and other objects to avoid short circuit after the insulation is damaged by the soldering iron head.
3、 Five step welding method
1. Prepare for welding - clean the soldering iron
(1) Add tin to the soldering iron head and clean the soldering iron head, which is conducive to heat conduction
(2) Do not use a knife or other things to scrape the oxide layer of the soldering iron head
2. Heating weldment
(1) Place the soldering iron head at the connection point of the metal to be welded (the place with the largest heat capacity)
(2) Start heat flow and heat to the surface of the metal to be welded
3. Molten tin wetting
(1) Place the tin wire between the connection point of the soldering iron head and the metal to be welded to form a thermal bridge.
(2) Flux flows in the cold direction and soaks the pad - it flows from the soldering head to the entire pad to remove the oxide layer and promote heat conduction.
(3) Move the solder wire to the opposite side of the heat source, the molten tin flows in the heat direction, soaks the pad and pin, and capillarity, diffusion, dissolution and metallurgical bonding occur at the interface.
(4) Push the flux residue toward the surface and edge of the solder joint.
4. Withdraw the tin wire
Remove the tin wire first and then the soldering iron, otherwise the tin wire will solidify on the solder joint.
5. Stop heating
(1) Cooling and solidification to form solder joints
(2) Note: Do not shake the components and PCB when the tin wire is not completely solidified, so as to avoid false soldering.
PCB manufacturing, PCB design and PCBA processing manufacturers will explain the method of manual welding.