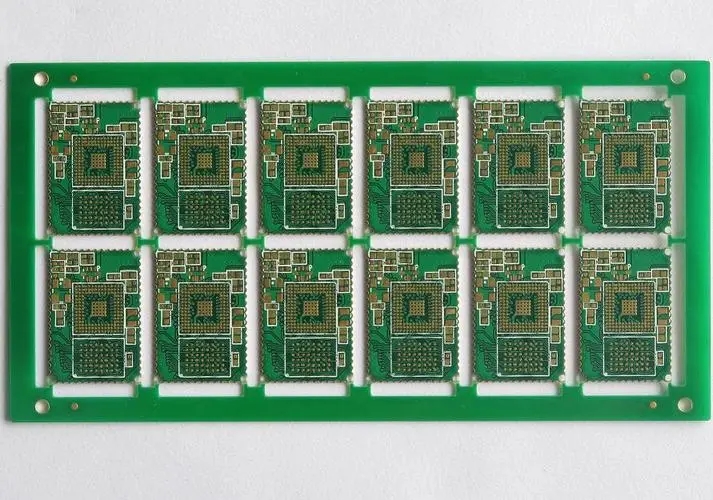
What impact does lead-free technology have on PCB manufacturing?
In the past decade, we have clearly seen the impact of environmental issues on electronic manufacturers. In addition to the strict control on the use of CFCs, the reduction of lead and halogen use is a major project for circuit board manufacturers. In terms of electronic assembly applications, major manufacturers in Europe, the United States and Japan all put forward lead-free requirements, and the largest impact on the production of circuit boards was the first to promote tin spraying alternative technology. There are many technologies that can replace tin spraying, but it is very difficult to choose between advantages and disadvantages. Basically, the alternative soldering technology is selected, and the most important factors are production cost, part weldability, process compatibility, contact reliability, etc. Lead free tin spraying process also has solid product at present
In the past decade, we have clearly seen the impact of environmental issues on electronic manufacturers. In addition to the strict control on the use of CFCs, the reduction of lead and halogen use is a major project for circuit board manufacturers. In terms of electronic assembly applications, major manufacturers in Europe, the United States and Japan all put forward lead-free requirements, and the largest impact on the production of circuit boards was the first to promote tin spraying alternative technology.
There are many technologies that can replace tin spraying, but it is very difficult to choose between advantages and disadvantages. Basically, the alternative soldering technology is selected, and the most important factors are production cost, part weldability, process compatibility, contact reliability, etc. At present, lead-free tin spraying process also has a solid product, but the scope of use of materials or equipment is very limited. Whether it will become the mainstream of the industry remains to be tested over time.
1. Updating of PCB substrate
In addition to lead-free soldering tin, halogen-free substrate is also an important issue in circuit board manufacturing and electronic product production. Many base material manufacturers have introduced halogen-free formula, and how to match the lead-free soldering process needs to be considered together.
In order to maintain the flame resistance and avoid halogen, Circuit board manufacturers try to use different methods such as adding phosphorus and boron to achieve the same function. However, many use experiences have found that it is difficult for the overall performance to reach the same level as the previous materials, especially in terms of chemical resistance.
After the lead-free system is adopted by the circuit board manufacturer, for example, the melting point of 96.5/3.5 tin silver alloy is 221 ° C. Parts may face a surface temperature of about 260~265 ° C during reflow. The operating temperature of wave soldering tin furnace is about 238~260 ° C, which is much higher than the traditional 63/37 tin lead alloy. The variation of these operating temperatures makes the PCB fabrication and assembly have to face the improvement of the temperature resistance of the substrate. At present, although the general circuit boards are still made of FR-4 materials, the industry can find that many new high-temperature substrates are gradually being introduced, and the glass transition point has also increased from about 140 degrees to about 170 degrees.
In the face of more and more sophisticated assembly of a variety of electronic components, the test of multiple assembly and rework is bound to be the challenge that the future circuit board substrate must face. How to improve the thermal shock resistance of the substrate will be a subject that PCB material manufacturers must face directly.
2. Selection of final metal surface treatment
In addition to tin spraying, there are still various final metal surface treatments that can be used for circuit board and electronic component assembly. How to provide proper metal surface treatment has also become an important test for circuit board manufacturing.