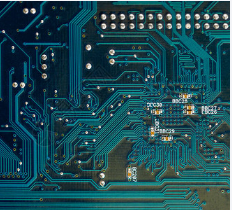
There are seven major wastes in PCB, namely, the waste of waiting; Waste of handling; Waste of defective products; Waste of action; Waste of processing; Waste of inventory; Excessive (early) waste in PCB manufacturing.
Waiting for waste: idle PCB equipment, idle equipment, unplanned downtime, production shortage, etc. The reasons for waiting generally include: poor order receiving or insufficient orders, unbalanced production lines, improper planning, downtime for material shortage, abnormal quality problems, etc. For example, if the switching between different material numbers on the production line is not fully prepared, it is easy to waste waiting; Problems in the previous process sometimes lead to the shutdown of the next process and no work to be done.
Waste of handling: It is a kind of action that does not produce additional value, and the work that does not produce value belongs to waste. The main phenomena of waste in handling are: manual handling of production materials from warehouse to workshop, handling of semi-finished products in the previous and next processes, handling in the processing process, etc. Factory layout, excessive or premature production, inventory transfer, plan change, etc. are the main reasons for handling waste.
Waste of defective products: repair, rework and scrapping of products are regarded as waste of defective products. In the production process of products, any nonconforming products will cause waste of materials, equipment and labor. Any repair, rework and scrap are additional costs. If the defective products are not effectively controlled, customer complaints or returns will be caused, or the delivery date will be missed, and serious problems will lose customer confidence. The main reason for the waste of defective products is that people are busy fighting fires, rather than effective prevention. At the source of production, unqualified raw materials and semi-finished products shall be prevented from flowing into the next production process.
Action waste: frequent taking, excessive bending, long walking distance, frequent walking back and forth, looking for tools or materials, repeated correction of alignment accuracy, repeated inspection of products, and other repetitive and unnecessary actions, which cause unnecessary consumption of time and physical strength. If the design of process flow, operation specification, auxiliary tools, PCB equipment layout, etc. is reasonable, many actions can be omitted.
The waste of processing is also called the waste of excessive processing: the waste of processing has two meanings, the first is redundant processing and overly accurate processing. The second aspect is redundant operation time and auxiliary equipment. For example, QC in the forming production process has measured the external dimension once, and PQC in the quality department has repeated the measurement again, which is a waste of processing. In order to achieve the same operation purpose, some processing programs can be omitted, replaced, reorganized or merged. Such redundant processing programs are a waste of processing. Long manufacturing cycle, reduced production efficiency, frequent classification, testing, inspection, and additional processing are the main reasons for processing waste.
Waste of inventory: Lean production believes that excessive production and excess inventory are the biggest waste, and excessive production is ultimately reflected in excess inventory. The inventory of raw materials, equipment accessories, semi-finished products and finished products will not generate any added value, and will increase operating costs. Inventory items not only occupy space, but also increase labor management costs. There are many reasons for inventory waste, such as the complexity of products, inefficient processes, unbalanced production plans, poor market forecasting and management, unreasonable incentive system and other factors will cause excessive production or excessive inventory waste.
Excessive (early) manufacturing waste refers to the production and early production exceeding the necessary quantity: due to excessive production, raw materials will be consumed early, manpower and facilities will be wasted, space will be occupied, materials and product handling will be increased, and management costs will be increased. The reasons include pursuing the local efficiency of the production workshop, ignoring the overall efficiency of the factory, blindly overproducing or putting more margin, long process refueling number, unbalanced production plan, excessive equipment and capacity design, and production not according to the plan.
For these seven wastes, PCB production cost management can start from these points:
On site observation method: take the production process as the unit, observe each process section and each equipment on site for 4~8 hours, record the working hours of personnel, equipment use, equipment downtime, material change number time, quality abnormalities, etc., and use on-site video recording and other methods to make a list of seven major wastes according to the results of observation and recording, calculate the equipment turnover rate (or equipment comprehensive efficiency) and personnel work, and find out the waste problem, Then sort out the list of waste problems, and organize project team members to discuss, formulate and implement improvement countermeasures.
Fast type change: record the current process time of each PCB → distinguish between internal and external work → convert internal work into external work → reduce internal work → reduce external work → standardize.
Kanban management: Kanban is used to indicate production and handling, and display production material number, production quantity and other information. Timely arrange the plan, timely produce, reduce the inventory of WIP, and also timely expose problems, such as equipment downtime, quality abnormalities, to achieve the purpose of improvement.
Standardization: operation standards are documented, continuous training is conducted according to the documents, and results are measured and followed up.
There are also some detailed cost control capabilities. For example, for the chemical solution required in the production process, PCB manufacturers usually outsource a certain process to the solution supplier, and negotiate with the supplier about the total price in advance. The supplier is responsible for the specific amount of solution consumed. However, Jingwang will help chemical liquid medicine suppliers save the amount of liquid medicine through the optimization of its PCB board production process, and then the supplier will provide discounts for feedback.