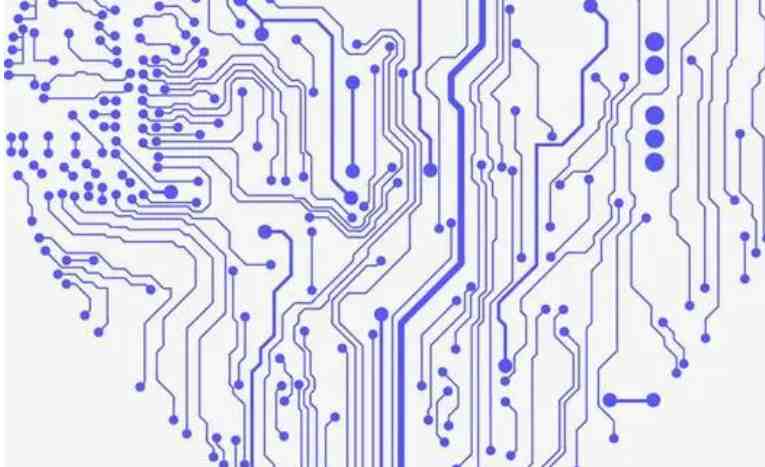
Almost all PCB circuit board maintenance without drawing materials, so many people are skeptical about circuit board maintenance, although various circuit boards vary, but the same is that each circuit board is composed of a variety of integrated blocks, resistors, capacitors and other devices, so the circuit board damage must be one or some of the devices damaged, The idea of circuit board maintenance is established based on the above factors. Circuit board maintenance is divided into two parts: inspection and maintenance, among which inspection occupies a very important position. The basic knowledge of each device on the circuit board is repaired and tested until the bad parts are found and replaced, so a circuit board is repaired.
PCB board maintenance experience
Circuit board detection is the process of finding, determining and correcting the fault of each electronic component on the circuit board. In fact, the whole detection process is the thinking process and the testing process of providing logical reasoning clues, so the detection engineer must gradually accumulate experience in the maintenance, testing and overhaul of the circuit board, and constantly improve the level.
General electronic equipment is composed of tens of thousands of components, in the maintenance, overhaul, if by direct test and check each component of the PCB circuit board to find the problem will be very time-consuming, implementation is also very difficult. So from the fault phenomenon to the fault cause of the type of check, is an important maintenance method. As long as the circuit board has detected the problem, then maintenance is easy. The following is a summary of the circuit board maintenance basic formula, convenient and practical.
A common circuit board, circuit combination tens of millions
The appearance of components changes frequently, and character recognition is the key
Resistive capacitors are the most common, and damage is common
Resistance value is easy to change, capacitance leakage capacity leakage
Inductance transformer is coil, simple test to see through
Diode and audion, measure the PN junction positive and negative
MOS tube and thyristor, trigger test is key
These are discrete parts, integrated circuits for many years
Optocoupler isolation before and after the level, the damage is thousands of millions
Digital devices are often seen, 40 and 74 front
Then there's the analog-to-digital converter, which is a lot of testing
Don't forget ROM and CPLD, burn write to rely on the programmer
CPU, single chip microcomputer, timing judgment logic instrument
All kinds of sensors. Damage rate is number one
The following take a look at the actual case: industrial control circuit board capacitor damage fault characteristics and maintenance
The failure caused by capacitor damage is the highest in electronic equipment, especially the electrolytic capacitor damage is the most common.
Capacitor damage is manifested as: 1. Capacity becomes smaller; 2. 2. Complete loss of capacity; 3. Electric leakage; 4. Short circuit.
The function of capacitor in the circuit is different, and the fault caused by it has its own characteristics. In the industrial control circuit board, digital circuit accounts for the vast majority, capacitors are mostly used for power supply filtering, and less capacitors are used for signal coupling and oscillation circuit. If the electrolytic capacitor used in the switching power supply is damaged, the switching power supply may not vibrate, no voltage output; Or the output voltage filtering is not good, the circuit due to the voltage instability and logic chaos, as the machine working good or bad or can not open the machine, if the capacitor and in the digital circuit between the positive and negative terminals of the power supply, the fault performance is the same as above. This is especially obvious in the computer motherboard performance, many computers with a few years on sometimes can not open the machine, sometimes can boot phenomenon, open the case, often can see the electrolytic capacitor bulge phenomenon, if the capacitance is removed to measure the capacity, found to be much lower than the actual value.
The life of the capacitor is directly related to the ambient temperature. The higher the ambient temperature is, the shorter the life of the capacitor is. This rule applies not only to electrolytic capacitors, but also to other capacitors. Therefore, when looking for the fault capacitor, we should focus on checking the capacitor close to the heat source, such as the capacitor beside the heat sink and high-power components. The closer it is, the more likely it is to be damaged.
I once repaired the power supply of an X-ray flaw detector, and the user reported that there was smoke coming out of the power supply. After opening the case, it was found that there was a large 1000uF/350V capacitor with something like oil flowing out. The capacity of the disassembled capacitor was only tens of uF, and it was also found that only this capacitor was closest to the heat sink of the rectifier bridge, while the others far away were intact with normal capacity. In addition, there is a short circuit of the ceramic capacitor, and it is found that the capacitor is relatively close to the heating parts. So in the maintenance of search should be focused on. Some capacitors leak so badly that they even get hot when touched by fingers. This capacitor must be replaced. In the maintenance of good or bad fault, excluding the possibility of poor contact, generally most of the capacitor damage caused by the fault. So in the event of such a failure, you can focus on checking the capacitor, replacing the capacitor is often surprising (of course, also pay attention to the quality of the capacitor, to choose a better brand, such as ruby, black gold just).