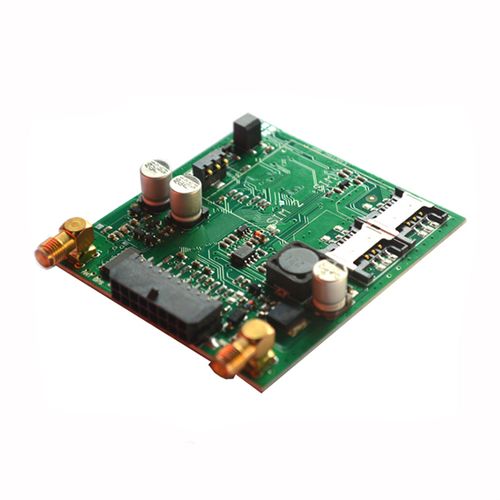
With the rapid development of electronic technology, enhance the continuous progress of printed circuit board technology. PCB board path through single-sided, double-sided, multi-layer progress and improvement, and the proportion of PCB multi-layer board increased year by year. PCB multilayer board is also in high, fine, dense, fine, large and small two extreme progress. One of the closing processes of PCB multilayer board production is lamination, and the control of lamination quality becomes more and more tight in the production of multilayer board. Because of this, to ensure the quality of PCB multilayer lamination, it is necessary to have a better understanding of PCB multilayer lamination process.
For this reason (ipcb) PCB manufacturers based on years of experience in lamination technology, how to increase the lamination quality of multilayer circuit boards in the process technology is summarized as follows:
First, the inner core plate is preset to meet the requirements of lamination
Because of the layer-by-layer progress of laminating machine technology, hot pressing machine has changed from non-vacuum hot pressing machine to vacuum hot pressing machine. The hot pressing process is in a closed system, which can not be seen or touched. Because this requires a reasonable preset of the PCB inner board before laminating, a reference requirement is provided here:
1, there should be a certain distance between the outer size of the core board and the tube unit, that is, the distance between the tube unit and the PCB board edge should try to leave a larger space under the premise of not consuming materials. Ordinary four-layer board requires spacing greater than 10mm, six-layer board requires spacing greater than 15mm, the higher the number of layers, the greater the spacing.
2. The inner core board of PCB circuit board requires no opening, short, open circuit, no oxygen, clean and tidy board surface, no remaining film.
3. The thickness of the core board should be selected according to the total thickness requirements of PCB multilayer board. The thickness of the core board is exactly the same, the deviation is small, and the direction of feeding longitude and latitude is exactly the same, especially for PCB multilayer board with more than 6 layers.
4. The presetting of positioning holes is to reduce the deviation between layers of PCB multilayer board, because it needs attention in the presetting of positioning holes of PCB multilayer board: it only needs more than 3 positioning holes for drilling of 4-layer board. In addition to preset positioning holes for drilling holes, at least five preset nail holes and at least five positioning holes for tool boards used for drilling nails are required for PCB boards with more than 6 layers. However, the higher the number of preset positioning holes, nail holes and tool holes, the more preset holes should be, and the position should be as far away as possible. The main important item is the alignment deviation between the loss layer and layer and to leave a large space for production. The target shape presets are designed to satisfy the requirements of semi-automatic identification of target shape by the target shooting machine. The common presets are complete circle or unified circle.
Two, to meet the requirements of PCB circuit board users, choose appropriate PP, CU foil layout
Customer requirements for PP mainly table now media layer thickness, dielectric constant, special property impedance, voltage resistance, laminate surface smoothness and other requirements, because the selection of PP can be based on the following aspects to select:
1, can guarantee bonding strength and smooth surface;
2. Resin can fill the hole of printed wire during lamination;
3, can supply PCB multilayer board with the necessary thickness of the media layer;
4, can fully eliminate the air and volatile matter between laminates when laminating;
5, CU foil mainly according to the PCB circuit board user requirements for different equipment layout, CU foil quality in line with IPC standards.
3. Inner core plate disposal process
When PCB multilayer board is laminated, the inner core board should be disposed of. The treatment processes of the inner plate include black oxygenation treatment and brown oxygenation treatment. In the oxygenation treatment process, a black oxygenation film is formed on the inner copper foil, and the thickness of the black oxygenation film is 0.25-4). 50mg/cm2. Brown treatment process (level brown) is the formation of an organic film on the inner layer of copper foil. The effect of inner plate disposal process is:
1. Increase the specific appearance of the contact between the inner copper foil and the natural resin, so that the bonding force between the two is strengthened;
2, make the multi-layer circuit board in the wet process to increase acid resistance experience, prevent magenta circle;
3. Prevent the decomposition of a nutrient of the curing agent dicyandiamide in the liquid natural resin under high temperature on the copper surface;
4, increase the flow of molten natural resin on copper foil tube wet wetting, so that the flow of natural resin has sufficient experience to extend the oxygen film, solidified after showing a strong grip.
Four, the organic matching of laminating parameters
The control of PCB lamination parameter mainly refers to the organic matching of lamination "temperature, pressure and time".
1. Temperature
There are several temperature parameters in the lamination process. That is, the melting temperature of natural resin, the curing temperature of natural resin, the setting temperature of the hot plate, the actual temperature of the material and the speed change of heating. The melting temperature is the natural resin begins to melt when the temperature rises to 70. It is because of this further increase in temperature that the natural resin melts further and begins to flow. In the temperature of 70-140 this period of time, natural resin is easy to fluid, it is because of the fluidity of natural resin, to ensure that natural resin filling, moist. As the temperature gradually rises, the fluidity of natural resin experiences a change from small to large, and then to small. Finally, when the temperature reaches 160-170, the fluidity of natural resin is 0, and the temperature at this time is called curing temperature.
In order to make the natural resin can be better filled, wet and moist, the heating efficiency of the choke must be very tight. The heating efficiency is the embodiment of the laminating temperature, that is, when the temperature of the choke rises to how high. The temperature rise efficiency is a close parameter of PCB lamination quality, and the temperature rise efficiency is generally 2-4 / MIN. The heating efficiency is closely related to the different types and numbers of PP.
For 7628PP, the heating efficiency can be faster, that is, 2-4 / min; for 1080 and 2116PP, the heating efficiency can be limited to 1.5-2 / MIN. At the same time, a large amount of PP, and the heating efficiency can not be too fast. Due to the fast heating efficiency, the wet and wettability of PP is poor, the natural resin has large fluidity, and the time is short, which is easy to lead to sliding plate and affect the lamination quality. The temperature of the hot plate is mainly determined by the thermal conductivity of the steel plate, steel plate, cow paper, etc., which is generally 180-200.
2. Pressure
The pressure volume of PCB multilayer board is based on the basic principle of whether natural resin can supplement the empty space between layers and exhaust the gas and volatile matter between layers. Because the hot press is divided into non-vacuum press and vacuum hot press, because the pressure from the start has a section of increasing pressure, two sections of increasing pressure and several sections of increasing pressure. Ordinary non-vacuum presses are used as appropriate to increase the normal pressure and secondary pressure. The vacuum pump considers it appropriate to use two-stage and multi-stage pressure increases. For high, fine and fine multilaminates, it is generally considered appropriate to use multiple sections to increase pressure. The pressure volume is generally confirmed according to the pressure parameter provided by the PP supplier, which is generally 15-35kg/cm2.
3. Time
The time parameter mainly includes the choke of laminating pressure increase opportunity, the choke of heating opportunity, gel time and so on. For two-stage laminating and multi-stage laminating, the chance of controlling the main pressure and the change time from the initial pressure to the main pressure are the key to controlling the laminating quality. If the main pressure time is given too early, it will cause the extrusion of natural resin, glue flow is very much, resulting in the lack of glue, thin plate, and even skateboard phenomenon. If the main pressure is given too late, it will lead to weak laminating bond interface, empty, or there are insufficient bubbles.