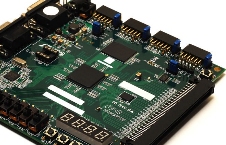
Rigid and flexible bonded boards are not ordinary circuit boards. The process of combining thin layers of flexible and rigid substrates and then laminating them into individual components presents extraordinary challenges and opportunities. When designers started designing their first rigid flexible printed circuit board (PCB), they found that most of what they had learned about PCB design was problematic. Their design is no longer a flat bottom layer of second space, but a three-dimensional interior line that can be bent and folded. I dare say it will be a more powerful PCB. The designer of rigid and flexible composite board uses a single component instead of multiple connectors, multiple cables and strip cables to connect to composite printed circuit boards, which has stronger performance and higher stability. They limited the design to a single component, optimizing the available space by bending and folding the lines like a paper folding swan.
On paper, the "flexible circuit" feels like an alternative to multi-wire ribbon cables. Above the flexible plane substrate is the circuit layer, which is connected to each other end to end. This type of connection is often seen between the print head and the control panel on inkjet printers. In flexible circuits, this continuous flexibility is called "dynamic flex". In dynamic flexible applications, flexible circuits are often (but not limited to) single panels, with the aim of achieving the best results and the strongest reliability. In interconnections between subsystems, such as connecting print heads to control panels, flexible circuits are preferable.
During the life of a flexible circuit, it must be bent, folded and assembled with minimal deflection, which is called "flex-to-install". Depending on the needs of the application, there are several types of flexible installation structures, from single layer to multi-layer. The limited deflection during the life cycle helps to limit the stress on the conductor and to make more layers.
During flexible installation, if single-sided module installation is required, the treatment strategy is to position and laminate rigid materials into the flexible circuit to reinforce specific areas. This flexible circuit design is called "rigidized flex". Rigid materials (usually FR4) do not contain conductors and are used primarily to strengthen the base or connection area of the element. Rigid pliable plate has the advantages of flexible circuit and rigid material, but the cost is relatively high. Rigid and flexible binding plates can be used as substitutes for rigid and flexible binding plates. Rigid materials do not need to be etched or plated, only drilled and added according to the circuit, which can reduce the processing time of printed circuit boards.
In the flexible installation process, if a double-sided module installation is required, or an ultra-thin printed circuit board is required, then choosing a combination of soft and hard board may be the only feasible solution. Rigid and flexible bonded board has both rigid layer and flexible layer, is a multilayer printed circuit board. A typical (four-layer) rigid-flexible PCB has a polyimide core covered with copper foil on both sides. The outer rigid layer consists of single-sided FR4, which are laminated into both sides of the flexible core to assemble the multilayer PCB. Rigid adagio is widely used, but the processing time of rigid adagio is longer and the production cost is higher because of the mixed use of various materials and production processes. The processing technology of flexible layer is completely different from that of outer FR4 layer when making multi-layer rigid and flexible bonded plate. Layers made of different materials must be brought together by lamination, then drilled and electroplated. As a result, it can take five to seven times longer to make a typical four-layer rigid PCB than a standard four-layer rigid PCB.
Application of rigid and flexible bonded plates
Rigid and flexible panels are often found in consumer electronics, such as digital cameras, camcorders and MP3 players. It can also be used in high-end airborne weapon navigation systems. According to research, rigid flexible bonding plates are most commonly used in the manufacture of military aircraft and medical equipment. Rigid and flexible bonding panels have been of great benefit to the design of military aircraft, as they improve connection reliability while also reducing weight. Of course, the benefits of overall smaller size cannot be ignored. Implantable medical devices, such as pacemakers and cochlear implants, also benefit from the ability of rigid and flexible binding plates to bend and fold in tight Spaces, greatly improving reliability. Imagine what it would be like if a pacemaker didn't work because the wires attached to the battery had come off. Using stiff-flex bonding plates, the battery can be connected directly to the circuit layer and can be installed anywhere in the component.
Designers in the field of rigid and flexible composite boards choose rigid and flexible composite boards as the first choice, because it is the only way to achieve product goals. They may use rigid designs as prototypes to test their design ideas, and then use rigid and flexible plates to create new products.
The infrared system will be mounted on a micro-aircraft or unmanned aerial vehicle. The system needs to cover the monitoring range of a 5-cubic-inch handheld digital camera with a payload of up to 3 ounces. That's 50 percent less space and 95 percent less weight while maintaining the original level of functionality and reliability.
One of the biggest challenges is getting the total weight down from three pounds to under three ounces. The only solution was to remove the rigid PCB components connected by multiple connectors and switch to rigid and flexible bonded boards. I met Jeff early on in the design process. Although it was his first time using rigid and flexible plates, he did well at every step. During the production process, he outsourced the PCB design project to an experienced rigid-flexible board application designer and got the PCB manufacturer involved early in the morning.
Although rigid and flexible panels cost more than traditional rigid and flexible panels, they provide an ideal solution for this project. Instead of connecting multiple PCBS, we are using interconnections of flexible substrates. This is the key to reducing space and weight, which is exactly what we need.
Due to the flexible and flexible nature of the rigid and flexible plates, they can be used to create custom circuits to maximize the available space in the interior. Jeff used this to reduce the total system footprint. Since this design will not be mass-produced, although the production cost is higher, the revenue is still higher than the cost by comparison.
Design considerations
The characteristics of manufacturing process and the diversity of materials used must be considered when designing rigid and flexible bonded plates. A designer cannot simply create a typical circuit type for a four-layer rigid PCB and hope to achieve the same effect as a rigid adagio. Because the dimensional stability of polyimide is more than 3 times worse than that of ordinary FR4. Once the copper is etched away, the flexible material will shrink significantly. Most manufacturers understand this property of the material and accurately estimate the situation, so when PCBS enter the machining process (drilling and on-line addition), they try to get the board close to the dimensional tolerance. If the designer does not consider possible manufacturing problems, it is likely that at the last minute he realizes that the design must be updated to accommodate the manufacturer's special processing process.
For optimal results, consider maximizing the minimum ring hole for plating through holes on the flexible layer, and ensure that all wire-to-pad and wire-to-trace nodes add teardrops. If a flexible inner layer is to be used to connect areas of a rigid circuit, careful consideration must be given to support floating rigid areas of the board during the manufacturing process, as areas of the rigid layer are removed to expose the flexible layer underneath. But removing too much rigid material can make the board brittle.
We usually press flexible layers because stamping is more suitable for thin polyimides. Areas on the flexible layer can also be removed, thereby reducing contact with the wiring points in the final wiring. These "layer-free" areas must be considered in the design tool. In addition, wiring and/or component-free areas may not need to be placed in the design to prevent certain components or lines from hanging over the edges of rigid areas.
Design suggestions Because flexible circuits can be bent and folded, bad circuits are avoided, which increase the likelihood of conductor breakage. Here are some suggestions for reducing conductor pressure in the bending region:
1. Wire through the bending area perpendicular to the curved crankshaft
2. Keep the circuit chamfer, width, and hole path outside the bending area
3. Use grid copper instead of solid copper
4. Cross-beaming side-by-side wiring of adjacent layers, "I-Beaming"