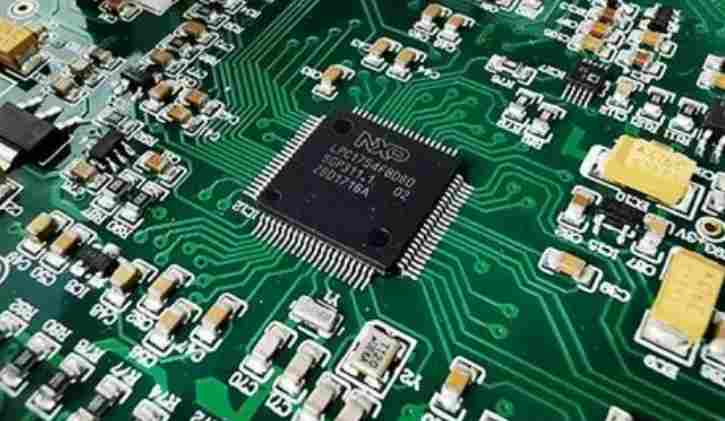
Optical module PCB and optical device simulation belongs to a small branch of high speed serial data link simulation, which involves relatively few things. Generally, as long as you can practice a solid optical module simulation example, no matter QSFP28 or CFP2, Other types of module simulation can deal with, after all, the module inside the things are much the same. It should be noted that the simulation design of optical devices to photoelectric conversion (EO\OE), how to accurately reproduce this conversion process in simulation, requires some experience accumulation.
Saifu circuit specializing in the production of PCB multilayer board, HDI board, soft and hard combined board, optical module PCB board.
Optical module PCB and optical device simulation belongs to a small branch of high speed serial data link simulation, which involves relatively few things. Generally, as long as you can practice a solid optical module simulation example, no matter QSFP28 or CFP2, Other types of module simulation can deal with, after all, the module inside the things are much the same. It should be noted that the simulation design of optical devices to photoelectric conversion (EO\OE), how to accurately reproduce this conversion process in simulation, requires some experience accumulation.
The following figure summarizes the knowledge to be mastered in the cascaded simulation of optical module PCB and optical device, which is mainly divided into three parts. The first part is the knowledge of software operation. Although there are not many things in the simulation, there are five software used. The second is about PCB (including FPC) simulation content, mainly PCB import and cutting simplification, as well as PCB common impedance discontinuity structure optimization simulation; The third is the simulation of optical devices, mainly evaluating the EO and OE response bandwidth of devices, eye map, etc. "Improving the performance of devices by using chip peripheral packaging" is a very important idea in this section.
First, let's take a look at the 5 software used in simulation, which are respectively HFSS, HFSS 3D Layout, Q2D\Q3D and circuit simulator, covering electromagnetic field and circuit analysis software. Field and path co-simulation has become a very popular trend. It is recommended that you upgrade to the latest version of the software, as the new version of the software has introduced many important features such as directly using the S-Parameter model in HFSS, PAM4 emulation support, broadband scanning support, etc. The function of the software is not introduced, there are a lot of online information, in the process of simulation, to flexibly cross the use of these several software, save modeling and solving time, and then reduce their workload.
Second, as for the simulation of optical module PCB, as long as you can master the optimization simulation of the following 7 basic interconnection structures, you are off. The next task is to make calibration test plate, to improve the accuracy of your simulation model.
Thirdly, the simulation of optical devices, the most important thing is to get the equivalent circuit model of the chip. Without this model, the simulation of devices will lose its soul. With this model, all the package S parameters related to high frequency in the device can be extracted for cascade simulation observation eye map and bandwidth. Of course, you can also import hfss or Q3D model directly, without additional extraction of S parameters. Again, packaging can sometimes have a big impact on performance, so pay special attention to the design of the peripheral packaging. In addition, the simulated response bandwidth should be flat, without too large ripple, and a good bandwidth must correspond to a good eye map, and vice versa, if not, it is certain that the simulation model can not be used bit.
The above is the knowledge that optical module PCB and optical device cascade simulation need to master. Compared with chip packaging and board level PCB, there are a lot less things, and because there are a lot of repetitive things in optical module simulation, it is necessary to gradually accumulate the frequently used models and turn them into their own general models, and then simulate them. It is only necessary to adjust as it is used. There is no need to repeat the last simulation work each time, the following is some personal simulation model classification, for reference.
passive channel simulation usually takes up most of the working time. We will start with passive simulation to introduce the basic process of using ANSYS AEDT to simulate optical modules. Pure passive simulation is mainly to optimize and extract the impedance discontinuous structure, packaging, PCB routing S parameter, adjust the channel impedance, the ultimate goal is to make the channel reflection and crosstalk minimum, the bandwidth is large enough.
The simulation of passive channel is divided into pre-layout simulation and post-layout simulation. Please refer to the red and black arrows below to indicate the direction, which all start from PCB import. Pre-layout simulation is in HFSS 3D layout. Each impedance discontinuous structure (goldfinger, through hole, coupling capacitance, interface of pcb and fpc, etc.) is cut out, and then exported to HFSS for local optimization. After optimization, the corresponding structural size parameters are directed to layout engineer for modification of PCB. Here, why not directly optimize 3D layout in HFSS, because 3D layout drawing ability is relatively weak, although some variables can be set parameterized, but far less convenient optimization than in HFSS, so local optimization is recommended to be carried out in HFSS. Simulation of other optical devices and high-speed submounts also needs to be performed in HFSS.
However, I suggest that the post-layout simulation be completed directly in 3D layout. Of course, HFSS can also be used to cope with this work, but it is relatively tedious to guide and export the model again. In 3D layout, after cutting out the net to be analyzed, you can import 3d component. QSFP28 connector, SFP+ connector and SMA connector are common on optical mode. In this way, the simulation of the whole passive path can be carried out. And the use of 3d layout of phi mesh, mesh division can save a little time, after all, layout simulation, the model is relatively large, more than 300,000 grid number is very common.
After the passive simulation performance adjustment, it is necessary to carry out the cascade simulation of the whole TX and RX channel, which belongs to the active simulation. It is necessary to observe the voltage, current waveform, eye diagram and EO/OE response bandwidth of the channel. The following is the overall simulation summary diagram of the DML model emission channel, and there are some details to be carefully handled. Please refer to the caption in the image below.
The above is the overview of optical module PCB and optical device simulation. There are not many things to simulate, but there are also many places to be carefully handled. The above content is just a summary of my personal experience, please forgive the mistakes, thank you!