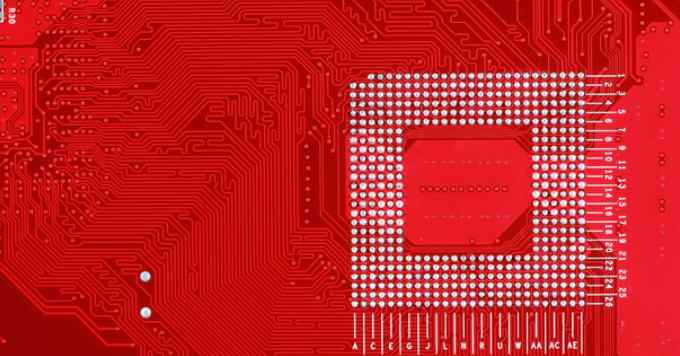
There are many kinds and numbers of holes and complex shapes of single-sided paper substrate and double-sided non-metallic holes of epoxy glass cloth substrate.
Punching: large production batch. Usually use one or several die punch.
Contour processing: Printed boards are produced in large quantities for single and double panel contour, usually by die stamping. According to the size of the printed board, it can be divided into upper blanking die and falling die.
Composite processing: printed board holes and holes, holes and shapes between the requirements of high precision, at the same time in order to shorten the manufacturing cycle, improve productivity, the use of composite die processing single panel holes and shapes. The design and processing of moulds is the key to processing printed boards with moulds, which requires professional technical knowledge. In addition, the installation and debugging of moulds are also very important. At present, most of the moulds of PCB manufacturers are processed by outside factories.
Notes for mold installation:
Select the punch (including type and tonnage) according to the punching force, the size of the die and the closing height calculated by the die design.
Start the punch, a comprehensive check including the clutch, brake, slider and other parts are normal, the operation mechanism is reliable, never impact phenomenon.
The pad iron under the die, usually 2 pieces, must be ground out at the same time on the grinder, to ensure that the die is installed parallel and vertical. The interposition of the pad is not to obstruct the blanking while being as close to the center of the mold as possible.
Several sets of platen and T-head platen screws are to be prepared for use in accordance with the mold. The front end of the platen should not touch the straight wall of the lower die. Emery cloth should be placed between each contact surface, and screws must be tightened.
During mold installation, pay great attention to the screws and nuts on the lower die not touching the upper die (the upper die falls and closes).
When adjusting the mold, use manual rather than manual.
In order to improve the blanking performance of the substrate, the paper substrate should be heated. Its temperature is better at 70 90 ℃.
The hole and shape of the die punching printed board, its quality defects are as follows: the hole around the bulge or copper foil warping or stratification; There are cracks between holes; The hole position is skewed or the hole itself is not vertical; Large burr; Rough section; Printed boards warped in the shape of POTS; Jump on scrap; Clogged with waste materials. The inspection and analysis steps are as follows: check whether the punching force and rigidity of the punch are enough; Mold design is reasonable, rigidity is enough; Convex, concave die and guide column, guide sleeve processing accuracy is reached whether the installation is concentric, vertical. Whether the fit gap is even. Convex and concave clearance is too small or too large to produce quality defects, mold design, processing, debugging, use of the most important problem. Convex and concave die edge is not allowed to round, chamfering. The punch is not allowed to have taper, especially when punching either positive or inverted cone is not allowed. Production should always pay attention to convex, concave die edge wear. Discharge port is reasonable, low resistance. Pushing plate, punching rod is reasonable, enough force. The thickness of the blanked sheet and the binding force of the substrate, the amount of glue, the binding force with copper foil, thermal humidity and time are also factors to be considered in the analysis of blanking quality defects.
Hole and shape processing can be used die blanking method, printed board material. For the processing of simple PCB or not very high requirements of PCB can be used punching way. It is suitable for the production of low level and large batch PCB and PCB whose appearance requirement is not very high, and its cost is low.
There is a composite plate, the upper and lower layers are 0.06mm aluminum alloy foil, the middle layer is a pure fiber core, the total thickness is 0.35mm. It is not difficult to see that this structure and material can meet the requirements of printed board drilling plate, used for high-quality multilayer plate plate, compared with aluminum foil its advantages are: high quality drilling, high precision hole location, due to wear small drill life, at the same time, the external force of the plate to return to the original shape is much better than aluminum foil, weight is much lighter, especially suitable for drilling holes.
The lower cushion board used in China has phenolic paper board, cardboard, wood chip board. Cardboard is soft and easy to produce burrs, but the uniform texture is not easy to break the bit and bite the bit, but the price is cheap, can be used in thin copper foil or single panel. The wood chip board has poor texture uniformity and better hardness than paper board. However, burrs will occur if the copper foil of the PCB is larger than 35 microns when drilled. I have tried to use this board to drill dual panels of 70 micron copper foil, but all the results failed. Phenolic paper board hardness is the best uniformity between the former two, the use of the best effect but more expensive and not environmentally friendly.
There is also a composite bottom plate abroad, the upper and lower layers are 0.06mm aluminum alloy foil, the middle layer is a pure fiber core, the total thickness is 1.50mm. Of course, the performance is very outstanding and environmental protection, much more than phenolic paper board, especially when drilling multilayer board and small diameter holes can fully reflect its advantages, the disadvantage of course is expensive.