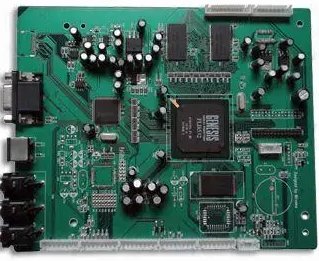
What is HDI
The English abbreviation of HDI (High Density Interconnection) high density interconnection PCB is the abbreviation of multi-layer buried/blind hole PCB produced by laser drilling, horizontal/vertical PTH wet process and other processes on the basis of traditional multi-layer circuit board manufacturing technology, through high-density micro wiring and micro through hole technology.
As defined in IPC-2226:
The diameter of blind hole or buried hole is ≤ 0.15 mm [0.00591 in], and the diameter of disc is ≤ 0.35 mm [0.0138 in]. The conductive coating is formed by laser or mechanical drilling, dry/wet etching, pattern transfer, and electroplating.
Remarks: refer to the through hole in this standard for hole diameter > 0.15 mm [0.00591 in].
HDI common PCB drilling size range:
3-5 mil, the median value of 4 mil is generally used for design and production.
IPC standards commonly used by HDI
1) IPC/JPCA-2315 High Density Interconnection Structures and Microholes Design Guidelines
2) IPC-2226 - High Density Interconnection (HDI) Printed Circuit Board Design Criteria
3) IPC/JPCA-4104 - Specification for Verification and Performance of Dielectric Materials for High Density Interconnection (HDI) Structures
4) IPC-6016, Specification for Verification and Performance of High Density Interconnection (HDI) Structures
Processing principle of HDI blind hole:
Non mechanical drilling, blind hole with hole diameter less than 0.15 mm (6 mil) and pad at the bottom of blind hole less than 0.25 mm (10 mil), is specially called Microvia micro guide hole or micropore.
Microholes are usually processed by laser, and the light types mainly include infrared light and ultraviolet light.
There are two common LASER excitation methods:
One is UV light, the other is sealed CO2 gas
By using infrared heat energy, when the temperature rises or the energy increases to a certain extent, such as the melting point, burning point or boiling point of organic matter, the interaction force or binding force of organic matter molecules will be greatly reduced to make organic matter molecules separate from each other into free or free states, and organic molecules will escape or burn with oxygen in the air to become carbon dioxide or water gas due to the continuous energy provided by the excitation, Because the laser is processed by an infrared beam with a certain diameter, a micro hole is formed.
The solid-state Nd: YAG ultraviolet laser emits a high-energy ultraviolet light beam. Using its optical energy (high-energy photons), it destroys the molecular bonds (such as covalent bonds) of organic substances, metal crystals (such as metal bonds), etc., forming suspended particles or atomic clusters, molecular clusters or atoms, and molecules, and finally forming blind holes.
Filling method of laser hole:
Advantages of electroplated hole filling:
1. It is conducive to the design of stacked holes and holes on the plate (via on Pad)
2. Improve electrical performance, which is helpful for high-frequency PCB design
3. Contribute to heat dissipation and increase current carrying
4. Plug hole and electrical interconnection are completed in one step
5. The blind hole is filled with electroplated copper for higher reliability
Since the aperture of the radium perforation is smaller than 0.075-0.2mm, the electroplating method is adopted to increase the copper thickness in the hole, so as to achieve the purpose of plugging the hole.
The limit of the thickness to diameter ratio (thickness to diameter ratio) of the plate for hole filling electroplating is 1:1, usually 0.8:1, that is, with a 4mil laser hole, the maximum depth of hole filling is 4mil, and the normal depth is about 3.2mil. It can be seen from the lamination diagram of a typical HDI board that the dielectric thickness of all blind hole layers does not exceed the thickness diameter ratio of 1:1.
Influence of blind hole depression on welding:
Due to the reason of blind hole diameter or through hole thickness diameter ratio electroplating hole filling (hole structure), as well as the basic principle of electroplating additives, the Dimple value is inevitable. Since the blind hole involves the subsequent PCB welding process, there are usually different specifications for the Dimple value, which is generally required to be ≤ 15um.
The first batch of samples meets the Production requirements.
The second batch of samples obviously exceeded the standard.
If dimlpe on blind hole disc exceeds the standard, as shown in the figure below, BGA solder ball will produce a hole during welding.
Holes in the plate and blind hole pads have large depressions, which are easy to produce cavities and bubbles during welding.
If the PCB pad is not in the middle of the solder joint, it will cause one side of the PCB solder joint to crack. This is where the defects occur, especially after aging and vibration tests.