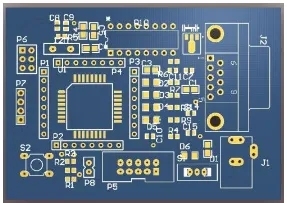
The Aspect Ratio of PCB Design and Its Importance to Multilayer PCB
During the manufacturing process after PCB design, you may be one of the few skilled people who are faced with the challenge of incorporating vias in the entire design. Although you will soon benefit from adding this technology to the layout of the circuit board, there will inevitably be some obstacles that you must overcome in advance, but this is life.
The aspect ratio plays a crucial role in the manufacturing process of aspect ratio PCB, so it should not be taken lightly. If they are ignored, they may leave broken circuit boards, and it is almost impossible to form proper connection points for through-hole coating or even electronic component placement.
Basis: vias before PCB aspect ratio
Before discussing the aspect ratio, let's step back and review what PCB through-hole and torus are and why they play an important role in the design.
Through hole is a hole drilled on the routing lines of each layer of the printed circuit board, whose sole purpose is to connect to another routing line on another layer. They usually exist in HDI multilayer PCB, and each layer is required to be connected in one way or another. There are several variations of blind holes, buried holes and through holes.
Blind hole: They connect the outer layer of the printed circuit board to the inner layer of the circuit, but can't go any further. Therefore, if we have a four layer printed circuit board, the first two layers will drill a hole in the routing, but the third or fourth layer does not.
Buried holes: These holes connect two or more internal layers. Similarly, in our four layer PCB board, the second and third layers will have a hole drilled and connected, while the outer layers of the first and fourth layers will not show any holes, but will only be like blank points on the board.
Through holes: As you have now deciphered, these holes are actually drilled on the entire board connecting the entire external first and fourth layers (or other combinations connecting the four layers).
After these vias are correctly designed into the circuit board, it is now time to drill through the location of each vias. Enter the ring. The annular ring is a copper ring left around the drilled part of the through-hole. It provides us with a connection surface where components can be installed or filled, thus providing us with beautiful plated through-hole. The larger the ring, the larger our connecting surface. This is a simple but critical part of the manufacturing challenge.
The aspect ratio will affect your routing position
Sweet, sweet aspect ratio
The aspect ratio of a PCB board is simply defined as the ratio of the thickness of the board to the diameter of the drilled through hole. This is an important ratio because it affects the plating in the through-hole (also affected by the ring).
Suppose your board is 0.2 inch thick and the through hole diameter is 0.02 inch. The aspect ratio will be 10:1. With the increase of this ratio, more plating will surround the through-hole compared with the internal drilling part, so there is a greater risk of cracking due to z-axis expansion during welding. Maintaining a low PCB aspect ratio will ensure uniform plating throughout the vias and provide higher strength throughout the life of the printed circuit board.
Most PCB manufacturing workshops can achieve a length to width ratio of 6:1. The minimum actual drill hole diameter is about 0.013 "floating, so the maximum plate thickness is about 0.078".
When considering reducing the aspect ratio, both the thickness of the plate and the minimum drill diameter should be considered, which may save you a long and confusing manufacturing problem. In addition, your through-hole will be stronger and provide you with more connection space to install components on it. PCB processing and PCB Assembly plants explain the aspect ratio of PCB design and its importance to multi-layer PCB.