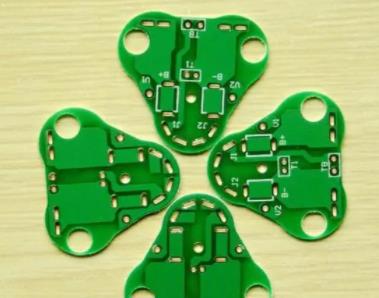
Design Skills of High Frequency PCB in Embedded System
Today's high-speed embedded systems combine various functions, components, digital interfaces, and of course, wireless/RF signaling. If you want to design an embedded system with any computing power, and also include an analog front-end, you will face multiple mixed signal design challenges. Whether it is a simple radio connection below 1 GHz, Wifi/BLE or Gigabit Ethernet, embedded systems need some way to interact with the outside world, and this way does not depend on pure digital signaling. This applies to backplane, single board computers, IoT products and other systems.
Using the high frequency signals used in today's embedded systems, circuit board designers have the responsibility to solve these problems early in the design process. The successful design of high-frequency PCB can be summed up in three aspects:
Stack design and grounding
Component placement
Wiring and impedance control
It sounds obvious that this is the basic design technique we have introduced in many articles on this blog. However, these points should be emphasized here, because high-frequency PCB with some digital functions, especially modern embedded systems, must rely on success in these three aspects to ensure that the system operates as designed. To help you start the layout and layout of the next PCB, let's look at each area from the high-frequency design of embedded systems.
Design Challenges of High Frequency PCB
As I will briefly discuss, the design challenges involved in high frequency PCB and digital system are all focused on signal integrity, and to some extent, power integrity. The PCB type we are considering here is a board for embedded systems, which will also include some RF functions. The RF part can be realized by standard wireless protocols such as WiFi or BLE, while the digital part can almost interface with MCU, MPU or FPGA.
Isolate high-frequency signal
Perhaps the most important design consideration in these systems is the isolation of digital and analog signals. If the system has an analog part, antenna feeder, etc., it is necessary to isolate the analog part from the digital part, because crosstalk will interfere with the analog signal. This is one of the reasons why waveguide routing is best used because it provides natural isolation, as I will explain in more detail below.
If you can successfully complete this section, you will be closer to producing an analog section with higher EMI immunity in the analog section. As I will discuss below, it is better to start thinking about this in the stacking phase (the beginning of the design) rather than in the cabling phase (the end of the design). First, some characteristics should be considered in the layout design of embedded systems.
What makes embedded technology different?
The difference between embedded system and many other digital systems with high-frequency PCB is the use of high-speed digital interfaces. Although high-speed computing interfaces use differential pairs for data transmission, it is still possible to cause common mode noise (crosstalk) between digital and analog parts. In addition, signals with faster rise times will concentrate their signal power to higher frequencies, so they are more likely to appear as noise on single ended RF interconnects.
Since you are basically dealing with high-speed minicomputers, you also need to consider power integrity, especially ground bounce/track bounce. The two effects are basically the same, but they are displayed in different ways.
The correct PCB stack can solve most power and signal integrity problems. Stacking also affects solubility, distributability, impedance control, EMI/EMC, thermal control, and isolation. If you are designing an embedded system with high-speed digital interfaces and analog parts, you can use the stack to start thinking about your design.
If you are using pure analog or mixed signal equipment, there are many important things to consider in the stacking and grounding plan. However, you must also place the high-speed/high-frequency components on the board, so it is natural to check the placement of the components before starting wiring.
Component placed above top reference plane
First, you should divide the ground plane into digital part and analog part, but keep the two parts physically connected to provide a consistent low reactance grounding path. If you are using frequency RF signals of multiple frequencies, consider cutting a third analog to use for these signals and components. If you stack the ground and power according to the above instructions, you have already done the same for the power part, and ideally, you can prevent multi port excitation caused by high transmission impedance in the PDN.
Separate your digital part and RF part above the ground plane and follow the return path to ensure that the signal is isolated in the PCB layout.
High frequency PCB for isolated wiring
The next point to consider is how to route wires between components. However, you may also need some strategies to isolate different board parts and interconnects to prevent interference. Some strategies include:
The coplanar waveguide wiring on the surface layer, especially the routing between components, to the feeder or to the coaxial connector.
If you have enough layers, consider leaving one layer for ribbon routing. Please pay attention to this, because vias can cause problems on ultra-high frequency (mmWave).
Since two out of phase radiation sources will be generated, placing the grounding through hole fence around the RF power plane can provide good suppression effect.
Consider using bandgap structures to provide isolation, as they can be printed directly onto high-frequency PCBs.
How interconnects are designed to ensure consistent impedance matching is not as important as how they are wired to prevent interference. Perhaps the most important point here is to trace the return path and keep the RF interconnects away from the digital part. As long as there is no large return current near your RF interconnects, you can reduce the concern about crosstalk. However, before prototype design, there are still many points to be evaluated, and the on-site solver can help find these problems.
Evaluate your board before prototyping with a field solver
You can save time and money as long as you can eliminate prototype runs and discover ultra-high frequency signal/power integrity issues. The correct field solver can help you complete the PCB layout and calculate the important signal integrity indicators required to ensure that RF products will work as designed. In high-frequency PCB, some important points to check are network parameters, radiated EMI and interference between different board parts. If you place the antenna directly on the board, you also need to check the radiation pattern and radiation power. PCB processing and pcb assembly manufacturers explain the design skills of high-frequency PCB in embedded systems.