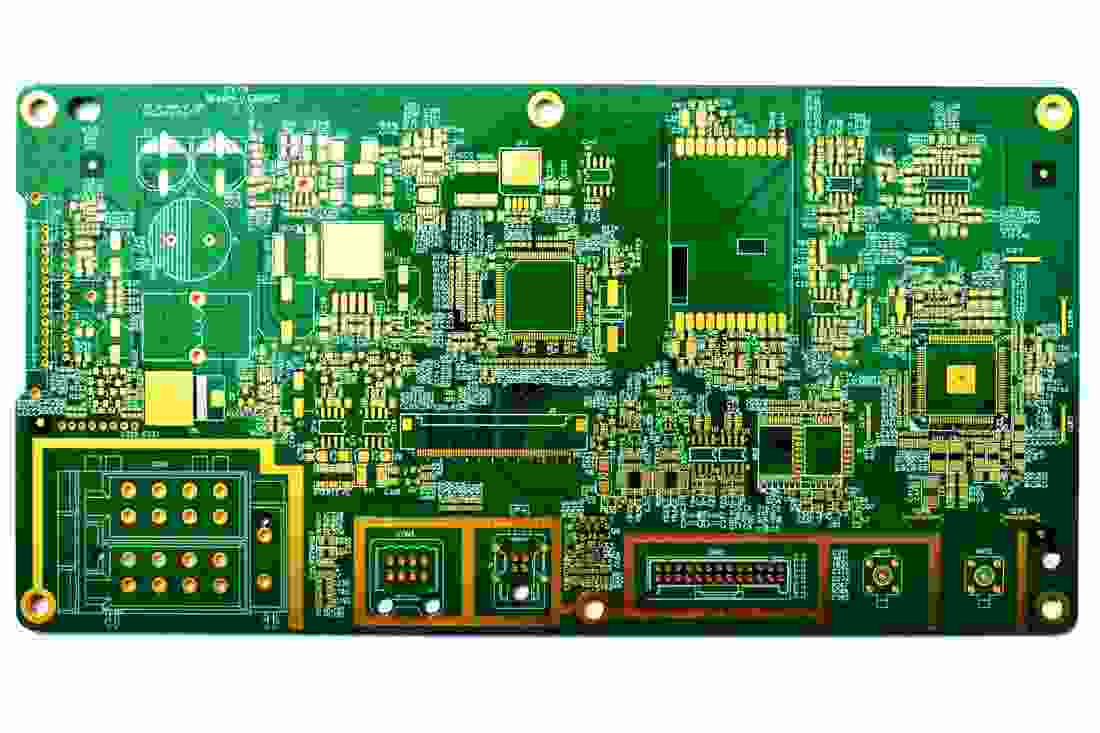
PCB manufacturing shares high temperature PCB design considerations
Printed circuit board (PCB) is an essential electronic device, but sometimes engineers are faced with temperature restrictions, which forces them to think differently. We will give a high-level overview of the design of high-temperature circuit boards, and in this process, we will consider some options that may be given to you in this case.
Material selection for high temperature environment
Before considering the circuit itself, we need to consider the materials that will be made by the manufacturer of the circuit board. Most circuit boards are made of materials called FR-4, a glass epoxy resin laminate that can withstand temperatures of 90 to 110 degrees Celsius. If our environment is lower than this threshold, we can usually order the circuit board like any other design without considering this factor. However, if the application we are designing will experience temperatures above the boiling point of water, we need to upgrade our circuit board to be high temperature resistant FR-4 or polyimide. These upgraded materials can withstand 130 to 260 degrees Celsius, depending on the manufacturer and the specific material type.
In addition, the melting temperature of traditional leaded solder paste is about 160 to 180 ℃, so we need to guide the assembly personnel to use lead-free solder paste. If this is not the case, we run the risk that the component will fall from the literal. Similarly, we should consider certain types of conformal coatings to further protect our design from baking.
Design rules for high temperature environment
Finally, we can start to focus on our design. This is where big challenges begin to surface. Many logic components simply cannot operate at extreme temperatures. Many silicon chips can not work normally in high temperature environment, thus forming useless circuit boards. To ensure that this will not happen, we need to add temperature parameters when searching for components, especially when our design needs to include logic chips or microcontrollers. Most vendor search tools have this option, but far fewer options are available.
After the component is selected successfully, we need to consider the placement location. Generally, when placing our components, we want to keep all the heating components as far away as possible, even under normal circumstances, these components do not have to worry about heat generation. This is because these devices will generate additional heat in the environment. The parts to be considered include voltage regulator, high-power resistor, etc.
Finally, we may want to consider our shell. Although PCB can be designed to fit most environments, in most cases, it is beneficial to modify the housing design to make it insulated, which is very beneficial to us. This cannot replace the design considerations we have discussed, but it should definitely be considered as the first line of defense. Some considerations may include insulation on the inner wall of the enclosure, temperature shielding materials such as titanium and Kevlar, or ABS plastic if not extreme.
High temperature due to element dissipation
Some components require a lot of heat dissipation, so no matter what the environment, we should consider the design rules for high-temperature components. This is a major problem in extensive design, because the implementation of good design will affect reliability and service life.
As in a heated environment, it is best to separate the heat generating components from each other by a certain distance. In general, multiple heated parts may lead to the overall baking of the entire circuit board, which makes it impossible for us to use the equipment. In addition, adequate ventilation is always required. If we put the circuit board in the box, and the parts we choose will generate a lot of heat, then the combination of small fan and heat sink can ease our trouble. The position of the fan is also important because we want the fan to blow cold air onto the radiator blades to dissipate heat, thereby reducing the temperature of the components.
In our entire design, strategically placing through holes can also help cool the parts, thereby cooling them. For example, if we use a flat mount package, you can use multiple vias to attach the thermal mass of the part to the ground plane. By filling these through holes with conductive adhesive, we can obtain higher thermal conductivity. In fact, this turns the entire circuit board itself into a heat sink, eliminating the need for independent circuit boards. Although this is not always possible, for example in most through-hole designs, this technique allows us to reduce costs and reduce line items in the bill of materials. PCB processing and pcb assembly manufacturers introduce PCB manufacturing and share high temperature PCB design considerations.