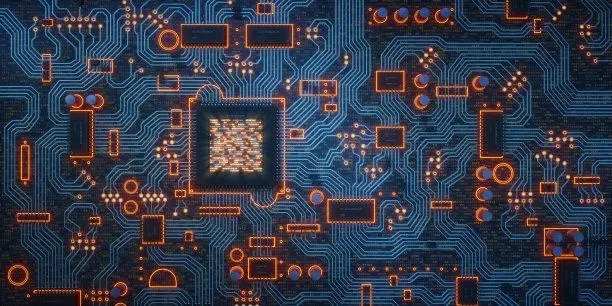
What is multi board design? Create a multi board system
When you use the best PCB design software for your boards, creating a multi board system is much easier. The PCB toolset you need in the design software includes standard electrical utilities and MCAD integration to ensure that your boards fit correctly. In this short guide, we will introduce some basic aspects of defining connections in your design, while also ensuring signal integrity in your design. Whether you use standard rigid multilayer PCB design and layout, or more involved flexible/rigid flexible combination circuit boards, you need some basic design toolsets to ensure that your design works as expected.
Plan your multi board PCB system design
Native 3D PCB design for multi board components
Multi board design starts with a plan for the mechanical profile of each board in the system and how they are connected. Your connection method may involve simple standardized connectors, such as sandwich connector or pin array, or integrated edge connector. Once these points have been identified, a layout and cabling strategy needs to be developed so that components can properly interconnect throughout the design process without creating EMI/EMC, SI/PI, and mechanical vibration issues. Read the following sections to learn how to start high-speed design and the important role of PCB design software.
Plan your multi board PCB system design
Designing multi board PCB layout is a system level design project, which involves defining the connection between all boards in the system. A good process to start layout planning for a multi board PCB system is as follows:
Determine board arrangements: How will the boards be oriented relative to each other? Does the system have mobile elements that need to interact with the board in some way? Mechanical modeling needs to start at this stage and will decide how to design
Select connector: will your circuit board be interconnected with the existing board to board connector, edge connector, flexible tape or cable? You need to select connectors to support the board layout you need while still fitting your enclosure.
Determine the function of the circuit board: Ideally, each circuit board in a multi board system will perform a specific function and should contain only the components needed to support that function. This may force you to reconsider your board arrangement and connector options, so consider this when deciding which functions to place on which boards.
Mapping signals across connectors: Each connector shall support specific signals or signal groups and ensure signal integrity in the design. The pin distribution can be determined at this stage and can be defined on the schematic symbol of the connector.
Start creating schematics: To stay organized, it is best to segment the schematics so that they reflect the arrangement of your boards in a multi board system layout. Each group of schematic diagrams shall only contain components from a single circuit board, and components from different circuit boards shall not be placed in the same schematic diagram.
After creating a schematic for each circuit board in the system, it is time to start creating a physical PCB layout for each circuit board. Follow the standard process of PCB design to import your components into your design and place them around each circuit board. At this point, the connector can be placed in the desired position on the PCB, and the edge connector can be defined on a specific component.
Some multi board PCB designs and layouts will use edge connectors to establish electrical connections between the two boards.
Before starting to route components, it is important to start considering your mechanical requirements and whether you can still put the design into its intended enclosure after the layout is completed. This requires using the enclosure model and each board in the system to ensure that there is no interference and that the boards will be installed together as expected.
Native 3D PCB design for multi board components
Some measurements and modeling are very difficult in 2D, which creates a risk of interference between boards, components, and enclosures. In a multi board PCB design, PCB components involve multiple boards, and there may be unwanted interference between boards in the design or between components, cables and other components in the system. The best way to prevent this is to add mechanical back testing in the design process to ensure that there is no interference.
During the back check, MCAD tools will be used to automatically check the gap in 3D. These tools will check the 3D models of your circuit boards, shells and components. The standard 3D modeling file format in MCAD software and PCB design function is STEP model. By combining STEP models for each component in the design, your design software can create a real model of the circuit board.
If you work with a mechanical designer to build your multi board design, they should provide a model of the PCB housing for the design. It can then be imported into your PCB design software to perform interference checking within your ECAD tool. Another option is to export the STEP model or IDF file of the circuit board, and then import it into the MCAD application for back checking. The standard workflow for enterprise level teams is to have MCAD users perform backtracking checks to verify component placement.
After the initial layout on all boards is completed and interference is checked, the design can be routed. Multi board systems need to take some important cabling considerations for high-speed signals and low-speed digital protocols to ensure signal integrity.
In each circuit board, wiring should be performed after setting the initial design rules, calculating any required impedance curves, and setting the design to the appropriate wiring mode. Although not every circuit board has high-speed interfaces, they can be routed between boards in a multi board system through edge connectors, cables, flexible tapes, or board to board connectors. Slow single ended signals (for example, from GPIO) or bus protocols can also be routed between cables and boards. However, care must be taken to ensure uniform grounding and prevent possible signal integrity problems.
Defining foundations in a multi board system
As in other PCBs, it is necessary to clearly define the grounding in the multi board layout to ensure that the signal can be laid linearly. When routing signal paths between boards, use the following procedure to ensure that a consistent ground potential is enforced throughout the system:
Use the ground plane on each board to provide clear characteristic impedance, provide shielding to suppress EMI/crosstalk, and help provide strong decoupling in the PDN.
When wiring between two boards, a grounding connection is included on the connector to connect the grounding area in each circuit board. This will provide shielding for the connector or cable.
For ribbon or twisted pair cables, consider using staggered grounding between signals to provide clear reference and stronger shielding in the wiring path.
This simple grounding is an important part of signal integrity when connecting and wiring between circuit board designs in a multi board system. This helps to define consistent impedance, return path, and crosstalk suppression in multi board PCB design and wiring. If you follow these steps, you are more likely to maintain the signal integrity of single ended signals when you route between boards and through cables.
When the grounding area of a PCB in a multi board system can be easily bridged through a connector, the two boards will be at the same ground potential, and signals can be accurately read on each side of the connection.
Unfortunately, the topology of some multi board systems cannot provide such grounding connections. This usually happens when the system is physically distributed on multiple cabinets, rather than connecting all boards in the same cabinet. However, sometimes the circuit boards are connected in the same cabinet in the form of daisy chain and provide high power. In this case, the design may cause safety and reliability problems, which can only be solved by differential pair wiring.
Why use difference protocol in multi board design
When wiring on equal length cables in industrial systems, it is better to use differential protocols for wiring. Larger systems with grounding connections between circuit boards, especially in DC systems that can carry high current through grounding, may have potential safety hazards and may lead to cable damage, because cables will emit high heat in the grounding connection.
When shielding is used on larger systems connected to cables, especially in the linear arrangement of series circuit boards, the ground planes in each circuit board should be isolated rather than interconnected. Instead, chassis and ground connections should be used for shielding, not PCB ground plane. Then, in order to route signals between boards, differential pairs should be used because they can adapt to the ground offset between boards in a multi board system.
The main reason for using differential protocols in multi board systems is that they do not require clear grounding references when routing between two circuit boards in the system. Once the differential pair is back on the circuit board and the differential signal is read, the data can be recovered without worrying about the ground offset during wiring. Common differential protocols for cabling between PCBs in multi board systems include CAN bus, Ethernet and RS485. What does the PCB Assembly and PCB processing manufacturer explain about multi board design? Create a multi board system.
Differential pairs are used for longer cable links, especially when shielding cannot be implemented.
When you need to build advanced high-speed digital systems while ensuring signal integrity and power integrity, use the best high-speed design and layout toolset based on the rule driven design engine. Whether you need a single board computer with dense layout or a complex mixed signal PCB, the best PCB layout tools will help you maintain flexibility when creating multi board designs and PCB layouts for each circuit board.