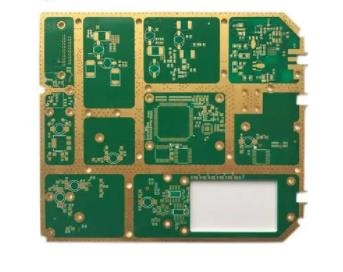
PCB design: PWM introduction in power supply design
Switching mode power supplies use semiconductor switches (usually MOSFETs) to drive magnetic components, usually transformers or inductors. Then the output of the switching power supply circuit is rectified and adjusted to provide DC output. Switching mode power supplies are popular because they are more efficient than non switching power supplies such as linear regulators.
What is pulse width modulation
Pulse width modulation (PWM), also known as pulse duration modulation (PDM), is a technique to reduce the average power of AC signals. Without affecting the fundamental frequency of the signal, effectively truncating part of the waveform will reduce the average voltage. Increasing the voltage "off" time decreases the average voltage, which reduces power.
Use PWM output control
The switching mode power supply must implement a feedback control loop to keep its output voltage within the required limits when the load changes - the output voltage of the power supply is fed back through the error amplifier to provide a control signal. The most common control method is to use pulse width modulation (PWM). Adjust the pulse width of the AC signal at the input end of the power supply to increase or decrease the electric energy, which in turn translates into the change of the voltage at the output end of the power supply. For example, increase the input pulse width, increase the output voltage, decrease the pulse width, and decrease the output voltage. This mechanism provides a closed-loop feedback control of the output voltage. The circuit board assembly, circuit board design and circuit board processing manufacturer explain the PWM introduction in the switching power supply design.
One problem to remember is that typical AC waveforms often have benign rising and falling edges. When PWM control is applied, the rising and falling edges will become more abrupt, especially when the duty cycle is small. Sudden voltage change will produce transient, resulting in electromagnetic noise and large surge current in the circuit. In addition, small errors in the control circuit may be amplified into serious output errors, which may lead to unstable output voltage. The standard solution is to avoid sudden on-off switching of the input waveform, but use slope compensation technology to limit the rate of change.
Peak current mode control (PCMC) technology provides a simple solution for PWM power supply, except for inductor inductor capacitor (LLC) converters that require voltage mode control. When the duty cycle approaches the maximum value, PWM control will always be challenging. It is always preferable to design circuits to avoid this situation than to add additional control circuits to apply slope compensation to prevent output instability.
Design considerations
Transient starting current
One of the disadvantages of switching mode power supply, especially when it is used to isolate the power supply, is that the inductance of the power supply may cause considerable transient current when it is energized. In addition, the initial current is unpredictable; When the inductive element is first energized, it changes with the exact point in the AC cycle.
The control circuit based on PWM can realize the soft start function, which can control the initial power on stage to limit the available energy of the circuit and limit the excitation current until the power supply reaches the steady state condition. Limiting the initial surge current protects the components and reduces noise emissions associated with transient currents.
Overcurrent protection
One advantage of PWM control is that if the output current exceeds a defined limit, the current detection logic can be used to disable the power supply by turning off PWM. This provides an easy to implement overcurrent protection mechanism that automatically resets once the current returns to its boundary.
Managing low loads using pulse frequency modulation
One of the main disadvantages of PWM in switching mode power supply is its inherent low efficiency under extremely low load. Under no-load conditions, the power supply will continue to generate losses due to the power control circuit. This may be a problem for battery powered devices that operate in standby mode for a long time. In this mode, the efficiency of the power supply determines the battery life.
The solution to this situation is to replace PWM with Pulse Frequency Modulation (PFM). Here, the duty cycle of the AC waveform is unchanged, and the power output is controlled by changing the frequency of the AC input. The Circuit board assembly, circuit board design and circuit board processing manufacturer explain the PWM introduction in the switching power supply design.
The main problem with PFM is that the design of noise filtering becomes more challenging because it generates noise over a wider frequency range.
The other problem is that PFM control will generate much larger output voltage ripple than PWM control, and the transient response time may be longer. If the power supply drives components sensitive to voltage fluctuations, especially integrated circuits, these problems will make the task of designers more difficult.
The power supply chip can now provide built-in dual mode PWM and PFM control, which can automatically switch according to the output load. Therefore, by definition, limiting PFM control to low load conditions greatly reduces the impact of adverse effects such as emission noise and voltage ripple.
Managing low loads using pulse skip modulation
Another technique for managing low load conditions is to turn off the PWM waveform for a short period of time, during which time the output voltage is maintained by the output capacitor of the power supply. This process of disabling PWM waveforms is called pulse skip or pulse skip modulation (PSM). Under no-load condition, PWM waveform only needs to be enabled intermittently for a short time to compensate the loss of power supply consuming output capacitor.
conclusion
The main advantages of using PWM are high efficiency, very low power loss, and using very high frequency to optimize the circuit board design. Compared with similar technologies in power supply design, its implementation cost is relatively low, and it can handle high loads. The main disadvantage is the additional complexity required to manage low loads. However, the availability of integrated devices that combine PWM control with automatic low load management simplifies this task for power designers. The circuit board assembly, circuit board design and circuit board processing manufacturer explain the PWM introduction in the switching power supply design.