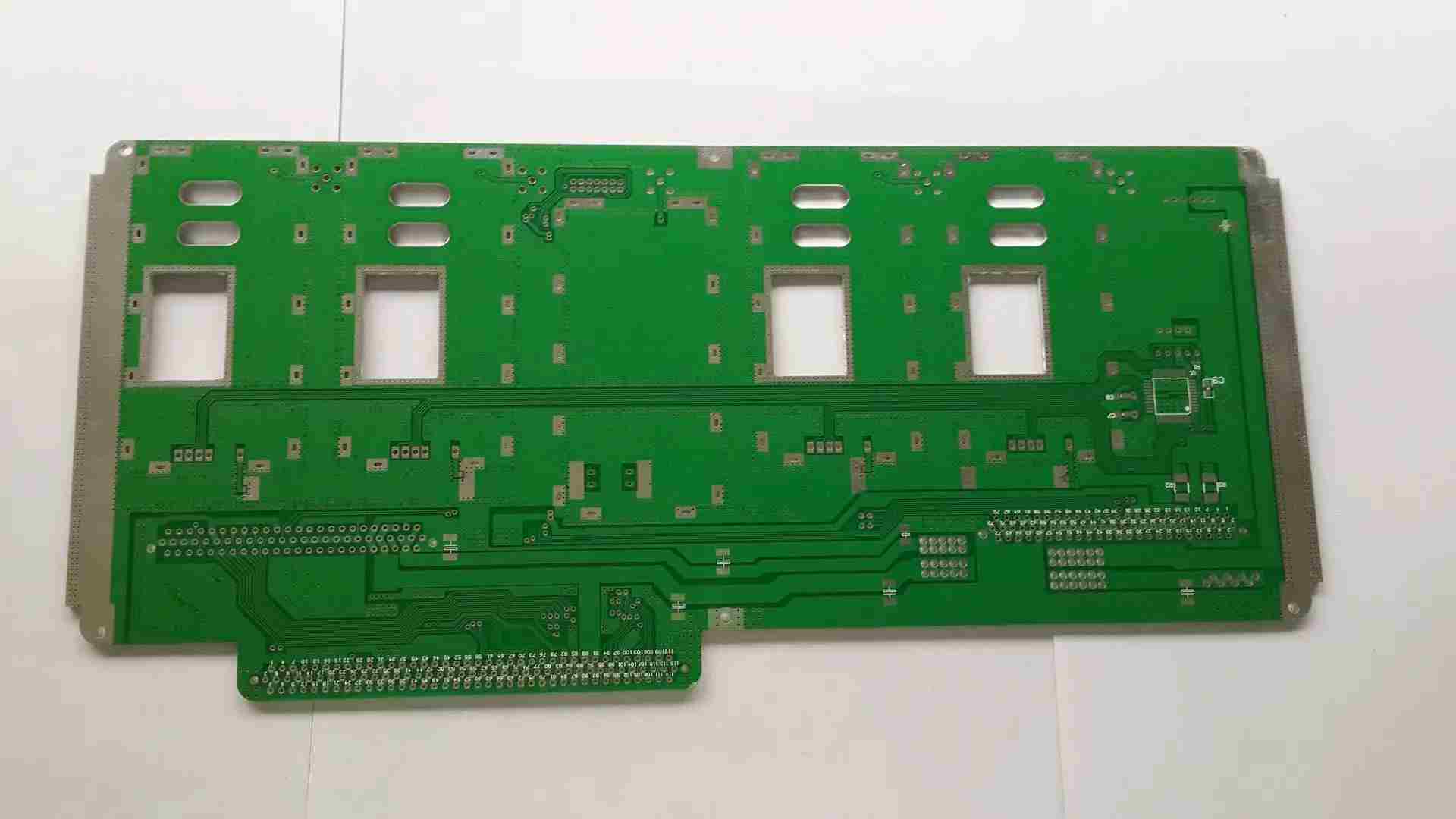
Circuit board factory explains the bypass and decoupling design of electromagnetic compatibility design in circuit board design of designed products
Bypass and decoupling design
Bypass refers to the transfer of unwanted common mode RF energy from components or cables. The main function of bypass capacitor is to generate an AC component, so as to eliminate unnecessary energy entering the sensitive area. Decoupling refers to the removal of RF energy entering the distribution network from high-frequency components during component switching. The main function of decoupling capacitor is to provide a local DC power supply to components, so as to reduce the transmission of switching noise on the board, And guide the noise to the ground.
3.1 Selection of capacitance
When selecting bypass and decoupling capacitors, the autoresonance frequency of the required capacitor can be calculated through the logic series and the clock speed used, and the capacitance value can be selected according to the frequency and the capacitive reactance in the circuit. The SMT capacitor with lower lead inductance shall be selected as the packaging scale as far as possible, rather than the through hole capacitor. In addition, parallel decoupling capacitors are often used in product design to provide a larger working frequency band and reduce the grounding imbalance. In parallel capacitor system, when the operating frequency is higher than the self resonant frequency, the large capacitor shows inductive impedance and increases with the increase of frequency; The small capacitance is capacitive impedance and decreases with the increase of frequency, and the impedance of the whole capacitor circuit is smaller than that of a single capacitor.
3.2 Bypass capacitor configuration
Bypass capacitors are generally used as high-frequency bypass devices to reduce the requirements for transient power supply of power modules. Generally, aluminum electrolytic capacitors and tantalum capacitors are more suitable for bypass capacitors. Their capacitance values depend on the requirements for transient current on PCB boards, generally within the range of 10-470LF. If there are many integrated circuits, high-speed switching circuits and power supplies with long leads on PCB boards, large capacity capacitors should be selected.
3.3 Decoupling capacitor configuration
(1) The power input terminal is connected with 10~100LF electrolytic capacitor. If possible, it is better to connect to more than 100LF;
(2) In principle, each integrated circuit chip should be equipped with a 0.01pF ceramic chip capacitor. If the gap between printed boards is insufficient, a 1~10pF tantalum capacitor can be arranged every 4~8 chips;
(3) For devices with weak noise resistance and large power supply change during shutdown, such as RAM and ROM memory devices, decoupling capacitors should be directly connected between the power line and ground wire of the chip;
(4) The capacitor lead shall not be too long, especially the high-frequency bypass capacitor shall not have lead;
(5) Because there are contactors, relays, buttons and other components in the printed circuit board, large spark discharge will occur during operation, and RC circuit must be used to absorb the discharge current. Generally, R is 1~2K and C is 2.2~47LF;
(6) CMOS has a high input impedance and is susceptible to induction, so the unused end should be grounded or connected to a positive power supply when in use.
4 Design of mixed signal circuit board
Understanding the path and mode of current return to ground is the key to optimize the mixed signal circuit board design. We should not only consider where the signal current flows, but also ignore the specific path of the current. If the ground wire layer must be divided and must be routed through the gap between the divisions, a single point connection can be made between the divided ground to form a connection bridge between the two grounds, and then the wiring can be routed through the connection bridge. In this way, a direct current return path can be provided below each signal line, so that the formed loop area is very small. The following points should be paid attention to in the mixed signal PCB design process:
(1) The PCB is divided into independent analog part and digital part to realize the division of analog and digital power supply, and the A/D converter is placed across partitions;
(2) Do not divide the ground. Lay uniformly under the analog part and digital part of the circuit board;
(3) In all layers of the circuit board, digital signals can only be wired in the digital part of the circuit board, and analog signals can only be wired in the analog part of the circuit board;
(4) The wiring shall not cross the gap between the split power supply planes, and the signal lines that must cross the gap between the split power supply planes shall be located on the wiring layer adjacent to the large area;
(5) Analyze the actual flow path and mode of return ground current;
(6) Adopt correct layout and routing rules.
In a word, with the complexity, high-speed and intensification of electronic products, the design requirements for PCB boards are getting higher and higher, especially the design problems of electromagnetic compatibility are becoming more and more prominent. The key problem to solve electromagnetic compatibility is the reasonable design of power supply, ground, bypass, decoupling and mixed signal circuits.