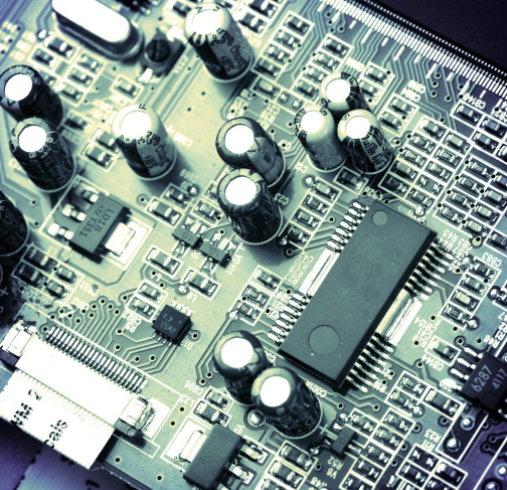
The most complete PCB circuit design check items
After designing PCB, electronic engineers need to conduct a comprehensive check on the rationality of the design. The following checklist covers all aspects related to the design cycle. For special applications, some additional items should be added.
All PCB design drawing inspection items
1) Has the circuit been analyzed? Is the circuit divided into basic units to smooth the signal?
2) Does the circuit allow the use of short circuited or isolated key leads?
3) Are the areas that must be masked effectively?
4) Do you make full use of basic grid graphics?
5) Is the size of the printed circuit board the optimal size?
6) Do you use the selected wire width and spacing as much as possible?
7) Are preferred pad sizes and hole sizes used?
8) Are photographic negatives and sketches appropriate?
9) Do you use the least jump shot? Are jumper wires routed through components and accessories?
Circuit board
L0) Is the letter visible after assembly? Is it the correct size and model?
11) To prevent blistering, is there a window in the large area of copper foil?
12) Is there a tool locating hole?
PCB power characteristic inspection items
1) Has the influence of conductor resistance, inductance and capacitance been analyzed? In particular, is the effect of critical pressure drop reliable?
2) Does the spacing and shape of wire accessories meet the insulation requirements?
3) Is the insulation resistance controlled and specified in key areas?
4) Is polarity fully identified?
5) Is the influence of wire spacing on leakage resistance and voltage measured from a geometric perspective?
6) Is the medium used to change the surface coating determined?
PCB physical characteristics inspection items
1) Are all gaskets and their locations suitable for final assembly?
2) Can the assembled PCB meet the shock and vibration conditions?
3) What is the required spacing for standard components?
4) Are the loosely mounted components or heavier components fixed?
5) Is the heat dissipation and cooling of the heating element correct? Or is it isolated from printed circuit boards and other hot parts?
6) Are voltage dividers and other multi lead components located correctly?
7) Is the layout and orientation of components easy to check?
8) Have all possible interferences on the printed circuit board and the entire printed circuit board assembly been eliminated?
9) Is the size of the locating hole correct?
10) Are tolerances complete and reasonable?
11) Do you control and sign the physical properties of all coatings?
12) Is the diameter ratio of hole to wire within acceptable range?
PCB Mechanical Design Factors
Although the printed circuit board uses mechanical methods to support components, it cannot be used as a structural part of the entire equipment. At the edge of the printing plate, support at least every 5 inches.
The following factors must be considered when selecting and designing printed circuit boards:;
1) The structural size and shape of the printed circuit board.
2) Type of mechanical accessories and plugs (sockets) required.
3) Adaptability of the circuit to other circuits and environmental conditions.
4) Depending on some factors, such as heat and dust, consider installing the printed circuit board vertically or horizontally.
5) Some environmental factors requiring special attention, such as heat dissipation, ventilation, shock, vibration and humidity. Dust, salt spray and radiation.
6) Degree of support.
7) Keep and repair.
8) Easy to take off.
Installation requirements of printed circuit board
The printed circuit board shall be supported within at least 1 inch of the 3 edges of the printed circuit board. According to practical experience, the distance between support points of printed circuit boards with thickness of 0.031-0.062 inches shall be at least 4 inches; For PCB with thickness greater than 0.093 inch, the distance between supporting points shall be at least 5 inches. This measure can improve the rigidity of PCB and destroy the possible resonance of PCB.
Some printed circuit boards must generally consider the following factors before deciding which installation technology to use.
1) The size and shape of a printed circuit board.
2) Number of input and output terminals.
3) Available device space.
4) Required handling convenience.
5) Attachment type.
6) Heat dissipation required.
7) Required protection capability.
8) Circuit type and its relationship with other circuits.
Requirements for printed circuit board
1) Printed circuit board area where components do not need to be installed.
2) The influence of insertion tools on the installation distance between two printed circuit boards.
3) Specially prepare mounting holes and slots in PCB design.
4) When using plug-in tools in equipment, their dimensions should be taken into account in particular.
5) A plug-in device is required, which is usually permanently fixed to the printed Circuit board assembly with rivets.
6) In the installation frame of printed circuit board, special design is required, such as bearing flange.
7) The adaptability of the tools used and the size, shape and thickness of the printed circuit board.
8) The cost of using tools includes the price of tools and new expenditure.
9) In order to fasten and use plug-in tools, it is necessary to be close to the inside of the equipment to some extent.