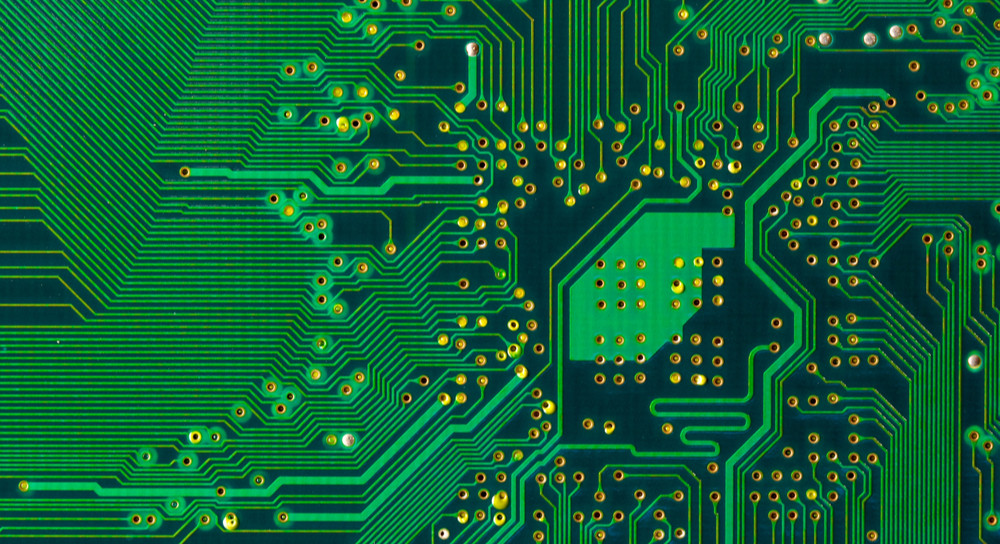
PCB welding method and reasons for using high TG data
1. Immersion tin effect
When the hot liquid solder dissolves and penetrates the metal surface of the PCB being welded, it is called tin in metal or tin in metal. The mixture of solder and copper molecules forms new copper and some solder alloys. This solvent is called tin. It forms intermolecular bonds between various parts of PCB to generate metal alloy compounds. Good intermolecular bond formation is the core of PCB welding process, which determines the strength and quality of PCB welding joints. Only the copper surface is free of pollution, and there is no oxide film formed due to PCB exposure to air, so as to contact tin, solder and working surface need to reach appropriate temperature.
2. Surface tension
Everyone is familiar with the surface tension of water, which makes the cold water drop stay in the metal plate ball shape of the printed circuit board coated with grease, because in this case, the adhesion of the liquid on the solid surface is less than its cohesion Clean with warm water and detergent to reduce surface tension Water soaks greased printed circuit board metal plates and flows outward to form thin metal plates This can happen if the adhesion is greater than the cohesion
The cohesion of tin lead solder is even greater than that of water, making the solder a sphere to reduce its surface area (for the same volume, compared with other geometric shapes, the surface area of the sphere is smaller to meet the requirements of low energy state).
Circuit board
The effect of flux is similar to that of cleaner on PCB metal plate coated with grease In addition, the surface tension largely depends on the cleanliness and temperature of the PCB surface Only when the adhesion energy is much greater than the surface energy (adhesion), PCB is an ideal tin dipping material
3. Zhantianjiao
When the eutectic point temperature of the solder is about 35 ° C higher than that of the solder, a drop of solder drops on the surface of the hot solder PCB to form a meniscus. To some extent, the adhesion between PCB metal surface and tin can be evaluated by the appearance of meniscus. If the meniscus of solder has obvious undercut, the shape is similar to the water drops on the greased PCB metal plate, or even tends to be spherical, then the metal cannot be welded. Only the length of meniscus is less than 30. Small angle, good weldability.
4. Production of metal alloys
The intermetallic bond between copper and tin forms grains. The shape and size of grains depend on the duration and strength of welding temperature. There is less heat in the welding process, which can form a fine crystal structure. This PCB can form a good solder joint with strength. If the reaction time is too long, whether due to too long PCB welding time or too high temperature or both, it will lead to rough crystal structure, that is, sandy and brittle, and low shear strength. Copper is used as the metal substrate of the printed circuit board, and tin lead is used as the solder alloy. Lead and copper do not form any metal alloy compound, but tin can penetrate into copper. The intermolecular bond between tin and copper forms metal alloy compounds Cu3Sn and Cu6Sn5 on the bonding surface of solder and metal.
The metal alloy layer (N phase+Î µ phase) must be very thin. In PCB laser welding, the thickness of metal alloy layer is 0.1mm. In wave soldering and manual soldering, the thickness of the metal bonding layer of PCB solder joints is greater than 0.5m. Since the shear strength of PCB solder joints decreases with the increase of metal alloy layer thickness, the welding time is usually shortened as much as possible to control the thickness of metal alloy layer below 1mm.
The thickness of the metal alloy cobalt composite layer depends on the temperature and time of forming the solder joint. Ideally, welding should be completed in about 2 seconds at 220 ° t. Under this condition, the chemical diffusion reaction of copper and tin will produce an appropriate amount of metal alloy connection data Cu3Sn and Cu6Sn5, with a thickness of about 0.5mm. In cold welded joints, there is usually insufficient metal to metal connection or the temperature does not rise to the proper temperature during welding. This may cause the PCB welding surface to be cut off. On the contrary, in the solder joints that are overheated or have been welded for a long time, an excessively thick metal alloy layer will cause the tensile strength of PCB solder joints to be very weak.
Reasons for using high TG data
In addition to the basic FR-4 data in PCB production, some customers also said that high TG data should be used in the data, so why use high TG data in PCB production?
TG used in PCB production is called glass transition temperature, which represents glass transition temperature. The circuit board must be flame retardant and cannot burn at a certain temperature, but can only be softened. The temperature point at this time is called the glass transition temperature (Tg point), which is related to the dimensional stability of the PCB. The higher the TG value, the better the temperature resistance of PCB. When the temperature rises to a certain area, the substrate will change from "glass like" to "rubber like". This temperature is called the glass transition (Tg) temperature of the sheet. In other words, Tg is the temperature at which the substrate maintains a high temperature (° C). That is to say, common PCB substrate materials will not only produce expansion, deformation, melting and other phenomena, but also have a sharp decline in mechanical efficiency and electrical characteristics at high temperatures.
The addition of substrate thermogravimetry will enhance and improve the heat resistance, moisture resistance, chemical resistance and resistance stability of Shenzhen circuit board. The higher the TG value, the better the temperature equivalent energy of the circuit board. Especially in the lead-free manufacturing process, high TG is used more and more.
High Tg indicates high heat resistance. With the rapid development of the electronic industry, especially the electronic products represented by computers, the development of high functionality and high multilayer has put forward higher requirements for the heat resistance of PCB substrate materials as an important guarantee. The emergence and development of high-density installation technology represented by SMT and CMT makes PCB more and more dependent on the high heat resistance support of the substrate in small aperture, fine wiring and thinning. This is also an important reason for using high TG data in PCB production.
Therefore, in PCB production, the difference between common FR-4 and high Tg FR-4 lies in mechanical strength, dimensional stability, adhesion, and water absorption of data under thermal state, especially when heating after moisture absorption Efficiency differences, thermal decomposition, thermal expansion and other conditions High Tg products are obviously superior to PCB substrate information of ordinary products