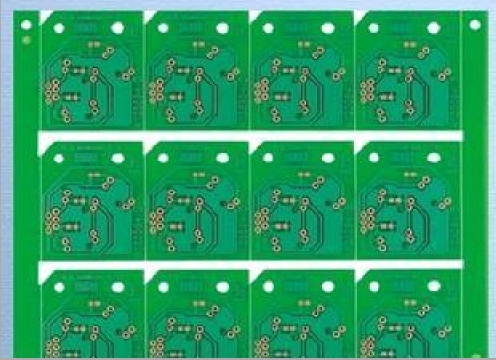
The development of modern science and technology has led to the miniaturization of electronic components and the extensive application of SMT technology and equipment in electronic products. SMT manufacturing device has the characteristics of full automation, high precision and high speed. Due to the improvement of automation, higher requirements are put forward for PCB design. PCB design must meet the requirements of SMT equipment, otherwise it will affect the production efficiency and quality, and may even be unable to complete the computer automatic SMT.
SMT and its attributes
SMT is the abbreviation of Surface Mount Technology, which is an advanced electronic manufacturing technology. It can weld and install components in the specified position of PCB. Compared with the traditional THT (through hole technology), the most significant feature of SMT is the improvement of the degree of automated manufacturing, which is suitable for large-scale automated manufacturing.
The basic integrated SMT production line shall include loader, printer, chip installer, reflow furnace and unloader. The PCB starts from the loader, travels along the path and through the device until production is complete. Then, the PCB will receive high temperature welding through the reflow furnace and be transferred to the unloader during the completion of printing, installation and welding.
PCB Design Elements Affecting SMT Manufacturing
PCB design is a key link in SMT technology, and SMT technology is an important factor to determine the manufacturing quality of SMT. This paper will analyze the PCB design elements that affect the quality of SMT equipment manufacturing. The design requirements of SMT manufacturing equipment for PCB mainly include: PCB pattern, size, positioning hole, clamping edge, MARK, panel wiring, etc.
• PCB pattern
In the automatic line, PCB production starts from the loader and is completed after printing, chip installation and welding. Finally, it will be generated by the unloader as a finished board. In this process, the PCB is transmitted on the path of the device, which requires that the PCB pattern should be consistent with the path transmission between devices.
The channel clamping edge of a standard rectangular PCB is as flat as a line, so this type of PCB is suitable for channel transmission. Right angles are sometimes designed as chamfers.
In PCB design, the clamping edge of the path is not a straight line, so the position of the PCB and the transmission in the device will be affected. The open space in Figure 3 can be supplemented so that its clamped edge becomes a straight line as shown in Figure 4. Another method is to add crack edges on the PCB,
• PCB size
PCB design size must meet the maximum and minimum size requirements of the placement machine. Up to now, the dimensions of most equipment are in the range of 50mmx50mm to 330mmx250mm (or 410mmx360mm).
If the thickness of PCB is too thin, its design size should not be too large. Otherwise, the reflow temperature will cause PCB deformation. The ideal aspect ratio is 3:2 or 4:3.
If the PCB size is smaller than the minimum size requirement of the equipment, the panel shall be assembled. The number of panels depends on the size and thickness of the PCB.
PCB positioning hole
SMT positioning methods are divided into two types: positioning hole and edge position and edge position. However, the most commonly used positioning method is Mark point alignment.
• PCB blank holder
Since PCB is transmitted on the path of the device, the component shall not be placed along the clamping edge, otherwise the component will be squeezed by the device, thus affecting the installation of the chip. Some components are placed near the lower edge of the PCB, so the upper and lower edges cannot be considered clamping edges. However, there are no components near the two side edges, so the two short edges can be used as clamping edges.
Changsha PCB design proofing
• Marking
PCB mark is an identification point for all automatic equipment identification and location, which is used to modify PCB manufacturing errors.
One. Shape: solid circle, square, triangle, diamond, cross, hollow circle, ellipse, etc. A filled circle is preferred.
1. Size: The size must be within the range of 3mm. A solid circle with a diameter of 1mm is preferred.
2. Surface: Its surface is the same as the welding plane of PCB pad, the welding plane is uniform, neither thick nor thin, and the reflection effect is excellent.
A cloth prohibition area shall be arranged around the Mark point and other pads, which shall not contain screen printing and solder mask.
Silk screen characters and silk screen lines are arranged around MARK in Figure 9, which will affect the recognition of MARK points by the equipment, and will cause frequent alarms due to MARK recognition, seriously affecting the manufacturing efficiency.
• Panel method
In order to improve manufacturing efficiency, a plurality of small PCBs with the same or different shapes can be combined to form a panel. For some PCB with double sides, the top side and bottom side can be designed as a panel, so that templates can be produced, which can reduce costs. This method also helps to reduce the displacement time of the top side and bottom side, thereby improving the manufacturing efficiency and device utilization.
The connection method of the panel includes punching holes and V-grooves,
One requirement of the V-groove connection method is to keep the remainder of the plate (uncut) equal to one quarter to one third of the plate thickness. If too many circuit boards are cut off, the notch may break due to the high temperature of reflow soldering, which will cause the PCB to fall, and the PCB will burn in the reflow soldering furnace.
It is a complex technology, which must consider both device requirements and component layout, pad design and circuit design. Excellent PCB design is an important factor to ensure product quality.