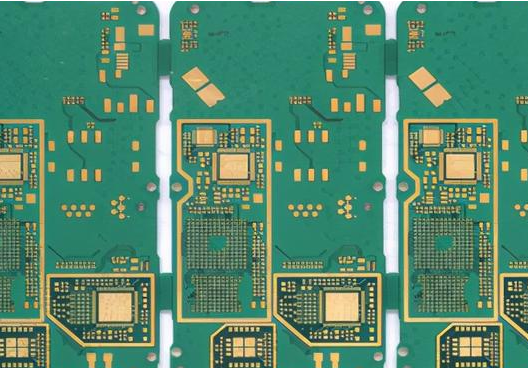
Nowadays, it is more and more common for electronic products to carry the wireless communication function, and the wireless communication technology is realized by relying on the RF circuit on the PCB. Unfortunately, even PCB designers often shy away from the RF circuit because it will bring huge design challenges and require professional design and simulation analysis tools. Because of this, the RF part of PCB has been designed by independent designers with RF design expertise for many years.
The RF circuit design engineer has brought out 18 kinds of martial arts. After a fierce operation, he has designed the RF circuit layout below and exported the DXF format to PCB Layout for copying
After importing the DXF format file of RF circuit into PCB design, we found that the routing has both right angles and sharp corners. We thought to ourselves, emmm, the RF is really water, the salary is higher than the labor, and we don't know how to avoid sharp chamfer and arc transition. Then we re optimized the routing of RF circuit
In order to avoid misunderstanding in the future, the RF bacteria called the layout bacteria after work, and closed the door to guide some key points related to RF PCB design.
According to the radio frequency circuit theory, when the wavelength of the signal transmitted on the signal connection line can be comparable to the geometric dimensions of the discrete circuit components, the bonding pad of the radio frequency IC pin, the transmission line of the radio frequency signal on the PCB, the radio frequency passive components, the through-hole and even the grounded copper laying are all important factors that seriously affect the performance of the radio frequency signal.
Microstrip line is an ideal choice for transmitting high-frequency signals on. Unless the connection distance between IC and antenna is very short, please use coaxial cable or transmission line with matching characteristic impedance. On the printed circuit board, it is better to use the microstrip line transmission line with the structure shown in the figure below.
The microstrip transmission line includes a fixed width metal wire (conductor) and a grounding area directly below (adjacent layers). For example, routing on layer 1 (top metal) requires a solid grounding area on layer 2. The width of the wire, the thickness of the dielectric layer, and the type of dielectric determine the characteristic impedance (usually 50 Ω or 75 Ω).
Of course, in addition to the microstrip line, there is also a common transmission line called the stripline
The ribbon line includes the routing of fixed width of the inner layer and the grounding area above and below it. The conductor can be located in the middle of the grounding area or have a certain offset. This method is suitable for RF cabling of the inner layer.
Since the stripline is also suitable for RF cabling, why did the old Wu say that the microstrip line is the ideal choice for transmitting high-frequency signals on a PCB?
Both the microstrip line and the stripline have excellent performance in transmitting millimeter wave frequency. The difference lies in the manufacturing cost.
Compared with the stripline circuit, the microstrip circuit has fewer processing steps, and the circuit components are easier to place, so it is easier to manufacture (lower manufacturing cost). Compared with microstrip lines, ribbon lines can provide more isolation for adjacent circuit lines and support more dense component layout. In addition, the stripline circuit is also very suitable for manufacturing multilayer circuit boards, and each layer can be well isolated.
The electrical properties of microstrip line and stripline conductor are affected by the dielectric constant of insulating material and proximity effect of ground plane. The microstrip line has only one ground plane, while the stripline has two ground planes. For microstrip lines, the effective permittivity affecting the conductor impedance is the sum of the relative permittivity of the insulating material and the air above the circuit (equal to 1). The effective permittivity of the stripline is the sum of the relative permittivity of the two substrates above and below the conductor.
For all high-frequency circuits, maintaining impedance control is critical to achieving consistent amplitude and phase response electrical performance. The impedance of conductors of two transmission lines is a function of conductor width, conductor thickness, thickness of insulating substrate, relative permittivity or dielectric constant of substrate, among other factors. For striplines, it is not important whether the distance between the central conductor and the two ground planes is equal or whether the dielectric constant of the upper and lower insulators of the conductor is the same (the same is true for microstrip lines).
The stripline has two ground planes, so the 50 Ω (or any given impedance) line of the stripline is thinner than the conductor with the same impedance of the microstrip line. Although thinner wires support higher circuit density, thinner wires also require stricter manufacturing tolerances, and the dielectric constant of the substrate of the entire circuit must be very consistent. The dielectric loss (defined by the dissipation factor of the substrate) of the single ended (unbalanced) transmission line of the microstrip line is less than that of the stripline, because some field lines of the microstrip line are in the air, and the dissipation factor is negligible.
Of course, the performance of these two transmission lines is virtually the same as that of the carrier used in their manufacture, the insulating substrate. As the PCB materials used, such as FR-4, can reduce the cost, but also limit its performance, selecting the most appropriate materials according to different applications of microstrip lines and striplines will give better play to the advantages of these two transmission lines.
Our pcb design company
As with many engineering decisions, the choice of microstrip or stripline will be weighed. For example, the circuit density of the stripline circuit is high. Therefore, at the same frequency, it requires more material layers, more processing time and cost, and more attention to detail processing than the microstrip circuit.
Compared with the common microstrip lines and strip lines, another RF transmission line is grounded coplanar waveguide, which provides good isolation between adjacent RF lines and other signal lines.
build
The transmission mode of microstrip line and grounded coplanar waveguide circuit is quasi transverse electromagnetic mode (quasi TEM). Due to the enhanced grounding structure of grounded coplanar waveguide circuit, its machining is more complicated to some extent. Compared with microstrip line, grounded coplanar waveguide circuit has low dispersion characteristics. When the frequency rises to the millimeter wave band, the radiation loss of grounded coplanar waveguide circuit is lower than that of microstrip line circuit.
Due to the enhanced grounding structure, the grounded coplanar waveguide circuit has wider effective bandwidth and wider impedance range than the microstrip line circuit. However, the microstrip line circuit structure is relatively robust, and its simple bottom ground circuit structure is easy to process. In addition, the performance of microstrip line circuit is not sensitive to circuit processing factors, and its circuit performance is less affected by conductor/gap etching difference and conductor thickness difference.
The sharp corners of RF PCB circuit layout are specially designed for transmission line corner compensation
When the transmission line is required to bend (change direction) due to PCB wiring constraints, the bending radius used should be at least 3 times the width of the intermediate conductor. in other words:
Bending radius ≥ 3 × (Lineweight)
This minimizes the change in characteristic impedance of the corner.