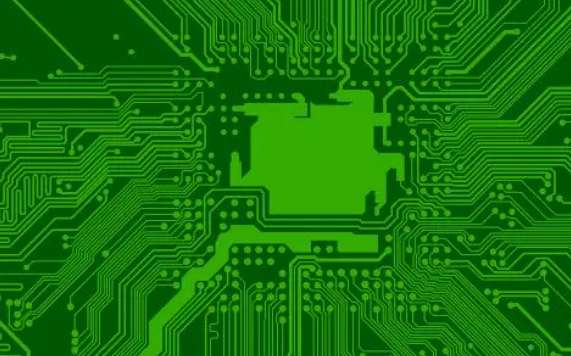
Shown are the wideband test results for the material under test (MUT) at 60mils and Dk = 3.48 using the clamped strip line method.
Ring resonators are often used as test circuits. It is simple and resonates at integer multiples of the mean perimeter of the microstrip loop (see Figure 3a). Signal coupling is usually loosely coupled because loose coupling between feeders and rings minimizes the coupling gap capacitance between them. The capacitance will vary with the frequency, causing the resonant frequency to shift and causing errors when extracting the material Dk. The conductor width of the resonant ring should be much less than the ring radius - as a rule of thumb, less than a quarter of the ring radius.
b is the S21 response of microstrip ring resonator based on 10mil thick circuit board material, where Dk = 3.48. The approximate calculation of Dk is given by the following formula
Although approximate, these formulas are useful for determining initial Dk values. More accurate Dk can be obtained using electromagnetic (EM) field solvers and precise resonator circuit sizes.
The load effect of resonators can be minimized by using loosely coupled resonators when measuring Dk and Df. Loose coupling can be considered if the insertion loss at the resonant peak is less than 20 dB. In some cases, the resonance peak may not be measured due to very weak coupling. This usually occurs on resonant circuits of thinner thickness. Thinner circuit materials are commonly used in millimeter wave applications because the higher the frequency, the shorter the wave length and the smaller the circuit size.
Millimeter wave test method
While there are many Dk testing methods, only some are suitable for millimeter wave frequencies, and none is yet recognized as an industry standard. The following two methods are relatively accurate and have high repeatability in millimeter wave testing.
Differential phase length method
Microstrip line differential phase length method has been used for many years. This is a transmission line test method that measures the phase of two circuits that differ only in physical length (see Figure 4). To avoid any variation in circuit board material properties, the test circuits are designed as close together as possible on the material under test (MUT). These circuits are microstrip transmission lines of varying lengths of 50Ω, and the signal feed is in the form of grounded coplanar waveguides (GCPW). At millimeter-wave frequencies, the GCPW signal feed mode is very important because the design at the feed can have a significant impact on the return loss. A non-soldered connector should also be used to allow a good contact between the coaxial connector and the test circuit without welding, and the same connector can be used to test two circuits of different lengths, minimizing the impact of the connector on the measurement results. For consistency, the same connector should always correspond to the same port on the vector network analyzer (VNA). For example, if connector A is connected to port 1 of the VNA, and connector B is connected to port 2 to test the shorter circuit, the same should be true when testing the longer circuit.
The phase subtraction of long and short circuits also subtracts the effects of connectors and signal feed areas. If the return loss of both circuits is good and the connectors have the same orientation, most of the impact of the connectors can be minimized. When using the differential phase length method at millimeter wave frequencies, the return loss is better than 15 dB below 60GHz and better than 12 dB from 60GHz to 110 GHz.
The Dk extraction equation of the microstrip differential phase length method is based on the microstrip line phase response formula of circuits with different physical lengths:
Where c is the speed of light in free space, f is the frequency of the phase Angle of S21, ΔL is the difference between the physical lengths of the two circuits, and ΔΦ is the phase difference between the short and short circuits.
The test method consists of several simple steps:
Measure the S21 phase Angle of a long and short circuit at a given frequency.
Use the formula to determine the valid Dk.
Test the exact circuit size of the circuit, determine the initial Dk value of the material and input it to the EM field solver.
Use software to generate valid Dk values for the simulation. Change the Dk in the solver until the measured effective Dk of the material matches the simulated effective Dk values at the same frequency.
By increasing the frequency to millimeter-wave and repeating the process, a definitive Dk value at millimeter-wave frequency can be obtained.
Figure 5 shows the frequency variation of Dk of 5mil RO3003G2TM circuit board material tested using the microstrip line differential phase length method. The curve is derived using the Dk calculation tool developed by Rogers. This data reflects the trend of Dk decreasing with increasing frequency. At lower frequencies, Dk varies greatly with frequency. However, DKS from 10 to 110 GHz vary very little with frequency. The curve reflects that materials with low losses and smooth calendered copper are used, and materials with high losses and/or high copper surface roughness show about a large negative slope in the Dk with frequency. Using this test method, the insertion loss of the circuit of the material under test (MUT) can also be obtained by the S21 loss value of the short and short lines at each frequency (see Figure 6).