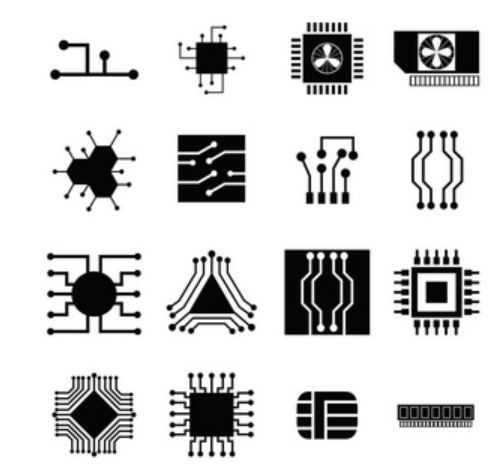
The "edge" formed by tin or lead tin makes it impossible to completely remove the sensitive film when removing the film, leaving a small part of the "residual glue" under the "edge". The "residual glue" or "residual film" left behind the resist "edge" will cause incomplete etching. The lines form "copper roots" on both sides after etching. The copper roots narrow the line spacing, resulting in the printed board does not meet the requirements of Party A, and may even be rejected. Because the rejection will make the production cost of PCB greatly increased. In addition, in many cases, due to the reaction and dissolution, in the printed circuit industry, residual film and copper may also form accumulation in the corrosion fluid and blocked in the nozzle of the corrosion machine and acid pump, have to stop processing and cleaning, and affect the efficiency of the work.
Equipment adjustment and interaction with corrosive solutions
Ammonia etching is a delicate and complex chemical process in printed circuit processing. On the other hand, it is an easy task. Once the process is upgraded, continuous production can be carried out. The key is to maintain a continuous working state once the boot, should not be dry stop. The etching process depends greatly on the good working condition of the equipment. At present, no matter what kind of etching fluid is used, high pressure spray must be used, and in order to obtain a cleaner line side and high quality etching effect, the nozzle structure and spray mode must be strictly selected.
In order to get a good side effect, there are many different theories, the formation of different design and equipment structure. These theories are often vastly different. But all theories about etching acknowledge the basic principle of constantly exposing metal surfaces to fresh etching fluids as quickly as possible. The chemical mechanism analysis of etching process also confirmed the above viewpoint. In ammonia etching, assuming all other parameters are constant, the etching rate is mainly determined by ammonia (NH3) in the etching solution. Therefore, the purpose of using fresh solution and etching surface action is mainly two: one is to wash away the copper ions just produced; The second is the continuous supply of ammonia (NH3) needed for the reaction.
In the conventional wisdom of the printed circuit industry, especially the suppliers of printed circuit raw materials, it is accepted that the lower the content of copper ions in ammonia etching solution, the faster the reaction. This has been borne out by experience. In fact, many ammonia etching liquid products contain special coordination groups of monovalent copper ions (some complex solvents), whose role is to reduce monovalent copper ions (these are the technical secrets of their products with high reaction capacity), so that the influence of monovalent copper ions is not small. When copper is reduced from 5000 PPM to 50ppm, the etching rate more than doubles.
Ultraviolet marking process is the use of UV light and material photochemical reaction resulting in color changes to achieve, using appropriate parameters can avoid the material surface to produce obvious removal effect, so can mark no obvious tactile graphics and characters.
Although UV laser can be used to mark metals and non-metals, due to cost factors, fiber laser is generally used to mark metal materials, and UV laser is used to mark products with high surface quality requirements, CO2 is difficult to achieve, and CO2 form high and low match.
Green laser is also a short wavelength laser, generally using frequency doubling technology, the solid laser emitted infrared light (1064nm), into 532nm (double frequency) green light, green laser is visible light, UV laser is invisible light. Green laser photon energy is very large, its cold processing characteristics are very similar to UV light, and can form diversified selection with UV laser.
Green marking process is the same as ultraviolet laser, which uses green light to change color due to photochemical reaction with materials. Appropriate parameters can avoid obvious removal effect on the surface of materials, so the graphics and characters without obvious tactile sensation can be marked. PCB board surface generally has a tin mask layer, which usually has a variety of colors. Green laser and its reaction effect is very good, marking out the graphics are very clear and delicate.
CO2 is a commonly used gas laser with abundant luminous levels. The typical laser wavelength is 9.3, 10.6um, and it is a far-infrared laser with continuous output power up to tens of kilowatts. Low-power CO2 lasers are usually used to complete the marking process of non-metallic materials such as polymers. CO2 lasers are rarely used to label metals because of their very low absorptivity (high power CO2 can be used to cut and weld metals, which have been gradually replaced by fiber lasers due to factors such as absorptivity, electro-optical conversion, optical path and maintenance).
CO2 marking process is realized by using the thermal effect produced by laser on materials, or by heating and vaporizing surface materials to expose deep materials of different colors, or by heating microscopic physical changes occurring on the surface of materials to make obvious changes in its reflective properties, or by some chemical reactions occurring during light heating. And display the required graphics, characters, two-dimensional code and other information.
CO2 laser is generally used in electronic components, instruments, clothing, leather, bags, shoes, buttons, glasses, medicine, food, beverage, cosmetics, packaging, electrical equipment and other fields using polymer materials.
Damage analysis and summary of laser coding on PCB materials
Both fiber laser and CO2 laser use the thermal effect produced by laser on materials to achieve the marking effect. Basically, the surface of the material is destroyed to form the elimination effect, and the background color is leaked out to form the color difference. Ultraviolet laser and green laser are the use of laser chemical reaction to materials and lead to changes in the color of the material, and then do not produce the elimination effect, the formation of no obvious tactile graphics and characters.