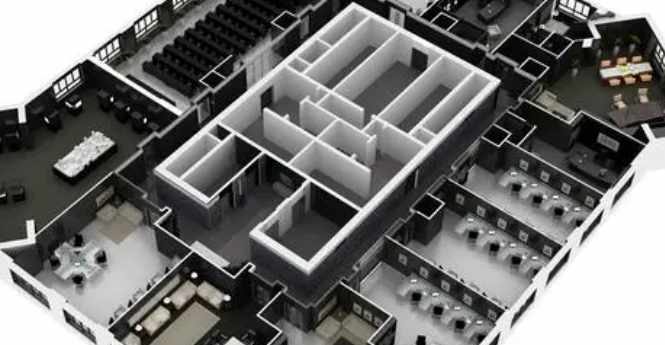
First, manual welding method
Manual welding is a traditional welding method. Although manual welding is rarely used in the mass production of electronic products, it is still inevitably used in the maintenance and debugging of electronic products. The quality of welding also directly affects the maintenance effect. Manual welding is a very practical skill, after understanding the general method, to practice more; More practice, can have better welding quality.
There are three methods of hand welding of electric soldering iron, namely holding, holding and holding the pen. It is more convenient to hold a pen when welding components and repairing circuit boards.
Manual welding is generally carried out in four steps.
(1) Preparation for welding: clean the dust and oil accumulation at the welded components, and then break the components around the welded components so that the electric iron head can touch the solder of the welded components, so as not to burn other components when the iron head reaches to the welding. When welding new components, the leads of components should be tinned.
(2) Heating welding: Touch the electric iron head with a little solder and rosin to be welded components for about a few seconds. If you want to remove the components on the printing plate, after heating the iron head, gently pull the components with your hand or silver to see whether it can be removed.
(3) Clean the welding surface: if the welding part is too much solder, the solder on the head of the soldering iron can be shaken off (pay attention not to the skin, and do not throw to the printed circuit board!) "Dip" some solder into the tip of a tin with a torch. If the solder joint is too little, not smooth, you can use the electric iron head "dip" some solder to solder the solder joint.
(4) Check the solder joint: See whether the solder joint is smooth, bright and firm, whether there is a phenomenon of welding with the surrounding components.
Two, the reason for the poor welding quality
The requirements of manual welding for solder joints are:
① Good electrical connection performance;
(2) Have a certain mechanical strength;
③ Smooth and round.
Common reasons for poor welding quality are:
(1) Excessive amount of solder, forming solder joints of tin accumulation; There is too little solder to cover the solder joint.
② Cold welding. When welding, the temperature of the iron is too low or the heating time is not enough, the solder is not melted, infiltrated, the solder surface is not bright (not smooth), there are small cracks (as well as!). .
(3) Clip rosin welding, solder and components or printing plate between a layer of rosin, resulting in poor electrical connection. If the underheated rosin is included, there is a yellow brown rosin film under the solder joint. If the heating temperature is too high, there is a layer of carbonized rosin black film under the solder joint. For the case of insufficient heating rosin film, you can repair welding with a soldering iron. For the black film has been formed, it is necessary to "eat" the clean solder, clean the surface of the welded components or printing plates, and weld again.
④ Solder bridge. Finger solder amount is too much, resulting in short circuit between the solder joints of components. This should be paid particular attention to when welding the most small components and small printed circuit boards.
⑤ too much flux, rosin residue around the solder joint. When a small amount of rosin remains, you can gently heat it with an electric iron to allow the rosin to evaporate, or you can use a cotton ball dipped in alcohol without water to wipe away the excess rosin or flux.
The solder on the surface of the solder joint forms a sharp tip. This is mostly due to insufficient heating temperature or too little flux, as well as improper Angle when the iron leaves the solder joint.
3. Welding of vulnerable components
Vulnerable components refer to components that are easy to cause damage when exposed to heat or contact with electric iron in the process of installation and welding, such as ** casting components, MOS integrated circuits, etc. Vulnerable components should be carefully prepared for surface cleaning and tin plating before welding. During welding, repeated scalding welding should be avoided for a long time. The iron head and temperature should be selected appropriately to ensure a successful welding. In addition, use less flux to prevent it from infecting electrical contacts of components (such as relay contacts). It is better to use energy storage electric iron for welding MOS integrated circuit to prevent damage to integrated circuit due to weak leakage of electric iron. Because the lead spacing of integrated circuit is very small, we should choose the appropriate iron head and temperature to prevent tin between the leads.
It is best to weld the ground end, output end and power end before welding the input end. For those components that are particularly sensitive to temperature, a cotton ball dipped in water (alcohol) can be held with tweezers to protect the root of the component, so as to minimize the heat transfer to the component. Learn more C language, JAVA, Android, IOS, FPGA, PCB, Microcontroller,