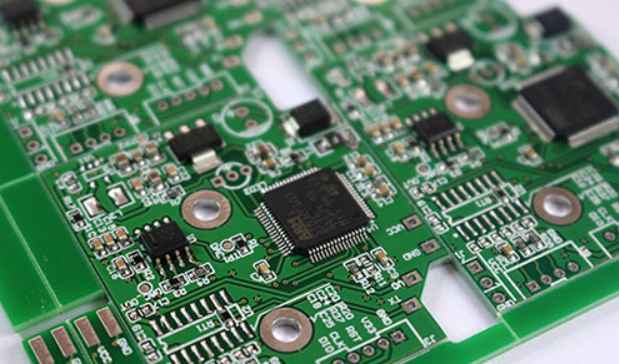
The following factors should be considered in the selection of capacitor components in PCBA processing:
First, capacitor voltage selection
In the selection of capacitance, the voltage of the component must be higher than the actual circuit in the working voltage, especially noteworthy is that the electronic circuit to take into account the possible high voltage.
Second, capacitance selection
In electronic circuits, capacitance is determined according to certain performance indicators, in determining the capacity to choose according to the nominal series. If the capacity value of the capacitor cannot be found through the nominal series, it can be solved by series parallel method or by modifying other parameters in the design scheme. When replacing the capacitor in the circuit, it is best to choose the original parameters of capacitive or performance index better than the original circuit capacitor components.
Three, capacitor medium selection
Capacitive media have different characteristics and different uses. In the selection of capacitive medium, we should first understand the characteristics of each medium, and then determine what is suitable for the occasion.
The following describes the use of several commonly used fixed capacitors:
1. The electrolytic capacitor is based on aluminum and other metals as the positive electrode, forming a layer of oxide film on its surface as the medium, the medium and the electrode become inseparable whole; The negative electrode is a solid or non-solid electrolyte. Because of the different materials of the two electrodes of the electrolytic capacitor, its positive and negative electrodes are marked respectively. When used, the high potential of the positive extreme connection circuit and the low potential of the negative extreme connection circuit must be used, otherwise it will cause damage to the capacitor. There are aluminum electrolytic capacitor, tantalum electrolytic capacitor and niobium electrolytic capacitor according to the different electrode materials.
2. Mica capacitor is a capacitor of mica sheet as medium. It has good insulation performance, low loss, good temperature stability, high capacitance accuracy, and is commonly used in high frequency oscillation circuit board.
3. The dielectric capacity of porcelain is ceramic, which can be divided into high frequency porcelain dielectric capacity and low frequency porcelain dielectric capacity according to different ceramic components (high frequency is represented by CC, low frequency is represented by CT). The dielectric capacity of high frequency porcelain is between a few hundredths of a skin method and several hundred skin method. It is often used in the occasions requiring small loss and stable capacitance and in high frequency circuit as tuning capacitor, oscillation circuit capacitor and temperature compensation capacitor. Capacitor voltage is 160V, 250V and 500V and so on. The capacity error is divided into 2%, 5%, 10% and 20%. Low frequency porcelain dielectric capacity from 300pF to 22000pF, suitable for low frequency circuit.
4. Paper capacitor production process is simple, low cost, wide voltage range; The disadvantage is that the capacitance is not easy to control, the loss is large, the stability is poor, the inductance is the largest, usually not suitable for use at high frequency.
5. Polyester capacitor is also called polyester capacitor. It is made of polyester film as a dielectric capacitor. It can be used in a variety of electronic instruments, television, radio recorder coupling, decoupling, bypass, DC separation circuit.
6. Polystyrene capacitor is a capacitor made of polystyrene film as a medium. The biggest characteristic of polystyrene capacitor is high insulation resistance. This kind of capacitor has low high-frequency loss and stable capacitance. It is a kind of capacitor widely used at present. Because of its high precision, it is widely used in filters and circuits requiring accurate capacity (such as electronic organ circuit). Its disadvantage is that the operating temperature range is not wide, the upper limit is +75℃. Therefore, the contact time of the soldering iron should not be too long when welding, so as not to damage the film due to overheating.
2. What are the main reasons for insufficient solder paste in SMT patch processing
1. The solder paste was not added in time when the printing press was working.
2. Abnormal quality of solder paste, which is mixed with hard and other foreign bodies.
3. The previously unused solder paste has expired and is used twice.
4, circuit board quality problems, there is an inconspicuous cover on the pad, such as the solder resistance (green oil) printed on the pad.
5, the circuit board in the printing press fixed clamping loose.
6, solder paste printing screen thickness is not uniform.
7, solder paste leakage screen board or circuit board there are pollutants (such as PCB packaging, screen board wiping paper, floating foreign bodies in the environment air, etc.).
8, solder paste scraper is damaged, the screen is damaged.
9. The pressure, Angle, speed and demoulding speed of solder paste scraper are not set properly.
10. After the solder paste was printed, it was accidentally knocked off because of human factors.