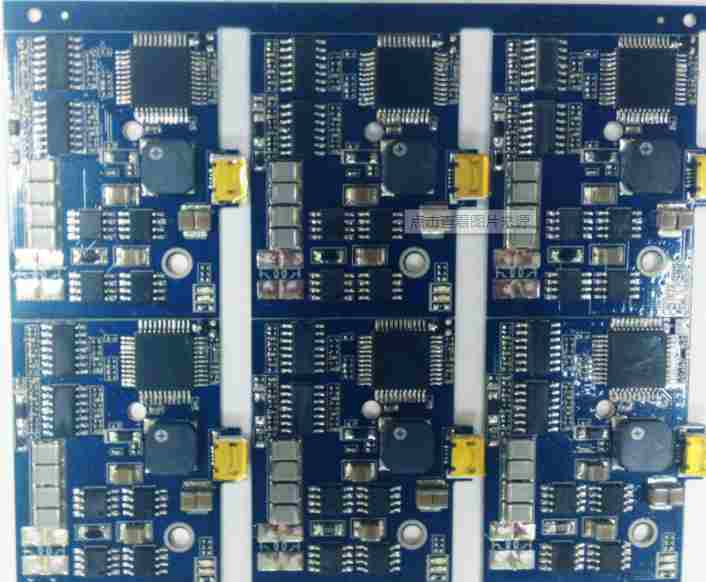
◆ Task and method of raw material quality inspection for SMT processing plant
Tasks: Raw material quality judgment, quality problem prevention, quality information feedback and quality problem arbitration
Methods: Sensory detection, instrument detection and trial detection
Quality judgment: It refers to the qualification degree or quality grade of raw materials through testing in accordance with relevant quality requirements and specifications
Quality problem prevention: It means to ensure that unqualified raw materials are not put into use through quality inspection, so as to prevent the quality problems caused by this.
Quality information feedback: it refers to feedbacks of quality problems existing in raw materials to relevant departments or cooperative enterprises through quality testing, timely finding out the causes of quality problems and providing basis for quality improvement.
Arbitration of quality problems: When the supplier and the recipient of raw materials have objections or disputes over quality problems, scientific quality detection and evaluation methods are adopted to determine the causes and responsibilities of quality problems.
SMT paste incoming materials including
Components, PCB board, welding paste, flux, bonding agent, cleaning agent and other mounting process materials.
◆ Main test items of components
Weldability, lead coplanar, service performance
◆ The weldability of SMT components mainly refers to the weldability of welding ends or pins.
Influencing factors: oxidation or contamination of welding end or pin surface of components.
Component weldability test methods: there are a variety of, the more commonly used are - welding groove infiltration method, welding ball method, wetting weighing method
Groove infiltration method
Samples are dipped in flux and removed. Excess flux is removed and then dipped in the molten solder tank for approximately twice the actual production welding time. Visual evaluation is performed: All samples to be tested shall demonstrate a continuous solder coverage, or at least 95% of the total solder coverage of each sample is acceptable.
◆ Ball welding method
Select the welding ball with appropriate specifications according to relevant standards and place it on the heater to heat to the specified temperature;
Lay the test part (lead or pin) of the sample coated with flux horizontally and vertically dip into the welding ball at the specified speed;
Record the time until the lead is completely wet and covered by the ball.
According to the length of the time to measure the weldability is good or bad, the lead is fully wet by the welding ball ls time, more than 2s is unqualified.
◆ Principle of wetting weighing method
Hang the sample of the component to be tested on the beam of the sensitive scale; Immerse the part of the sample under test into the molten solder (tin furnace) at a constant temperature to the specified depth; The resultant forces of buoyancy and surface tension on the immersed sample in the vertical direction are measured by the sensor and converted into signals, which are recorded by the high-speed characteristic curve recorder into the force time function curve. The test results are obtained by comparing the function curve with the ideal wettability weighing curve (a test sample with the same properties and size that can be fully wetted).
Component pin coplanar
The pin coplanar of surface-mounted components is not high, which affects the welding performance and the good contact between the pin of the components and the PCB pad.
The standard tolerance value of pin coplanar for surface mount devices is 0.1mm
That is, the vertical distance between the highest sole of the pins and the plane formed by the bottom three pins is no more than 0.1mm.
◆ Method of coplanar detection of component pins
The component was placed on a plane, and the value of the deviation of the highest sole from this plane was measured with a measuring instrument. The component was placed on the optical plane, the distance between the non-coplanar pins and the optical plane was measured with a microscope, and the visual system (AOI) was used for automatic detection. The performance of components generally needs to be tested before installation, otherwise the cost of repair and rework is very high.
The conformity between the actual performance parameters of components and the nominal performance parameters is checked by general or special testing instruments.
PCB appearance defect detection
Welding resistance film and pad alignment; Whether the welding resistance film has impurities, peeling, wrinkling and other abnormal conditions; Whether the reference mark is conforming; Circuit conductor width (line width) and spacing meet the requirements; Whether the multilayer board has peeling layer, etc.
◆ PCB solderability test
Test point: Weldability test of pad and plating through hole
Test methods: edge dipping test, rotary dipping test, crest dipping test, solder bead test, etc. (IPC-S-804 standard, etc.)
Edge impregnation test: used to test the weldability of surface conductor
The sample (edge) is impregnated with flux and removed. Excess flux is removed and impregnated in a molten solder tank for a period of time. The sample is then removed for visual or optical evaluation.
◆ Rotary dip test
Weldability test of surface conductors and electroplating through holes;
The test sample is fixed and clamped on the rotating test arm, which rotates at a certain speed according to the adjusted trajectory;
The surface impurity eliminator first removes impurities from the solder surface through the melt solder tank;
The test sample is then impregnated (stay at the molten solder liquid surface for about 3s to 5s according to the standard immersion depth);
After cooling off the molten solder level, visual inspection or instrument evaluation is performed.
PCB welding resistance film integrity test
The welding resistance film covering problem occurs, which affects welding. Under the thermal stress impact generated by reflow welding, the PCB surface will be stripped and broken. The PCB used for SMA generally adopts dry film or wet film solder paste which is composed of alloy solder powder, paste flux and some additives
In addition to the main content such as viscosity, collapse, solder ball and wetness, it is also necessary to detect the visual content such as the appearance and printing performance of the solder paste.
Printing performance of solder paste
Printing should be able to smoothly and continuously transfer to the PCB through the template or screen, without plugging holes, transfer is not smooth and other problems. The reasons leading to poor printing performance are insufficient printing aid, poor shape of alloy powder or particle distribution does not meet the requirements;
The typical viscosity of solder paste for printing SMT is 200Pa·s ~ 800Pa·s
◆ The main factors affecting the viscosity of solder paste
Flux, alloy percentage, alloy powder;
◆ Shape and temperature
Solder paste viscosity test standard: IPC - SP - 819;
Solder paste viscosity detection method: rotary viscosity meter;
◆ Thixotropic coefficient of solder paste
Thixotropy coefficient characterizes the thixotropy property of solder paste, and good solder paste has higher thixotropy coefficient
◆ Wettability of welding paste
The ability of solder paste to moisten and spread on oxidized copper was used to characterize the activity degree of solder paste.
◆ Commonly used test methods
Print welding paste with diameter of 6.5mm and thickness of 0.2mm on the copper skin. After welding, the diameter should be expanded by 20% ~ 30%, otherwise it is considered poor wettability.
◆ Solder ball
In the use of solder paste for reflow welding, when the solder paste has moisture, oxidation and other quality problems, welding may produce solder balls, and scattered in the vicinity of the component pins. Cause problems: cause solder joints bad, even short circuit and other failures.
◆ Collapse degree of solder paste
Solder paste collapse degree: after solder paste is printed on PCB and subjected to a certain high temperature, if the appearance of the edge shape is blurred and irregular, and even the phenomenon of adjacent graphics interconnection occurs in serious cases, it indicates that the solder paste has appeared "collapse".
Cause problems: Collapse phenomenon is one of the main causes of welding defects such as bridge and solder bead in the process of reflow welding.
Detection method: On the standard template, whether there is a bridge between the printed solder paste graphics, to judge the collapse of the solder paste.
◆ welding paste alloy percentage detection method: heating separation weighing method, the procedure is:
(1) Take 0.1g of the solder paste sample into the crucible;
Crucible heating and solder paste;
③ Solidify the alloy and remove the flux residue;
④ Weigh the alloy weight, alloy percentage = (alloy weight/solder paste weight) Xl00 %.
The oxidation of alloy powder is the main factor for forming welding defects such as solder ball, and the content of oxide on the surface of alloy powder is usually required to be less than 0.15%.
Bonding force of solder paste
Requirements: The solder paste must have a certain bonding force.
After printing, the components are attached to the required position.
No movement of components occurs during PCB transmission.
It is generally required that the solder paste can still maintain sufficient bonding force within 8 hours after printing.
The function of flux
It is mainly to remove the oxide of the welding metal surface, prevent the reoxidation of the solder and the welding surface during welding, reduce the surface tension of the solder, enhance the wettability, accelerate the heat transfer and so on.
◆ Classification according to traditional chemical composition
There are four types of flux: loose-scented (R), water-soluble (WS), synthetic-activated (SA), and low-solid (LS). The first three typically contain 25% to 35% (by weight) non-volatile (solid) substances. Low solid type contains less non-volatile material (1% to 5% by weight).
Classification of flux by activity: It can be simply divided into three main types: low active (L), medium active (M), and high active (H). Corrosive flux for flux labeled "M" or "H".
Low solid flux (LSF) has more active agents. The advantage of low solid flux is that it eliminates cleaning after welding.
◆ Characteristic requirements of no-cleaning flux
The residue is non-viscous. Flux and residue are non-corrosive and active enough to ensure qualified welding quality.
◆ Main test items
Appearance inspection, foaming capacity and solid content, expansion rate and relative wetting force, dryness of residue after welding, resistivity of aqueous solution, corrosion of copper mirror, chlorine content and acid value, insulation resistance, etc.
◆ Flux expansion rate index
The expansion rate of inactive rosin flux (R) should not be less than 75%, the expansion rate of moderately active rosin flux (RMA) should not be less than 80%, the expansion rate of fully active rosin flux (RA) should not be less than 90%, and the expansion rate of low solid free cleaning flux should not be less than 80%.
◆ Clean free flux
If the use of loose-scented liquid flux or low-solid no-cleaning flux is not cleaned, the residue left after welding is required to dry (the residue is non-viscous), otherwise the adhesion of the flux residue may bring product pollution, and even affect the electrical performance of the product.
◆ The role of binder
For SMT, it shall have suitable viscosity, low collapse, fast curing, moderate bonding strength, high temperature resistance, good electrical performance, chemical stability, no odor, identifiable color, stable storage and other properties.
The main items of adhesive testing: viscosity and thixotropic coefficient, bonding strength, spreading and collapsing property, curing time, electrical performance, whether there is deterioration phenomenon appearance testing, etc.
◆ Bonding strength of binder
The components are bonded to the PCB to ensure that they do not fall off due to vibration and thermal shock during the welding process.
Cleaning agent and cleaning effect detection
The main role of cleaning: to remove the residual flux and residue on the circuit components to prevent corrosion of the circuit.
Incoming materials of cleaning agent are detected by appearance detection, cleaning agent detection (generally by gas chromatography (GC)), cleaning effect test and other methods.