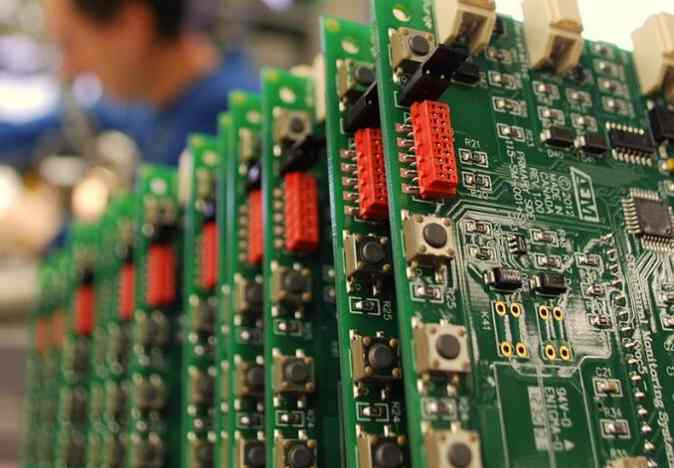
1. The quality of SMT products determines the market of SMT processing, and the quality of smt processing determines the quality of products. In order to prevent defects in the process of SMT processing, which machines and equipment can guarantee the quality of customers?
First of all, there are 9 testing processes, so how do 9 testing projects play a role in quality control?
1, solder paste testing equipment, global Wei uses online 3DSPI solder paste detector, it has the following characteristics:
① Discover the quality of printed matter in time. ② Find the trend of quality change, control the trend of spread. Then adjust in time.
2, online AOI testing equipment, check whether the production of products have error leakage, solder paste printing, offset, less tin, more tin, break. Even tin. Pollution and other parts defects missing parts, offset, skew, erect tablet, side stand, turn over pieces, wrong pieces, damage, reverse solder spot defects tin less, solder, even tin, copper foil pollution and a series of devices, solder paste problems, so as to ensure your quality
3. Off-line automatic aoi optical testing equipment is used for testing devices and solder paste after backfurnace welding. Sensitive elements need to be handled with extreme manual care.
4, X-RAY welding detection, for the naked eye can not see the original welding spot detection, to avoid virtual welding short circuit into the next process.
5, each process of manual detection, strict quality control. Smt processing is never expected to ship, layers of control quality exile, is to achieve 100% factory qualified rate. We understand that customers are worried about the quality of products in smt processing. What they need is continuous cooperation with customers. Fake products are only one order, which is not our original intention
2. Manage SMT processing materials provided by customers
In order to standardize the use procedure of materials provided by customers, ensure the storage safety of materials, control the production cost of the company, improve the economic benefits of the company and promote the development of production of the company, global smt manufacturers have carried out the ERP order management system, strictly treat each progress and the use of materials, and ensure the feedback of customer orders and the management system of the company. The following are the principles of material management of smt factory.
(1) First-in, first-out: the materials that enter the warehouse first go out of the warehouse for use
(2) Timely and appropriate amount: master the timing and quantity of each link of the warehouse.
(3) Consistent accounts: It is required to keep the daily record of the bill consistent with the real thing.
(4) Daily inventory: Warehouse staff must check the materials they are responsible for every day to keep the daily accounts consistent.
(5) E-management: realize the systematization and paperless management
SMT processing material management mode
(1) Kanban management: in the warehouse, the material number, quantity, warehousing date and other material information is listed in the form of a table, made of Kanban standing on the end of the shelf.
(2) Storage management: follow up different materials to be placed in different areas of the shelf, that is, the storage location of materials, shelf determination, positioning.
(3) FIFO management: advanced materials will be put into use first out of the warehouse, and the incoming months will be marked with different colors. See Figure 3.
(4) Area management: Different areas are represented with different colors as the identification of different materials.
(5) Management of defective products: After confirmation by the defective quality control personnel, the rejected label shall be affixed, placed in isolation, and returned to the defective product warehouse.
(6) MSD management: Due to the hygroscopicity of MSD components, its exposure time in the air must be controlled according to its sensitivity level.
3.SMT patch processing and welding technology
The installation and welding of surface assembly parts are mainly carried out by automatic installation and welding methods (the above-mentioned automatic welding methods such as wave soldering and reflow welding). The installation and welding of surface assembly parts are mainly divided into two basic technology methods, namely solder paste/reflow welding process and patch glue/wave soldering process
1. Welding paste/reflow welding process
Mainly for the installation and welding of welding components (SMDS), the solder paste/reflow welding production line is mainly composed of three major equipment: solder paste printing, SMT machine and reflow welding furnace. Different plug-in components are inserted before welding. It is first coated with solder paste on the solder plate of printed circuit board, and then pasted on the solder plate of the front coating paste through the high-precision automatic equipment SMT machine integrating optical, electrical, gas and mechanical. Finally, the solder paste is heated by the reflow welding furnace and melted again, so that the patch components are firmly welded to the solder plate.
2. Patch glue/wave soldering process
When a combination of patch components and traditional jack components need to be installed on a printed circuit board, the patch glue/wave soldering process is used. This process is first in side a through the butt pad between the space point adhesive, the patch component attached to the circuit board side a, and then turn over. Through the hole element on side b, so that the pin of the through hole and the patch element are on side a, that is, the lower plate, the plug-in and the patch element can be welded after wave soldering. The sticker/wave soldering process is cheap, but it requires many equipment and is difficult to achieve high-density assembly.
Reasonable assembly process is the guarantee of quality and efficiency. After the surface assembly method is confirmed, the process process can be confirmed according to the needs and specific equipment conditions. Different assembly methods have different process flow, the same assembly method can also have different process flow, which mainly depends on the type of materials and surface treatment quality requirements and so on.
Power board SMT patch processing technology has what
Return list
smt patch processing time: 2021-11-13 10:38
The PCB circuit board that provides the power supply is almost called the power supply board, the power supply board is mainly dealt with the power supply function. The SMT patch processing process of the power supply board is basically divided into three processes: automatic SMT patch component mounting, wave soldering plug-in, manual operation section. So the power board in the process of patch processing, will have those process requirements?
1. First of all, the temperature resistance requirements of the power board pcb, whether it reaches the level required by the customer; Whether it conforms to the lead-free process; The source plate is not bubbling, especially the process requirements of the rubber sheet more attention.
2. The temperature resistance value of Smt patch processing devices can fully meet the requirements of solder melting temperature of parts on the board (40-90 seconds above 222 degrees; Withstand temperature above 245 degrees). If the customer has special requirements, to inform and provide information in advance.
3, the power board in the patch processing parts spacing, material between aniseed and small material can not be less than 1mm, the spacing between the 0805 materials is greater than 0.3mm.
4. Design requirements of solder pad for smt patch processing, there shall be no wire holes on the solder pad, no tin leakage holes on the edge of the component solder pad, and circuit design of the power board shall meet the packaging requirements of the device.
5, half of the power board requirements, transmission side can not have a gap.
Some customers' products require the process requirements of double-sided pasting. The general reference choice is the reference of the production capacity of the SMT manufacturer and the accuracy of the SMT machine. In order to achieve higher accuracy, the two-sided surface assembly process of PCBA processing of the power supply board is as follows: Side A printed solder paste - patch - reflow welding - flip plate - side B printed solder paste - patch - reflow welding;
We need to find out the most appropriate process requirements and operating conditions from actual operations and records