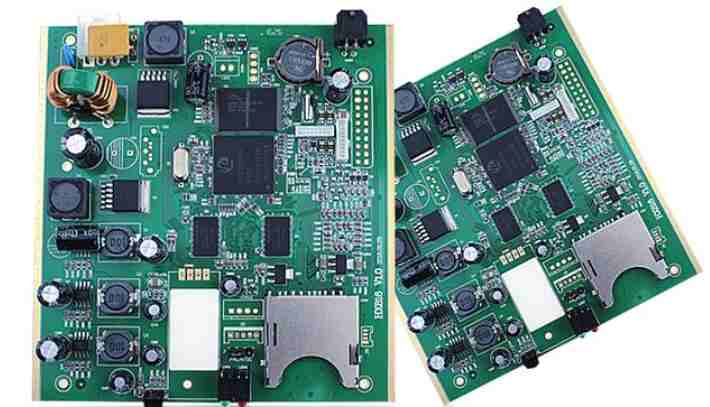
How to guarantee the quality of solder joint has become an important subject of high precision patch. As a bridge of welding, the quality and reliability of solder joint determine the quality of electronic products. That is to say, in the PCBA process, the quality of SMT is ultimately reflected in the quality of solder joints. A good solder joint should be in the service life of the equipment, its mechanical and electrical properties do not fail. The following patch processing manufacturer Xiaobian to explain how to judge the SMT patch processing quality and how to judge the PCB board is good or bad related knowledge.
1. How to judge the quality of PCB board
Due to the fierce competition in PCB market, PCB raw materials are also rising, so more and more PCB manufacturers often use low prices to monopolize the market in order to increase competitiveness. But behind the low price is to reduce the cost of materials and production costs, which will make PCB appear easy to crack, easy to scratch, precision unqualified and other problems, seriously affect the product solderability and reliability. Next, Shenzhen PCB manufacturer teaches you how to judge the quality of PCB board, so that you will not only pay attention to the price of PCB, but not to the quality of PCB.
1. Distinguish the quality of the circuit board by its appearance
First of all, we should distinguish the materials used for PCB board, and then look at the PCB board ink discoloration, copper deposition, surface treatment, smell. PCB board materials are usually as follows: The common HB board 22F is the cheapest and prone to deformation and breaking, and can only be used as a single panel. PCB surface color is deep yellow, with pungent odor, coarse copper and thinner color. Single-sided 94V0 and CIM-1 boards cost more than cardboard but are less expensive than semi-fiberglass boards. PCB surface is light yellow, mainly used for industrial boards and switchboards requiring fire rating. FR4 fiberglass board, high cost and strength. Basically most double-sided and multilayer boards use this material, copper can be very accurate, and PCB boards are relatively heavy. Surface treatments include OSP, gold plating, hot air leveling and other processes. The PAD surface must not be contaminated. Otherwise, it will affect the weldability. In addition, consideration should also be given to the size and thickness of the standard weld appearance. This may affect the quality of the weld.
2. Judge the quality of PCB board itself
Specification requirements ▪ Meet electrical connection requirements. ▪ The width, thickness and distance of the circuit should meet the requirements to avoid high temperature, break or short circuit. ▪ Copper surface should not be easy to oxidize, otherwise it will affect the SMT speed, and cannot be used for a long time after oxidation. ▪ No other electromagnetic radiation. ▪ The shape should not be deformed, and the deformation error of the hole position and reference line of the circuit board should be within the allowable range. ▪ High temperature, high humidity and tolerance to special environments should also be considered. ▪ The mechanical properties of the surface shall meet the installation requirements. Shenzhen Honglijie PCB production capacity ▪ energy production of 2 layers to 14 layers, 14-22 layers can be proofing production. ▪ Minimum line width/pitch: 3mil/3mil BGA pitch :0.20MM. ▪ Minimum aperture: 0.1mm Size :610mmX1200mm. ▪ high frequency boards: Rogers, Taconic, ARLLON. ▪ Surface process: Tin spray, lead-free tin spray, gold plating, full plate gold plating, plug gold plating, full plate thick gold, chemical tin (silver), anti-oxidation (OSP) blue glue, carbon oil. The above is about how to judge the quality of PCB board introduction, if you need to do PCB proofing, SMT processing, PCBA OEM, welcome to contact deep kingford!
2. How to judge the SMT patch processing quality
With the development trend of light, small and portable electronic products, the electronic components used in SMT processing are also getting smaller and smaller. The resistance and tolerance parts of 0402 have been largely replaced by 0201 size. How to guarantee the quality of solder joint has become an important subject of high precision patch. As a bridge of welding, the quality and reliability of solder joint determine the quality of electronic products. That is to say, in the PCBA process, the quality of SMT is ultimately reflected in the quality of solder joints. A good solder joint should be in the service life of the equipment, its mechanical and electrical properties do not fail.
Its appearance is as follows:
1. Complete, smooth and bright surface; 2. The appropriate amount of solder and solder completely cover the welding parts of the pad and lead, and the height of the components is moderate; 3. Good wettability; The edge of the welding point should be thin, and the wetting Angle between the solder and the pad surface should be less than 300, and the maximum should not exceed 600. SMT patch processing quality can be judged by appearance inspection: 1. Components are missing; 2. 2. Whether the components are pasted incorrectly; 3. Whether there is short circuit; 4. There is no virtual welding; The first three kinds of good inspection, virtual welding reasons are relatively complex, more trouble to check, next for you to introduce.
1, the judgment of virtual welding
1. Use the special equipment of online tester for inspection. 2. Visual or AOI inspection. When it is found that the solder solder solder is too little solder infiltration, or the solder joint in the middle, or the solder surface is convex ball, or solder and SMD do not melt, it is necessary to pay attention to, even a slight phenomenon will cause hidden trouble, should immediately determine whether there is a batch of virtual welding problem. 3. The method of judgment is to see whether more PCB solder joints at the same position have problems, such as individual PCB problems, may be the solder paste is scratched, pin deformation and other reasons, such as in many PCB problems at the same position, this is likely to be caused by bad components or problems with the pad.
2. Causes and solutions of virtual welding
1. The design of welding pad is defective. The existence of through-hole welding pad is a major defect of PCB design, less than all must not be used, do not use, through hole will cause solder loss resulting in solder shortage; Pad spacing, area also need to match the standard, otherwise should be corrected as soon as possible design.
2. PCB board has oxidation phenomenon, that is, the welding disc is not bright. If there is oxidation, you can use an eraser to remove the oxide layer, so that its bright return. PCB board damp, if suspected can be placed in the drying oven drying. PCB board has oil stains, sweat stains and other pollution, at this time to clean with anhydrous ethanol.
3. PCB printed with solder paste will be scraped and rubbed, which will reduce the amount of solder paste on the relevant pad and make solder insufficient. It should be made up in time. The method of filling can be dispensed with a little or a bamboo skewer.
4. SMD (table sticker components) quality is poor, expired, oxidation, deformation, resulting in virtual welding. This is a common reason. When buying components, be sure to see if there is oxidation, and buy back to use in a timely manner. Similarly, oxidized solder paste should not be used. The above is about how to judge the quality of SMT processing. If you have PCB products need proofing, SMT patch processing, PCBA OEM, please contact kingford.