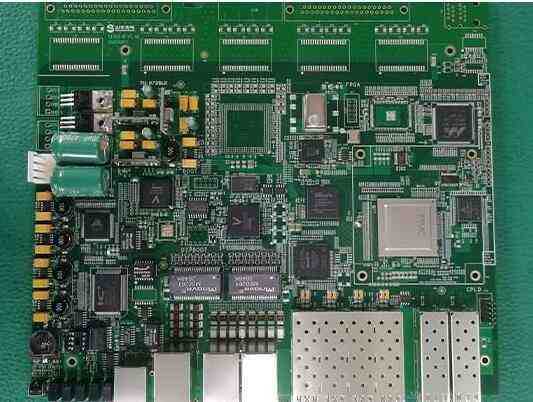
1.In the production process of patch processing, there will be many problems that we pay special attention to, especially the safety protection questions touched in the SMT processing and production process. So as long as the production line of SMT processing to ensure the health of the workers, we can ensure that the production of SMT processing will not be affected. In this respect, if the electronics factory attaches great importance to these details, it can show the humanized care of the manufacturers, so this is also a way to retain employees. In SMT processing and production will touch many power supply questions, so we should pay attention to the SMT patch processing and production of safety protection operations. If the power line is exposed to the outside, there may be leakage, so there may be electric shock, affecting the health of workers. If it is said that once we touch the power line, then it may cause serious damage to the body of the workers.
The damage to the human body is very serious, usually the light will cause workers to lose their intuition, the heavy will cause disability or death, the consequences are very serious. Therefore, we should regularly check whether the power supply of SMT patch processing and production line has done a good job of various safety protection, once there is any doubt, we should correct it in time. Other also do special training of power supply protection, if the operation if the risk of power supply, it is necessary to immediately respond to the situation of the relevant personnel, in order to immediately deal with this question, in order to the deterioration of the organizational situation at the source. So if you say that the situation of power supply risk can not be self-righteous start to repair the power supply, so as not to attack the risk situation.
In the SMT patch processing and production process, it is necessary to pay attention to the fact that this machine is a high-speed machine when using machine patch in the patch processing program. Because of the high-speed operation, there is a need for many power sources to ensure the operation of all production lines. So there are many sharp edges in these power sources. These edges are some risk items, so it is necessary to ensure that all kinds of protection methods are done in these machines. In addition, in these coerce to the local workers body is to pay attention to the protection of the guardrail. If someone accidentally touched the damage will be immediately closed all SMT plus operation switch. In order to avoid the onset of this situation, usually when cleaning the machine wheel to wear special gloves to avoid being cut.
In the SMT patch processing and production process, we should pay attention to fire safety. Because there may be some fireworks during welding, we should pay special attention to this question. There must be no flammable products around the production line, if if ignited, it is necessary to immediately suspend the SMT production line. In the patch processing and production, we should pay attention to anti-static, in the SMT processing and production line electrostatic protection must restrain the accumulation of charge, but also adopt some measures to effect the charge that has occurred. Therefore, whether in the SMT processing and production process or not yet produced, we should pay attention to anti-static maintenance operations.
2.How to replace chip components for SMT machining
kingfordSMT SMT factory, can provide minimum package 0201 components SMT processing services. Next, we will introduce how to replace chip components for SMT processing and repair. In SMT processing and repair, chip components are one of the most exposed materials, and it is often necessary to replace chip components during SMT processing. Replacing chip components looks very simple, but there are still a lot of tips in it. If you do not pay attention to it, it is still very troublesome to operate. In order to ensure the quality of products, we need to replace chip components in strict accordance with the relevant requirements. Before replacing chip components in SMT machining and repair, we need to prepare an electric iron with ground wire connected and temperature controllable. The width of the iron head and the size of the metal face of the chip element should be consistent, the iron needs to be heated to 320 degrees Celsius.
In addition to the electric iron, also need to prepare tweezers, tin strip, fine low temperature rosin, welding wire and other basic tools. When replacing the chip components, you can directly put the heated iron head on the upper surface of the damaged components, and then wait until the solder on both sides of the chip components and the adhesive below the components are melted by high temperature, you can use tweezers to directly remove the damaged lady components. After the damaged component is removed, the remaining tin on the circuit board should be scalded with a tin strip, and then the adhesive and other stains on the original pad should be scrubbed with alcohol. PCBA processing, usually only to the circuit board on one side of the plate hot solder; Then the element is placed on the pad with tweezers. In order to quickly heat the tin on the pad, it is necessary to place the solder contact plate element on the metal end, but it needs to be paid special attention to that the iron head must not directly contact the element.
Generally, as long as one end of the newly changed flake element is fixed, the other end can be welded. It is necessary to heat the welding pad on the circuit board and add appropriate amount of solder, so that the welding pad and the end face of the element form a bright arc. It should be noted that the amount of solder can not be put too much, otherwise the molten solder will flow to the element below causing a short circuit, and the other end of the welding, the rest of the end can only let the molten tin into the metal end of the element, can not let the iron head touch the element, and then complete the whole replacement process.