Шэньчжэнь, район Баоань, улица Фуюн, улица Фуцяо, район 3, промышленный парк Лонгхуй 6
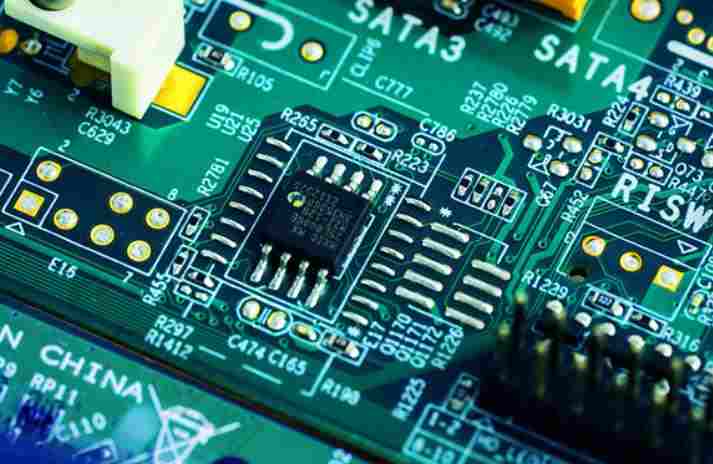
SMT patch checks for short circuit to improve product quality
Short circuit is a relatively common processing defect in SMT patch during manual welding To achieve the same effect as manual SMT patch and machine pasting, short circuit is a problem that must be solved Short circuit PCBA cannot be used There are many ways to handle SMT patches The following is about SMT patch processing
1. In order to form a good habit of manual welding operation, use a multimeter to check whether the key circuit is short circuited. Each time the SMT IC is manually operated, a multimeter is required to measure whether the power supply and ground are short circuited.
2 Turn on the short circuit network PCB diagram on the, find the place on the circuit board that is most likely to be short circuited, and pay attention to the internal short circuit of the IC
3. If a short circuit occurs in the same batch during SMT chip processing, you can take a board to cut the circuit, and then power on each part to check the short circuit.
5. If there is a BGA chip, because all the solder joints are covered by the chip and cannot be seen, and it is a multilayer board (more than 4 layers), the power supply of each chip is separated in design and connected with magnetic beads or 0 ohm resistance., In this way, when there is a short circuit between the power supply and the ground, the magnetic bead detection is disconnected, and it is easy to locate a chip.
6. When welding small sizes, be careful with SMT patch processing surface mounting capacitors (103 or 104), which are in large quantities and are easy to cause short circuit between power supply and ground
How to improve the quality of SMT products?
SMD processing technology has been widely used in the electronic industry. The product quality of SMT processing is related to the actual effect of product molding, and is also a test of enterprise strength. The overall goal of each SMT factory is to improve the quality of SMT products.
1. Select enterprise scientific and technological personnel. Establish a product quality organization network within the enterprise to provide timely and accurate product quality response, select product quality personnel to act as product quality inspectors on the production line, and the product quality department is still responsible for management; Avoid other factors interfering with the determination of product quality.
2. Ensure the accuracy of equipment and equipment testing and maintenance. Inspect and maintain the product through multimeter, anti-static wrist, soldering iron, ict and other necessary equipment. In this case, the product quality of the equipment itself will directly affect the quality of the products produced. In order to ensure the reliability of the equipment, timely inspection and measurement shall be carried out according to the provisions. Jingbang Technology has such high-precision testing equipment as AOI detector, X-ray detector, lcr bridge detector, 60 times digital electron microscope, etc. under the Yali line to ensure the quality standard of each product.
3. Formulate product quality regulations. The Quality Department shall formulate necessary rules and regulations related to product quality and department responsibility system, limit avoidable quality accidents through laws and regulations, give clear rewards and punishments, and participate in product quality assessment by economic means; And set up a monthly enterprise quality award.
4. Implementation of management measures. For quality control, in addition to strictly controlling the quality of the production process, the inspector shall also take measures to conduct sampling inspection (or overall inspection) on the purchased parts before they are put into storage, determine that the percent of pass does not meet the requirements of national standards, and return the goods. The inspection results shall be recorded in writing.
5. Set product quality process control points In order to ensure smt patch processing, strengthen the quality inspection of each process and monitor its operation status Therefore, it is particularly important to establish product quality control points after some key processes, so as to timely find and correct quality problems in subsequent processes and prevent unqualified products from entering the next process
Short circuit is a relatively common processing defect in SMT patch during manual welding To achieve the same effect as manual SMT patch and machine pasting, short circuit is a problem that must be solved Short circuit PCBA cannot be used There are many ways to handle SMT patches The following is about SMT patch processing
1. In order to form a good habit of manual welding operation, use a multimeter to check whether the key circuit is short circuited. Each time the SMT IC is manually operated, a multimeter is required to measure whether the power supply and ground are short circuited.
2 Turn on the short circuit network PCB diagram on the, find the place on the circuit board that is most likely to be short circuited, and pay attention to the internal short circuit of the IC
3. If a short circuit occurs in the same batch during SMT chip processing, you can take a board to cut the circuit, and then power on each part to check the short circuit.
5. If there is a BGA chip, because all the solder joints are covered by the chip and cannot be seen, and it is a multilayer board (more than 4 layers), the power supply of each chip is separated in design and connected with magnetic beads or 0 ohm resistance., In this way, when there is a short circuit between the power supply and the ground, the magnetic bead detection is disconnected, and it is easy to locate a chip.
6. When welding small sizes, be careful with SMT patch processing surface mounting capacitors (103 or 104), which are in large quantities and are easy to cause short circuit between power supply and ground
How to improve the quality of SMT products?
SMD processing technology has been widely used in the electronic industry. The product quality of SMT processing is related to the actual effect of product molding, and is also a test of enterprise strength. The overall goal of each SMT factory is to improve the quality of SMT products.
1. Select enterprise scientific and technological personnel. Establish a product quality organization network within the enterprise to provide timely and accurate product quality response, select product quality personnel to act as product quality inspectors on the production line, and the product quality department is still responsible for management; Avoid other factors interfering with the determination of product quality.
2. Ensure the accuracy of equipment and equipment testing and maintenance. Inspect and maintain the product through multimeter, anti-static wrist, soldering iron, ict and other necessary equipment. In this case, the product quality of the equipment itself will directly affect the quality of the products produced. In order to ensure the reliability of the equipment, timely inspection and measurement shall be carried out according to the provisions. Jingbang Technology has such high-precision testing equipment as AOI detector, X-ray detector, lcr bridge detector, 60 times digital electron microscope, etc. under the Yali line to ensure the quality standard of each product.
3. Formulate product quality regulations. The Quality Department shall formulate necessary rules and regulations related to product quality and department responsibility system, limit avoidable quality accidents through laws and regulations, give clear rewards and punishments, and participate in product quality assessment by economic means; And set up a monthly enterprise quality award.
4. Implementation of management measures. For quality control, in addition to strictly controlling the quality of the production process, the inspector shall also take measures to conduct sampling inspection (or overall inspection) on the purchased parts before they are put into storage, determine that the percent of pass does not meet the requirements of national standards, and return the goods. The inspection results shall be recorded in writing.
5. Set product quality process control points In order to ensure smt patch processing, strengthen the quality inspection of each process and monitor its operation status Therefore, it is particularly important to establish product quality control points after some key processes, so as to timely find and correct quality problems in subsequent processes and prevent unqualified products from entering the next process
Достаточно загрузить файлы Gerber, BOM и проектные документы, и команда KINGFORD предоставит полное предложение в течение 24 часов.