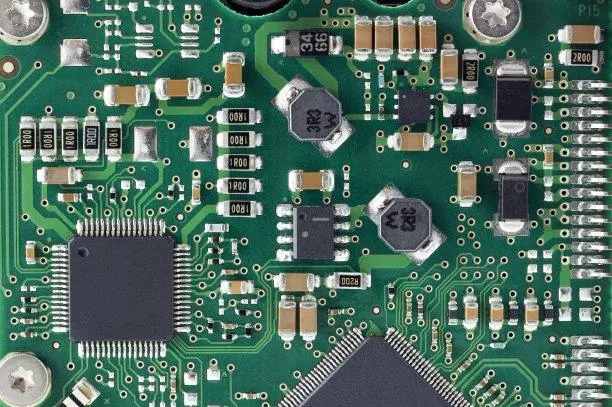
Quality assurance affects your PCB assembly in many ways
PCB is everywhere. From mobile phones to Bluetooth speakers, they have constituted the vast majority of electronic products in people's daily life. As a result, when PCB design becomes more complex and layout is smaller, an effective quality assurance plan is imperative.
Quality assurance is defined as the avoidance of problems and the prevention of errors, defects and defects in manufactured products. In order to achieve this successfully, this quality assurance must be integrated in the entire PCB Assembly process. Lack of quality assurance will make the company face serious mistakes, human errors, manufacturing defects, money waste and unsafe products.
risk management
Risk management is to discover problems before they actually occur. Steps should be taken before manufacturing begins to identify problems that may lead to additional costs, missed deadlines, and product failures. Risk management assessment shall include all contents from design inspection to ensuring that all PCB components can be purchased correctly, as well as methods for predicting financial risks and assessing the minimization of the impact of any unavoidable obstacles that may arise.
Provide DFM
When your ECM uses DFM analysis and design as part of its quality assurance program, it can be very valuable. DFM will determine whether your design meets the manufacturing process requirements of the actual production of printed circuit boards. Early discovery of differences can provide solutions to successfully produce high-quality PCBs.
quality certification
Quality certification shows that you are working with companies that take risk reduction and quality improvement seriously. Compliance with ISO, AS9100 and ITAR indicates that you are working with manufacturers that will protect your products. Certification also indicates that the manufacturer has purchased the parts carefully to ensure that forged parts will not enter your product.
Staff Engineer
When it comes to PCB assembly, the more eyes you have, the better. Needless to say, working with manufacturing partners and engineers is very valuable for staff to troubleshoot. When experienced engineers participate in this process, they can easily identify any potential problems with your product. This will optimize your production process and save money. After you hand over the product to the customer, you can also minimize the risk of repair.
Testing and prototyping
Testing and prototyping are essential steps in the quality assurance process. This is the only real way to understand how your design works. A small amount of debugging on the equipment allows engineers to test the function of the product and make necessary adjustments. Doing so early can save time and money. It also gives you better control over the quality of the final product.
Undetected defects in PCB manufacturing process will not only directly affect the single PCB that finds them, but also endanger the entire PCB assembly process. This is why efficiency and quality are improved at every step of the design and manufacturing process. We have strict quality assurance system at all levels, and strive to make your products reach the best state. The PCB design and processing factory explains that quality assurance affects your PCB assembly in many ways, and an effective quality assurance plan is imperative.