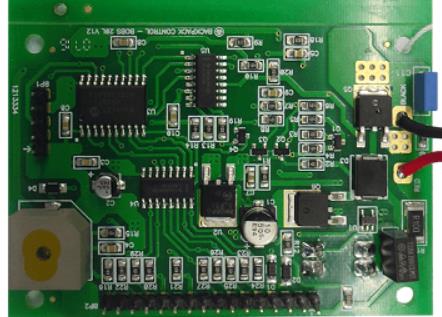
Production Process of SMT Chip Wire Mesh
The mold is also a SMT model (SMT mold), which is a special mold for SMT processing Its main function is to help solder paste deposition; The purpose is to transfer the exact amount of solder paste to the corresponding position of the empty PCB With the development of Surface Mount Technology, SMT wire mesh is also widely used in glue technology, such as red glue The production process of SMT steel mesh can be divided into three types: chemical cutting, laser cutting and electroforming
1. The chemical etching model is chemically etched to form a template opening, which is suitable for making brass and stainless steel templates. Specific characteristics are as follows:
1. The opening is bowl shaped, and the solder paste release efficiency is poor.
2. It can only be used for printing components with spacing values greater than 20mil, such as 25-50mil;
3. The template thickness is 0.1~0.5mm;
4. The size error of the hole is 1mil (position error);
The price is cheaper than laser cutting and electroforming.
SMT patch template etching process
2. The last hole of the laser cutting template adopts laser cutting, which has the following characteristics:
1. The opening is naturally trapezoidal, and the upper opening is usually 1~5mil larger than the lower opening, which is conducive to the release of solder paste;
2. The aperture error is 0.3 ~ 0.5mil, and the positioning accuracy is less than 0.12mil;
3. The price is more expensive than chemical etching and cheaper than electroforming;
4. The hole wall is not as smooth as the electroforming template; The thickness of the u5kemanzu template is. 12~0.3mm;
6. It is usually used for printing components with spacing values less than or equal to 20mil. Laser engraving process of SMT chip mold
3. The template of electroplating molding uses chemical method, but instead of etching the required figure on the metal plate, it directly electroplating the nickel leakage plate, that is, the additive method. It has the following characteristics:
1. The trapezoidal opening is naturally formed, and the hole wall is smooth, which is conducive to the release of solder paste;
2. The protective lip with an opening is naturally formed in the production process;
3. The template with a thickness of 2~12 mils can be made;
4. Good wear resistance and service life;
5. The price is expensive and the production cycle is long.
Electrified stencil engraving and engraving process
4. Compare the advantages and disadvantages of three carving methods. Template type. Etching templates. Laser template. Electroforming. Sample processing. Chemical etching. Laser cutting. Electroforming. Position accuracy. – 15mm–5mm–15mm。 The shape is 2~6 ℃, the hole wall is rough, no burr – 5mm, with fine burr – 5mm, the hole wall is smooth, no burr, and the service life can reach more than 300000 times, up to more than 400000 times
Other functions
1. Low production cost and fast production cycle;
2. Poor precision, unable to fully meet the requirements of fine printing
requirement
1. More accurate production;
2. Long production time;
High cost;
3. The force between the alloy surface and the solder paste is smaller, and it is easier to peel off
The above is the explanation given by the editor of PCB circuit board company.
If you want to know more about PCBA, you can go to our company's home page to learn about it.
In addition, our company also sells various circuit boards,
High Frequency Circuit Board and SMT chip are waiting for your presence again.