Шэньчжэнь, район Баоань, улица Фуюн, улица Фуцяо, район 3, промышленный парк Лонгхуй 6
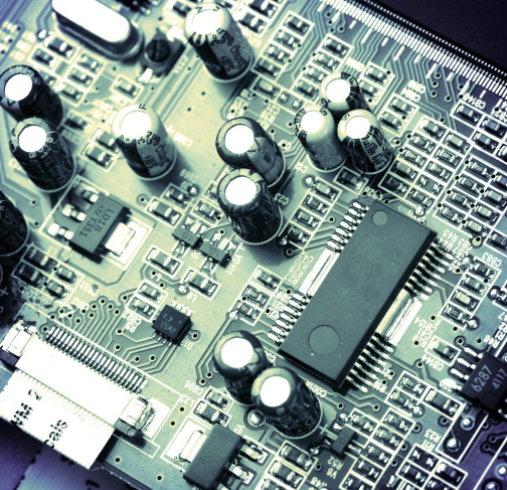
SMT solves printing problems and lead-free soldering
In the electronic industry, SMT chip processing is mainly processed by SMT, and many failures will occur in the use process According to statistics, 60% of the defects are caused by solder paste printing Therefore, to ensure the high quality printing of SMT is an important prerequisite to ensure its processing quality The following describes how to solve printing errors during the repair process
5 * 1. There is no gap between the template and PCB printing method, that is, "touch printing". High stability requirements for various structures, suitable for printing high-precision solder paste. The metal plate is in good contact with the printed board and can be separated from the PCB after printing. This method has high printing accuracy, and is especially suitable for fine and super macro printing.
1. Printing speed.
The solder paste rolls forward when scraping. Suitable for screen printing and fast printing.
This rebound can also prevent solder paste leakage. In addition, the paste cannot be rolled on the network, resulting in clear solder paste and too fast printing speed.
The dimension of is 10 * 20 mm/s.
2. Printing method:
3. Scraper type:
The scraper is divided into plastic scraper and steel scraper. For integrated circuits with a distance less than 0.5mm, steel solder paste can be used to form solder paste after printing.
Scraper adjustment.
In the welding process, the scraper working point is printed along the 45 ° direction, which can significantly improve the non-uniformity of the opening and reduce the damage of the steel plate and the opening. The pressure of the scraper is usually 30N/mm.
SMT wafer processing
2. During installation, select IC installation height with spacing no more than 0.5mm, 0mm or 0~-0.1mm to avoid solder paste falling off due to low installation height and short circuit during reflow.
Remelt welding.
The main reasons for assembly failure caused by reflow welding are as follows:
First, the temperature rises too fast;
B. High temperature and overheating;
The heating speed of solder paste is faster than that of circuit board;
D. Excessive water.
This, when determining the remelting welding process parameters, all factors shall be fully considered to ensure that there is no problem in welding quality before large-scale assembly.
Introduction to SMT processing lead-free welding and maintenance
The introduction of lead-free chip assembly has always been the challenge of the first assembly, because it will face more challenges when processing and rework are needed. The maintenance of PCBA in lead-free environment will have higher cost, quality details, time and repeatability problems, but due to lead-free requirements, these problems need attention. Due to the need for lead-free processes:
1. Train lead-free assembly, maintenance and inspection operators and evaluate time and cost.
2. The prices of lead-free solders are higher than those of traditional solders, such as lead-free wires, rods and core solders.
3. The processing temperature of lead-free components (about 30-35 ° C) requires higher precision and precision.
4. Lead free technology also needs to study and plan SMT processing plants to establish correct PCBA repair process.
First of all, it is necessary to analyze the technical personnel according to the characteristics of lead-free process. To define rework standards, whether standard solder or lead-free solder is required, the process is the same, and the required steps are:
Define and execute an accurate thermal profile.
2. The faulty component must be removed.
3. Clean all rust or solder residues on site and prepare new parts.
4. Replace parts with new solder and flux and reflow.
5. Thoroughly check the rework.
In a lead-free environment, accurate and reliable rework is more difficult because PCBA and the parts closest to maintenance must undergo multiple high-temperature cycles. In order to protect the stability of the circuit board, the preheating temperature should be set within the range not higher than the glass transition temperature of the PCB data.
The subsequent steps involved in the rework process vary depending on the lead-free requirements The difference between standard and lead-free brings many challenges, which can only be solved by introducing new or changed technologies, including stricter and more accurate thermal curves, as well as in the whole PCBA maintenance process With this kind of pipe, many expensive problems caused by different heat distribution can be avoided
In the electronic industry, SMT chip processing is mainly processed by SMT, and many failures will occur in the use process According to statistics, 60% of the defects are caused by solder paste printing Therefore, to ensure the high quality printing of SMT is an important prerequisite to ensure its processing quality The following describes how to solve printing errors during the repair process
5 * 1. There is no gap between the template and PCB printing method, that is, "touch printing". High stability requirements for various structures, suitable for printing high-precision solder paste. The metal plate is in good contact with the printed board and can be separated from the PCB after printing. This method has high printing accuracy, and is especially suitable for fine and super macro printing.
1. Printing speed.
The solder paste rolls forward when scraping. Suitable for screen printing and fast printing.
This rebound can also prevent solder paste leakage. In addition, the paste cannot be rolled on the network, resulting in clear solder paste and too fast printing speed.
The dimension of is 10 * 20 mm/s.
2. Printing method:
3. Scraper type:
The scraper is divided into plastic scraper and steel scraper. For integrated circuits with a distance less than 0.5mm, steel solder paste can be used to form solder paste after printing.
Scraper adjustment.
In the welding process, the scraper working point is printed along the 45 ° direction, which can significantly improve the non-uniformity of the opening and reduce the damage of the steel plate and the opening. The pressure of the scraper is usually 30N/mm.
SMT wafer processing
2. During installation, select IC installation height with spacing no more than 0.5mm, 0mm or 0~-0.1mm to avoid solder paste falling off due to low installation height and short circuit during reflow.
Remelt welding.
The main reasons for assembly failure caused by reflow welding are as follows:
First, the temperature rises too fast;
B. High temperature and overheating;
The heating speed of solder paste is faster than that of circuit board;
D. Excessive water.
This, when determining the remelting welding process parameters, all factors shall be fully considered to ensure that there is no problem in welding quality before large-scale assembly.
Introduction to SMT processing lead-free welding and maintenance
The introduction of lead-free chip assembly has always been the challenge of the first assembly, because it will face more challenges when processing and rework are needed. The maintenance of PCBA in lead-free environment will have higher cost, quality details, time and repeatability problems, but due to lead-free requirements, these problems need attention. Due to the need for lead-free processes:
1. Train lead-free assembly, maintenance and inspection operators and evaluate time and cost.
2. The prices of lead-free solders are higher than those of traditional solders, such as lead-free wires, rods and core solders.
3. The processing temperature of lead-free components (about 30-35 ° C) requires higher precision and precision.
4. Lead free technology also needs to study and plan SMT processing plants to establish correct PCBA repair process.
First of all, it is necessary to analyze the technical personnel according to the characteristics of lead-free process. To define rework standards, whether standard solder or lead-free solder is required, the process is the same, and the required steps are:
Define and execute an accurate thermal profile.
2. The faulty component must be removed.
3. Clean all rust or solder residues on site and prepare new parts.
4. Replace parts with new solder and flux and reflow.
5. Thoroughly check the rework.
In a lead-free environment, accurate and reliable rework is more difficult because PCBA and the parts closest to maintenance must undergo multiple high-temperature cycles. In order to protect the stability of the circuit board, the preheating temperature should be set within the range not higher than the glass transition temperature of the PCB data.
The subsequent steps involved in the rework process vary depending on the lead-free requirements The difference between standard and lead-free brings many challenges, which can only be solved by introducing new or changed technologies, including stricter and more accurate thermal curves, as well as in the whole PCBA maintenance process With this kind of pipe, many expensive problems caused by different heat distribution can be avoided
Достаточно загрузить файлы Gerber, BOM и проектные документы, и команда KINGFORD предоставит полное предложение в течение 24 часов.