Шэньчжэнь, район Баоань, улица Фуюн, улица Фуцяо, район 3, промышленный парк Лонгхуй 6
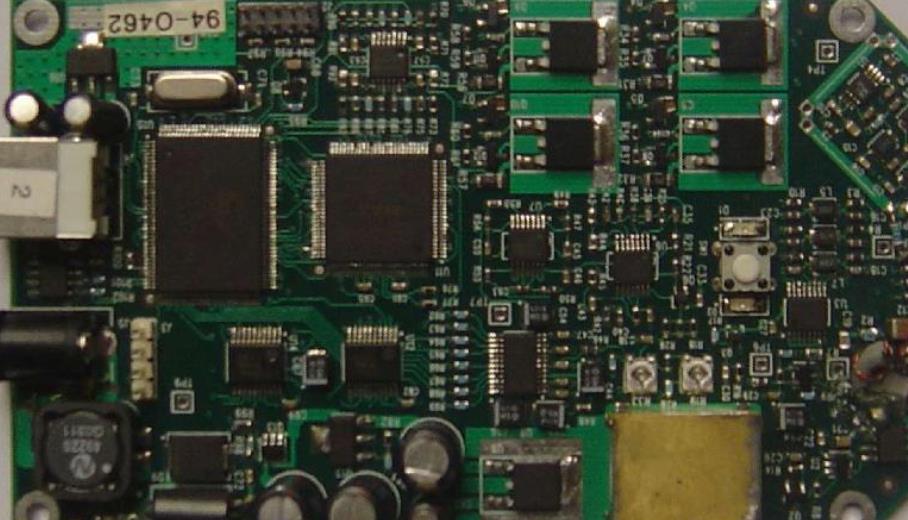
SMT chip programming operation and quality inspection process
Place the programming operation to open the mounting machine
1. Edit the optimized product program on the mounter
1. Call up the optimized program.
2. Make PCB mark and partial Mak image.
3. Make an image of the component that is not imaged and register it in the image library.
4. Register unregistered components in the component library.
5. For the multi tube vibrating feeder with unreasonable discharge, it shall be redistributed according to the length of the device body, and the devices with relatively short length of the device body shall be arranged on the same frame as far as possible: grasp the material station, and try not to have an idle material station in the middle, so as to shorten the distance between the picking parts.
6. Change the multi pin and narrow spacing equipment with large contour in the program, such as QFP with more than 160 pins, large size PLCC, BGA and long slots, to single pickup, which can improve the placement. Installation accuracy.
7. Save to the disk, check whether there is an error message, and modify the program according to the error message until there is no error message after saving.
2. Proofread check and backup patches
1. According to the PCBA process file, check whether the component name, label, and model and specification of each step in the program are correct, and correct the wrong part according to the process file
2. Check whether the components on each feeder station of the mounter are consistent with the picking program table.
3. Use the main camera on the mounter to check whether the X and Y coordinates of the components in each step are consistent with the component center on the PCB. Check the corner according to the element location diagram in the process file Whether it is correct and correct the error. (If this step is not performed, it can be corrected according to the actual placement deviation after placing the first SMT)
4. Copy the correct product program to the backup USB flash drive and save it.
6. Production can only be carried out after checking and checking.
Main quality inspection process of SMT chip processing products
In order to ensure the yield of PCBA casting materials, Kunshan SMT Factory must inspect the processed electronic products during SMT processing. The main quality inspection process problems of the patch processing products of Kunshan Patch Factory.
1. The surface of FPC board shall not affect the appearance of solder paste, foreign matters and traces. The bonding position of the parts treated with smt chip shall be free of rosin or flux and foreign matters that affect the appearance and soldering tin. There shall be no drawing or tipping when forming the lower tin point of the part.
2. Component installation process. During smt chip processing, the components shall be placed in a neat and central position without offset or skew; The type and specification of components placed in smt chip processing shall be correct; Components processed by smt patch can not lack stickers or have sticker errors in the village; Pay attention to components that cannot be reversed during smt chip processing; In the process of smt chip processing, the patch equipment with polarity requirements must follow the polarity instructions.
3. There shall be no obvious deviation between the positions of solder paste in the printing process, and the solder paste and soldering tin shall not be affected. If the printing solder paste is moderate and can be pasted well, there will still be no insufficient tin or excessive solder paste. The solder paste is well formed without tin connection and unevenness.
4. There is no crack and notch at the bottom of the component appearance, and there is no through hole on the surface, copper foil, wire and board The FPC is parallel to the plane without deformation The recognition information characters of SMT chip processing are clear, offset printing, reverse printing, offset printing, double shading, etc The Flexible circuit board on the outer surface of shall be free from bubble expansion The aperture size shall meet the design requirements
Place the programming operation to open the mounting machine
1. Edit the optimized product program on the mounter
1. Call up the optimized program.
2. Make PCB mark and partial Mak image.
3. Make an image of the component that is not imaged and register it in the image library.
4. Register unregistered components in the component library.
5. For the multi tube vibrating feeder with unreasonable discharge, it shall be redistributed according to the length of the device body, and the devices with relatively short length of the device body shall be arranged on the same frame as far as possible: grasp the material station, and try not to have an idle material station in the middle, so as to shorten the distance between the picking parts.
6. Change the multi pin and narrow spacing equipment with large contour in the program, such as QFP with more than 160 pins, large size PLCC, BGA and long slots, to single pickup, which can improve the placement. Installation accuracy.
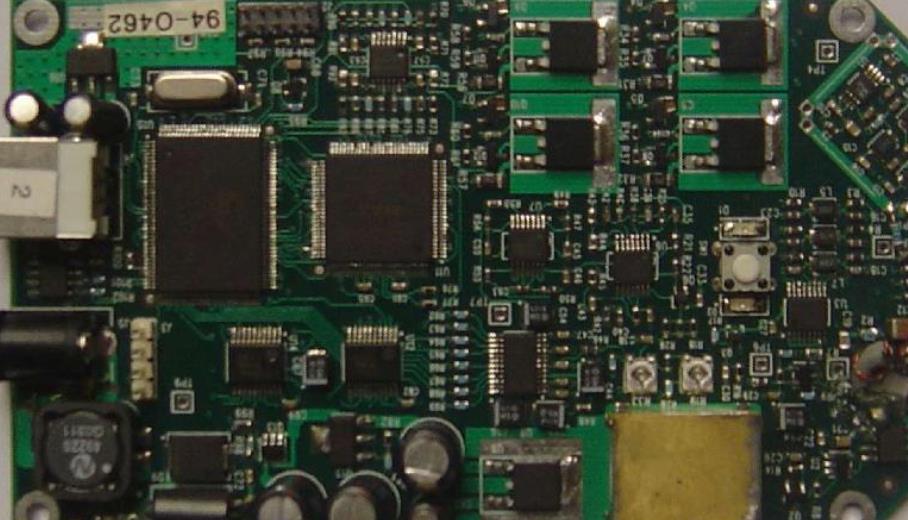
2. Proofread check and backup patches
1. According to the PCBA process file, check whether the component name, label, and model and specification of each step in the program are correct, and correct the wrong part according to the process file
2. Check whether the components on each feeder station of the mounter are consistent with the picking program table.
3. Use the main camera on the mounter to check whether the X and Y coordinates of the components in each step are consistent with the component center on the PCB. Check the corner according to the element location diagram in the process file Whether it is correct and correct the error. (If this step is not performed, it can be corrected according to the actual placement deviation after placing the first SMT)
4. Copy the correct product program to the backup USB flash drive and save it.
6. Production can only be carried out after checking and checking.
Main quality inspection process of SMT chip processing products
In order to ensure the yield of PCBA casting materials, Kunshan SMT Factory must inspect the processed electronic products during SMT processing. The main quality inspection process problems of the patch processing products of Kunshan Patch Factory.
1. The surface of FPC board shall not affect the appearance of solder paste, foreign matters and traces. The bonding position of the parts treated with smt chip shall be free of rosin or flux and foreign matters that affect the appearance and soldering tin. There shall be no drawing or tipping when forming the lower tin point of the part.
2. Component installation process. During smt chip processing, the components shall be placed in a neat and central position without offset or skew; The type and specification of components placed in smt chip processing shall be correct; Components processed by smt patch can not lack stickers or have sticker errors in the village; Pay attention to components that cannot be reversed during smt chip processing; In the process of smt chip processing, the patch equipment with polarity requirements must follow the polarity instructions.
3. There shall be no obvious deviation between the positions of solder paste in the printing process, and the solder paste and soldering tin shall not be affected. If the printing solder paste is moderate and can be pasted well, there will still be no insufficient tin or excessive solder paste. The solder paste is well formed without tin connection and unevenness.
4. There is no crack and notch at the bottom of the component appearance, and there is no through hole on the surface, copper foil, wire and board The FPC is parallel to the plane without deformation The recognition information characters of SMT chip processing are clear, offset printing, reverse printing, offset printing, double shading, etc The Flexible circuit board on the outer surface of shall be free from bubble expansion The aperture size shall meet the design requirements
Достаточно загрузить файлы Gerber, BOM и проектные документы, и команда KINGFORD предоставит полное предложение в течение 24 часов.